Wear-resistant and heat-resistant porcelain and processing technology
A processing technology and heat-resistant technology, applied in the field of porcelain processing, can solve the problems of inability to balance wear resistance and heat resistance, and achieve the effect of good wear resistance and good heat resistance.
- Summary
- Abstract
- Description
- Claims
- Application Information
AI Technical Summary
Problems solved by technology
Method used
Image
Examples
Embodiment 1
[0030] A processing technology of wear-resistant and heat-resistant porcelain, the specific steps are as follows:
[0031] (1) first add zirconium nitrate, tantalum acetate, and molybdenum nitrate to the first part of water, stir until completely dissolved, to obtain a mixed solution, then add a 5% ammonia solution by mass concentration to the mixed solution, precipitate, and age to obtain a gel, and then Add the gel into the second part of water, continue to add polyethylene glycol 800 and sodium carboxymethyl cellulose, ball-mill and mix to obtain a slurry, spray-dried, and calcined to obtain a premixed powder;
[0032] (2) Then use feldspar, mica rock, ball clay, sepiolite, premixed powder as raw materials to make billets, and then use spodumene, mica rock, wollastonite, purple wood joint soil, red shale , Diopside, premixed powder as raw materials to make glaze;
[0033] (3) Finally, the blank is made into a blank, bisque fired to obtain a blank, treated with ozone, and t...
Embodiment 2
[0045] A processing technology of wear-resistant and heat-resistant porcelain, the specific steps are as follows:
[0046] (1) first add zirconium nitrate, tantalum acetate and molybdenum nitrate to the first part of water, stir until completely dissolved to obtain a mixed solution, then add a 7% aqueous ammonia solution in mass concentration to the mixed solution, precipitate and age to obtain a gel, then Add the gel into the second part of water, continue to add polyethylene glycol 800 and sodium carboxymethyl cellulose, ball-mill and mix to obtain a slurry, spray-dried, and calcined to obtain a premixed powder;
[0047] (2) Then use feldspar, mica rock, ball clay, sepiolite, premixed powder as raw materials to make billets, and then use spodumene, mica rock, wollastonite, purple wood joint soil, red shale , Diopside, premixed powder as raw materials to make glaze;
[0048] (3) Finally, the blank is made into a blank, bisque fired to obtain a blank, treated with ozone, and ...
Embodiment 3
[0060] A processing technology of wear-resistant and heat-resistant porcelain, the specific steps are as follows:
[0061] (1) first add zirconium nitrate, tantalum acetate, and molybdenum nitrate to the first part of water, stir until completely dissolved, to obtain a mixed solution, then add a 6% aqueous ammonia solution in a mass concentration to the mixed solution, precipitate, and age to obtain a gel, then Add the gel into the second part of water, continue to add polyethylene glycol 800 and sodium carboxymethyl cellulose, ball-mill and mix to obtain a slurry, spray-dried, and calcined to obtain a premixed powder;
[0062] (2) Then use feldspar, mica rock, ball clay, sepiolite, premixed powder as raw materials to make billets, and then use spodumene, mica rock, wollastonite, purple wood joint soil, red shale , Diopside, premixed powder as raw materials to make glaze;
[0063] (3) Finally, the blank is made into a blank, bisque fired to obtain a blank, treated with ozone,...
PUM
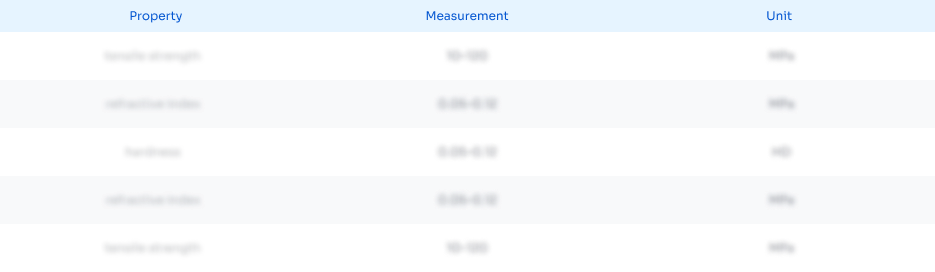
Abstract
Description
Claims
Application Information

- Generate Ideas
- Intellectual Property
- Life Sciences
- Materials
- Tech Scout
- Unparalleled Data Quality
- Higher Quality Content
- 60% Fewer Hallucinations
Browse by: Latest US Patents, China's latest patents, Technical Efficacy Thesaurus, Application Domain, Technology Topic, Popular Technical Reports.
© 2025 PatSnap. All rights reserved.Legal|Privacy policy|Modern Slavery Act Transparency Statement|Sitemap|About US| Contact US: help@patsnap.com