Intelligent identification and measurement method for defects of anti-corrosion layer
A technology of intelligent recognition and measurement method, applied in character and pattern recognition, optical testing flaws/defects, image data processing, etc. The effect of reliable defect identification and measurement, improved accuracy and improved work efficiency
- Summary
- Abstract
- Description
- Claims
- Application Information
AI Technical Summary
Problems solved by technology
Method used
Image
Examples
Embodiment 1
[0044] Embodiment 1 Coating Bubble Defect
[0045] Such as Figure 4 to Figure 6 As shown, this embodiment provides a method for intelligent identification and measurement of the anti-corrosion layer of the coating bubbling defect.
[0046] Firstly, the image acquisition of the defects of coating bubbles is carried out, and the following results are obtained: Figure 4 and Figure 6 The first original image in , and then grayscale processing is performed on the image to grayscale the coating image, so that the outline of the typical defect bubbles of the coating can be displayed. Then, according to the actual scale marked by the laser radar rangefinder, the number, size and density of the bubbles are automatically measured, and corresponding data reports are generated. According to the generated data report and grayscale image, compare it with the rating of coating defects in "GBT 30789.2-2014 Part 2: Evaluation of Blistering Grade", according to the standard evaluation pri...
Embodiment 2
[0048] Example 2 Coating Rusting Defects
[0049] Such as Figure 7 and Figure 8 As shown, this embodiment provides a method for intelligent identification and measurement of the anti-corrosion layer of coating rust defects.
[0050] Firstly, the image acquisition of the coating rust defect is obtained as follows: Figure 7 The first original image in the image, and then grayscale processing is performed on the image to remove the excess impurities other than rust on the surface of the coating rust defect image, and the rust on the coating surface is displayed in a more obvious dark color Then display the area of rusty features by means of color scale contrast enhancement, and extract rusty features; and generate basic parameters such as the number, density and area of rusty spots; generate corresponding data reports; according to the generated The data report and grayscale image are compared with the rating of coating defects in "GBT 30789.3-2014 Part 3: Evaluation of...
Embodiment 3
[0051] Example 3 Coating Cracking Defects
[0052] Such as Figure 9 and Figure 10 As shown, this embodiment provides a method for intelligent identification and measurement of anti-corrosion coating cracking defects.
[0053] Firstly, the image acquisition of the coating crack defect is obtained as follows: Figure 9 The first original image in the image, and then grayscale processing is performed on the image to clean up the dirty spots on the surface of the coating crack defect image, so that the image color is only the cracked crack color and the surface color of the coating, and then through The method of enhancing the contrast of the color scale makes the crack features more vividly displayed and extracts the crack features. And generate the corresponding data report; according to the generated data report and grayscale image, compare it with the coating defect rating in "GBT 30789.4-2014 Part 4: Evaluation of Cracking Grade", and automatically give the rating accord...
PUM
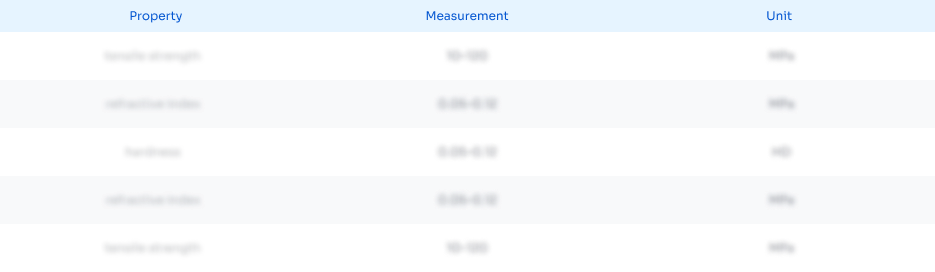
Abstract
Description
Claims
Application Information

- Generate Ideas
- Intellectual Property
- Life Sciences
- Materials
- Tech Scout
- Unparalleled Data Quality
- Higher Quality Content
- 60% Fewer Hallucinations
Browse by: Latest US Patents, China's latest patents, Technical Efficacy Thesaurus, Application Domain, Technology Topic, Popular Technical Reports.
© 2025 PatSnap. All rights reserved.Legal|Privacy policy|Modern Slavery Act Transparency Statement|Sitemap|About US| Contact US: help@patsnap.com