Crushing and drying all-in-one machine
An all-in-one machine and crushing chamber technology, applied in dryers, drying, drying gas layout, etc., can solve the problems of high cost, complex technology, low efficiency, etc. area effect
- Summary
- Abstract
- Description
- Claims
- Application Information
AI Technical Summary
Problems solved by technology
Method used
Image
Examples
Embodiment 1
[0042] The embodiment of the present invention discloses a crushing and drying integrated machine, which includes a casing 1, a spiral crushing knife 2, a hot air blower 3 and a motor 5. The hot air blower 3 is connected to one end of the casing 1, and the casing 1 is connected with the casing ring gear 11. The motor gear 51 on the motor 5 is meshed and connected. The shell 1 includes a crushing cavity shell 12, and the crushing cavity shell 12 is wrapped with a high-temperature resistant heat pipe 15. Crushing chamber, the spiral crushing knife 2 is installed in the crushing chamber, the high temperature resistant heat pipe 15 is wrapped to form a high temperature air cavity, one end of the high temperature air cavity is connected to the air outlet of the hot air blower 3, and the shell 1 is movably installed in the Rack 6.
[0043] refer to Figure 4 The shell 1 also includes a grinding chamber shell 13, one end of which is connected to the crushing chamber shell 12, and th...
Embodiment 2
[0050] Increase on the basis of embodiment 1:
[0051] The high temperature resistant heat pipe 15 is made of tungsten steel or tungsten-molybdenum alloy.
[0052] The steel slag is ground to about 100 mesh.
[0053] refer to Figure 5 , the crushing chamber casing 12 is provided with a feeding device 4, the feeding device 4 includes a feeding hopper 41 and a feeding casing 42, the feeding casing 42 is wrapped to form a feeding chamber, and the feeding chamber communicates with In the crushing chamber, the opening of the feeding hopper 41 faces upwards and communicates with the crushing chamber and the outside of the crushing chamber shell 12 .
[0054] The implementation mode of embodiment 2 is:
[0055] Increase on the basis of embodiment 1:
[0056] The feeding shell 42 is clamped on the crushing cavity shell 12, and the crushing cavity shell 12 rotates in the feeding shell 12, and the steel slag first enters the feeding cavity and then is slowly twisted into the crushi...
Embodiment 3
[0058] Increase on the basis of embodiment 2:
[0059] refer to Figure 1-4 A hot air valve 31 is provided at the place where the air outlet of the hot air blower 3 communicates with the high-temperature air cavity, and a valve switch 311 is provided on the hot air valve 31 .
[0060] The end of the casing 1 away from the hot air blower 3 is provided with a discharge port casing 14 , and a third discharge sieve plate 141 is provided at the connection between the discharge port casing 14 and the casing.
[0061] The end of the high-temperature-resistant heat pipe 15 away from the hot air blower 3 is provided with an air jet shell 151 .
[0062] refer to Figure 1-3 , the housing 1 is provided with a housing bearing seat 17 at the end away from the hot air blower 3, the housing 1 and the housing bearing housing 17 are connected by bearings, and an idler roller 16 is provided close to the outer surface of the housing 1 and close to the feeding device 4 , the idler roller 16 is...
PUM
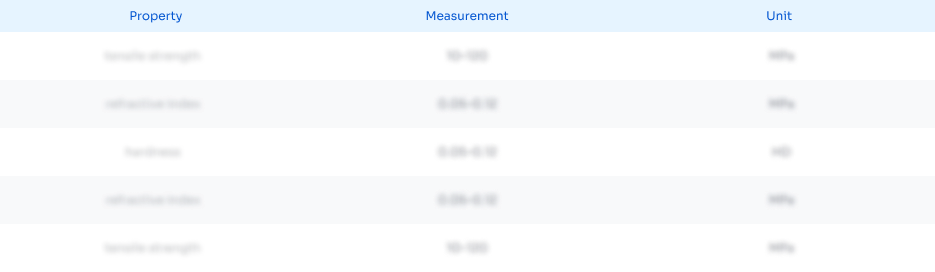
Abstract
Description
Claims
Application Information

- R&D
- Intellectual Property
- Life Sciences
- Materials
- Tech Scout
- Unparalleled Data Quality
- Higher Quality Content
- 60% Fewer Hallucinations
Browse by: Latest US Patents, China's latest patents, Technical Efficacy Thesaurus, Application Domain, Technology Topic, Popular Technical Reports.
© 2025 PatSnap. All rights reserved.Legal|Privacy policy|Modern Slavery Act Transparency Statement|Sitemap|About US| Contact US: help@patsnap.com