Converter tapping metallurgy process for reducing large-size inclusions in bearing steel
A technology for bearing steel and inclusions, which is applied in the field of iron and steel metallurgy production, can solve the problems of unstable control of large-sized inclusions, and achieve the effects of reducing nozzle nodulation, strong process stability, and reducing operations
- Summary
- Abstract
- Description
- Claims
- Application Information
AI Technical Summary
Problems solved by technology
Method used
Image
Examples
Embodiment 1
[0051] (1) Molten steel preparation for converter smelting: put 118t of pretreated molten iron and 32t of scrap cold material into the converter for blowing, add lime, dolomite and other slagging agents to complete the tasks of dephosphorization, decarburization, and temperature rise, and the converter blowing is completed The molten steel composition is: ω[C] 0.14%, ω[Si] 0.001%, ω[Mn] 0.092%, ω[P] 0.012%, ω[S] 0.017%, ω[Cr] 0.032%, tapping The temperature is 1600°C. , Carry out slag blocking operation before tapping.
[0052] (2) Ladle preparation: the basicity of the binary slag smelted in the first two furnaces of the used ladle is 5-9, there is no obvious residue after the ladle is cleaned, and the temperature of the ladle is 1100°C.
[0053] (3) Alloy and slag addition method in the tapping process: when the tapping amount reaches 1 / 5 of the total tapping amount, add 360kg of aluminum-iron alloy for deoxidation, and add 300kg of ferrosilicon and low-carbon manganese whe...
Embodiment 2
[0057] (1) Preparation of molten steel for converter smelting: put 130t of pretreated molten iron and 15t of scrap cold material into the converter for blowing, add lime, dolomite and other slagging agents to complete the tasks of dephosphorization, decarburization, and temperature rise, and the converter blowing is completed The molten steel composition is: ω[C] 0.15%, ω[Si] 0.001%, ω[Mn] 0.089%, ω[P] 0.010%, ω[S] 0.015%, ω[Cr] 0.033%, tapping The temperature is 1645°C. , Carry out slag blocking operation before tapping.
[0058] (2) Ladle preparation: The basicity of the binary slag smelted in the first two furnaces of the used ladle is 4.6-8.5, there is no obvious residue after the ladle is cleaned, and the temperature of the ladle is 1090°C.
[0059] (3) Alloy and slag addition method in the tapping process: when the tapping amount reaches 1 / 5 of the total tapping amount, add 400kg of aluminum-iron alloy for deoxidation, and add 296kg of ferrosilicon and low-carbon mangan...
Embodiment 3
[0063] (1) Molten steel preparation for converter smelting: put 125t of pretreated molten iron and 18t of scrap cold material into the converter for blowing, add lime, dolomite and other slagging agents to complete the tasks of dephosphorization, decarburization, and temperature rise, and the converter blowing is completed The molten steel composition is: ω[C] 0.20%, ω[Si] 0.003%, ω[Mn] 0.098%, ω[P] 0.013%, ω[S] 0.021%, ω[Cr] 0.051%, tapping The temperature is 1615°C. , Carry out slag blocking operation before tapping.
[0064] (2) Ladle preparation: the basicity of the binary slag smelted in the first two furnaces of the used ladle is 5-8.7, there is no obvious residue after the ladle is cleaned, and the temperature of the ladle is 1100°C.
[0065] (3) Alloy and slag addition method in the tapping process: when the tapping amount reaches 1 / 5 of the total tapping amount, add 380kg of aluminum-iron alloy for deoxidation, and add 322kg of ferrosilicon and low-carbon manganese w...
PUM
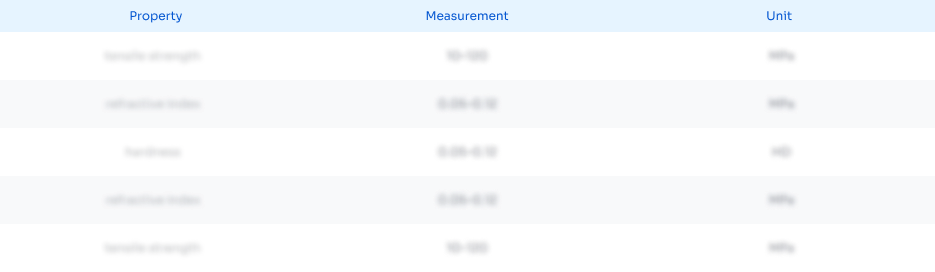
Abstract
Description
Claims
Application Information

- R&D
- Intellectual Property
- Life Sciences
- Materials
- Tech Scout
- Unparalleled Data Quality
- Higher Quality Content
- 60% Fewer Hallucinations
Browse by: Latest US Patents, China's latest patents, Technical Efficacy Thesaurus, Application Domain, Technology Topic, Popular Technical Reports.
© 2025 PatSnap. All rights reserved.Legal|Privacy policy|Modern Slavery Act Transparency Statement|Sitemap|About US| Contact US: help@patsnap.com