Method for preparing molybdic acid by using waste catalyst
A waste catalyst, molybdic acid technology, applied in the direction of improving process efficiency, can solve the problems of complex metal element recovery process, and achieve the effect of easy popularization and application and high metal recovery rate
- Summary
- Abstract
- Description
- Claims
- Application Information
AI Technical Summary
Problems solved by technology
Method used
Examples
Embodiment 1
[0027] (1) Take the spent catalyst crushed to more than 500 mesh, and roast it at 730°C for 9 hours in an air atmosphere;
[0028] (2) Weigh 50 grams of the above spent catalyst and 260 grams of ammonium bicarbonate, add 800 grams of distilled water to the above materials and stir for 20 minutes, transfer the mixed materials into an autoclave and raise the temperature to 140°C for hydrothermal treatment for 6.5 hours. After hydrothermal treatment, the material was filtered, and the filtrate was left to stand at 5°C for 100 hours. The filtrate after standing was filtered to obtain crystals B and solution C. Crystals B were determined to be ammonium vanadate crystals by XRD, and solution C was chemically Titration and ion chromatography were determined to be molybdenum-containing solution;
[0029] (3) Add concentrated nitric acid solution to solution C in step (3), control the pH value of the solution to 1.7 to precipitate precipitates, and after the precipitates are washed and...
Embodiment 2
[0031] Same as Example 1, except that the mesh number of the spent catalyst is 600 mesh, the roasting temperature is 840°C, the amount of ammonium bicarbonate added is 320 grams, the hydrothermal treatment temperature is 150°C, the treatment time is 5.5 hours, and the filtrate standing temperature is 8°C , the standing time was 75 hours, the concentrated nitric acid was changed to concentrated sulfuric acid, and the pH value of the control solution was 2.3; after calculation, the recovery rate of molybdenum in the spent catalyst after treatment was 90.1%, and the recovery rate of vanadium was 89.4%.
Embodiment 3
[0033] Same as Example 1, except that the mesh number of the spent catalyst is 800 mesh, the roasting temperature is 780°C, the ammonium bicarbonate addition is 355 grams, the hydrothermal treatment temperature is 130°C, the treatment time is 7.5 hours, and the filtrate standing temperature is 10°C , the standing time was 140 hours, and the pH value of the control solution was 2.6. After calculation, the recovery rate of molybdenum in the spent catalyst after treatment was 92.3%, and the recovery rate of vanadium was 91.5%.
PUM
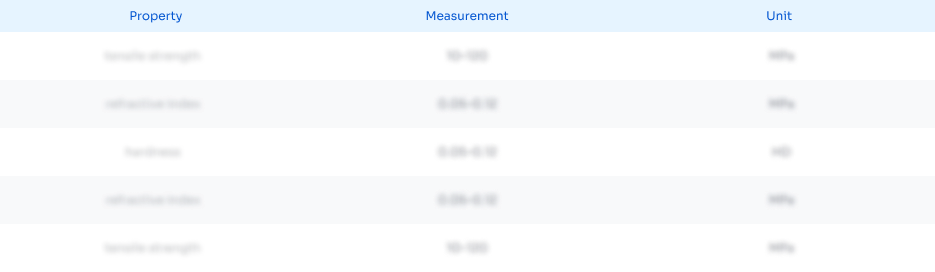
Abstract
Description
Claims
Application Information

- Generate Ideas
- Intellectual Property
- Life Sciences
- Materials
- Tech Scout
- Unparalleled Data Quality
- Higher Quality Content
- 60% Fewer Hallucinations
Browse by: Latest US Patents, China's latest patents, Technical Efficacy Thesaurus, Application Domain, Technology Topic, Popular Technical Reports.
© 2025 PatSnap. All rights reserved.Legal|Privacy policy|Modern Slavery Act Transparency Statement|Sitemap|About US| Contact US: help@patsnap.com