Three-body type composite casting wear-resistant lining plate and manufacturing method thereof
A composite casting and manufacturing method technology, applied in the field of steelmaking, can solve the problems of insufficiency of casting stress, hidden dangers left by installation and application, and the combination is not very smooth, so as to achieve both environmental benefits, outstanding comprehensive mechanical properties, improved casting performance and The effect of mechanical properties
- Summary
- Abstract
- Description
- Claims
- Application Information
AI Technical Summary
Problems solved by technology
Method used
Image
Examples
Embodiment 1
[0034] A three-body composite casting wear-resistant liner, including a back layer, a transition layer and a surface layer arranged in sequence, wherein the back layer is made of medium and low carbon steel, the filter layer is made of ferritic ductile iron, and the surface layer is made of Made of high chromium molybdenum anti-wear white cast iron, please refer to the attached structure diagram figure 1 .
[0035] The mass fraction percentage components of medium and low carbon steel are: C: 0.3~0.4w%, Si: ≤0.50w%, Mn: ≤0.90w%, S: ≤0.04w%, P: ≤0.04w%, the balance For Fe. The mechanical properties of medium and low carbon steel are shown in Table 1.
[0036] Table 1
[0037]
[0038] The mass fraction percentage components of high chromium molybdenum anti-wear white cast iron are: C: 2.0~3.0w%, Si: ≤1.0w%, Mn: 0.5~1.0w%, Cr: 13.0~18.0w%, Mo: 0.5 ~2.5w%, Ni: 0~1.0w%, Cu: 0~1.2w%, S: ≤0.06w%, P: ≤0.10w%, and the balance is Fe. The HCR after heat treatment is ≥ 55, and th...
Embodiment 2
[0044] A method for manufacturing a three-body composite cast wear-resistant liner, comprising the following steps:
[0045] S1. Casting: Three medium-frequency induction furnaces are used to smelt medium and low carbon steel, ferritic ductile iron and high-chromium-molybdenum anti-wear white cast iron respectively. The ferritic ductile iron is spheroidized and inoculated during smelting; After the smelting is completed, first pour medium and low carbon steel, solidify and crystallize, then pour ferritic ductile iron, solidify and crystallize, and finally pour high chromium molybdenum anti-wear white cast iron, solidify, crystallize and cool to obtain three Integral compound casting anti-wear lining blank material; ferritic nodular cast iron nodularization treatment process adopts the method of pouring into the bag, and inoculation treatment is carried out at the same time as nodularization treatment, which specifically includes the following steps:
[0046] S11, charging: acc...
PUM
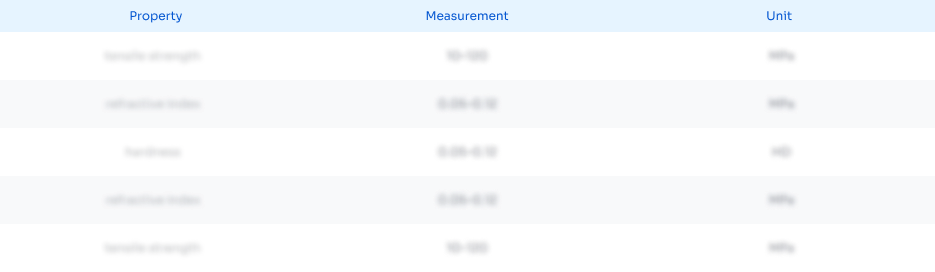
Abstract
Description
Claims
Application Information

- R&D
- Intellectual Property
- Life Sciences
- Materials
- Tech Scout
- Unparalleled Data Quality
- Higher Quality Content
- 60% Fewer Hallucinations
Browse by: Latest US Patents, China's latest patents, Technical Efficacy Thesaurus, Application Domain, Technology Topic, Popular Technical Reports.
© 2025 PatSnap. All rights reserved.Legal|Privacy policy|Modern Slavery Act Transparency Statement|Sitemap|About US| Contact US: help@patsnap.com