High-alumina magnesium alloy
A magnesium alloy and high-alumina technology, applied in the field of high-alumina-magnesium alloys, can solve the problems that the fluidity of alloys cannot be fully satisfied, and achieve the effects of improving fluidity, casting performance, and fluidity
- Summary
- Abstract
- Description
- Claims
- Application Information
AI Technical Summary
Problems solved by technology
Method used
Examples
Embodiment 1
[0020] Put 1063.2kg of magnesium ingots, 126.0kg of aluminum ingots, and 10.8kg of zinc ingots into the prepared clean crucible, add 18kg of RJ-2 bottom flux to melt, and sprinkle 6.0kg of RJ-4 covering agent to prevent burning during the process. Control it within 4 hours, and control the final temperature of the magnesium liquid at 670°C; after the melting is completed, blow air into the magnesium liquid, and use mechanical stirring, and add 18kg of RJ-6 refining agent and 11.0kg of manganese chloride for refining at the same time, and the time is controlled at 25min, the temperature is controlled at 680°C; continue to blow air into the magnesium liquid, and use mechanical stirring, and add 30kg of RJ-6 refining agent to refine again, and the last 5min to extract slag, the time is controlled at 45min, and the temperature is controlled at 730°C; after the end Let the flux and inclusions settle. The whole process is controlled at 60 minutes, and the final temperature is control...
Embodiment 2
[0023] Put 1059.6kg of magnesium ingots, 130.8kg of aluminum ingots, and 8.40kg of zinc ingots into the prepared clean crucible, add 24kg of RJ-2 base flux to melt, and sprinkle 4.8kg of RJ-5 covering agent to prevent burning during the process. Control at 5h, and the final temperature of magnesium liquid is controlled at 680°C; after melting, blow air into the magnesium liquid, and use mechanical stirring, and add 24kg of RJ-5 refining agent and 8.30kg of manganese chloride for refining at the same time, the time is controlled at 30min, the temperature is controlled at 710°C; continue to blow air into the magnesium liquid, and use mechanical stirring, and at the same time add 24kg of RJ-5 refining agent to refine again, and extract the slag for the last 5min, the time is controlled at 50min, and the temperature is controlled at 740°C; after the end Let the flux and inclusions settle. The whole process is controlled at 60 minutes, and the final temperature is controlled at 655°...
Embodiment 3
[0026] Put 1056.6kg of magnesium ingots, 136.2kg of aluminum ingots, and 5.40kg of zinc ingots into the prepared clean crucible, add 30kg of RJ-2 base flux to melt, and sprinkle 3.6kg of RJ-6 covering agent to prevent burning during the process. Controlled at 6h, and the final temperature of the magnesium liquid is controlled at 690°C; after the melting is completed, blow air into the magnesium liquid, and use mechanical stirring, and add 30kg of RJ-4 refining agent and 4.70kg of manganese chloride for refining at the same time, and the time is controlled at 35min, the temperature is controlled at 740°C; continue to blow air into the magnesium liquid, and use mechanical stirring, and at the same time add 18kg of RJ-4 refining agent to refine again, and the last 5min to extract the slag, the time is controlled at 55min, and the temperature is controlled at 750°C; after the end Let the flux and inclusions settle. The whole process is controlled at 60 minutes, and the final temper...
PUM
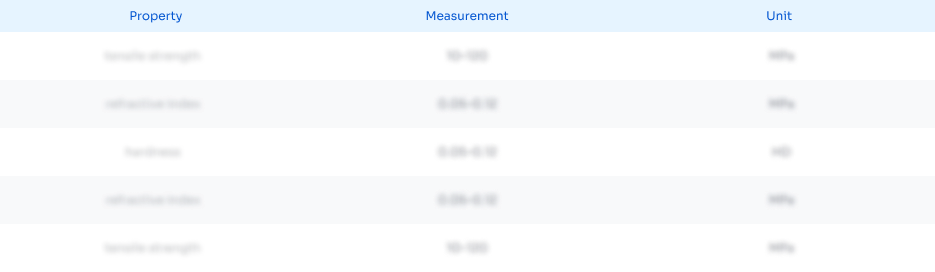
Abstract
Description
Claims
Application Information

- Generate Ideas
- Intellectual Property
- Life Sciences
- Materials
- Tech Scout
- Unparalleled Data Quality
- Higher Quality Content
- 60% Fewer Hallucinations
Browse by: Latest US Patents, China's latest patents, Technical Efficacy Thesaurus, Application Domain, Technology Topic, Popular Technical Reports.
© 2025 PatSnap. All rights reserved.Legal|Privacy policy|Modern Slavery Act Transparency Statement|Sitemap|About US| Contact US: help@patsnap.com