Preparation method of nickel-based alloy welding wire
A nickel-based alloy and welding wire technology, which is applied in the field of nickel-based alloy welding wire preparation, can solve problems such as easy generation of hot cracks, adverse effects on mechanical properties of components, and poor thermal corrosion resistance of nickel-based alloys.
- Summary
- Abstract
- Description
- Claims
- Application Information
AI Technical Summary
Problems solved by technology
Method used
Image
Examples
Embodiment 1
[0032] This embodiment provides a kind of auxiliary agent, is made by the following steps:
[0033] Step A1, prepare the following raw materials in parts by weight: 2.8 parts of phosphoric acid, 20 parts of rosin derivatives, 10 parts of diethylene glycol monobutyl ether, and 50 parts of polyethylene glycol;
[0034] Step A2: Put the raw materials in the above formula in a reaction kettle, heat up to 100°C for 10 minutes, then cool down to 65°C, stir and mix for 30 minutes, then cool down to room temperature, and grind 3 times to obtain additives.
[0035] Wherein, rosin derivative is made by following steps:
[0036] Step S1. Add 500g of masson pine rosin to the four-necked flask, and start to raise the temperature while introducing nitrogen. When the temperature rises to 180°C, add 131g of maleic anhydride in 5 times in equal amounts, with an interval of 5 minutes between each addition. After the addition, keep warm React for 4 hours, transfer to turpentine at 45°C while it...
Embodiment 2
[0041] This embodiment provides a kind of auxiliary agent, is made by the following steps:
[0042] Step A1, prepare the following raw materials in parts by weight: 3.0 parts of phosphoric acid, 23 parts of rosin derivatives, 12 parts of diethylene glycol monobutyl ether, and 55 parts of polyethylene glycol;
[0043] Step A2. Put the raw materials in the above formula in a reaction kettle, heat up to 100°C for 15 minutes, then cool down to 68°C, stir and mix for 32 minutes, then cool down to room temperature, and grind 4 times to obtain the additive.
[0044] Wherein, rosin derivative is made by following steps:
[0045] Step S1. Add 500g of masson pine rosin to the four-necked flask, and start to raise the temperature while introducing nitrogen. When the temperature rises to 180°C, add 132g of maleic anhydride in equal amounts in 5 times, with an interval of 5 minutes between each addition. After the addition, keep warm React for 4 hours, transfer it to turpentine oil at 48°...
Embodiment 3
[0050] This embodiment provides a kind of auxiliary agent, is made by the following steps:
[0051] Step A1, prepare the following raw materials in parts by weight: 3.2 parts of phosphoric acid, 25 parts of rosin derivatives, 18 parts of diethylene glycol monobutyl ether, and 60 parts of polyethylene glycol;
[0052] Step A2. Put the raw materials in the above formula in a reaction kettle, heat up to 100°C for 10-20 minutes, then cool down to 70°C, stir and mix for 35 minutes, then cool down to room temperature, and grind 5 times to obtain the auxiliary agent.
[0053] Wherein, rosin derivative is made by following steps:
[0054] Step S1. Add 500g of masson pine rosin to the four-necked flask, and start to raise the temperature while introducing nitrogen. When the temperature rises to 180°C, add 136g of maleic anhydride in equal amounts in 5 times, with an interval of 5 minutes between each addition, and keep warm after the addition React for 4 hours, transfer to turpentine ...
PUM
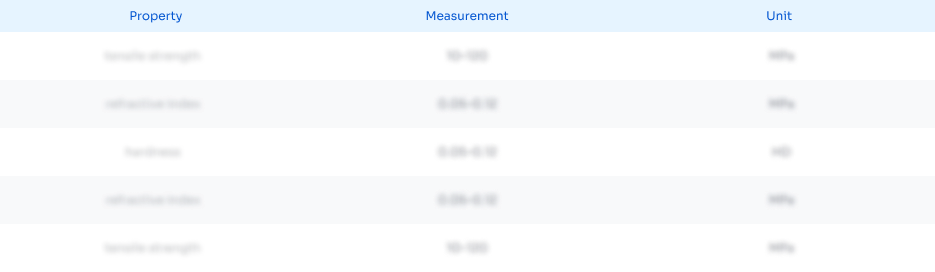
Abstract
Description
Claims
Application Information

- R&D Engineer
- R&D Manager
- IP Professional
- Industry Leading Data Capabilities
- Powerful AI technology
- Patent DNA Extraction
Browse by: Latest US Patents, China's latest patents, Technical Efficacy Thesaurus, Application Domain, Technology Topic, Popular Technical Reports.
© 2024 PatSnap. All rights reserved.Legal|Privacy policy|Modern Slavery Act Transparency Statement|Sitemap|About US| Contact US: help@patsnap.com