Halogen-free flame-retardant identification sleeve capable of being subjected to laser etching and preparation method thereof
A laser engraving and marking technology, applied in the field of casing preparation, can solve problems such as halogen, easy to fade or even fall off, high smoke density, etc.
- Summary
- Abstract
- Description
- Claims
- Application Information
AI Technical Summary
Problems solved by technology
Method used
Image
Examples
Embodiment 1
[0069] In terms of parts by weight, 30 parts of modified solvent-resistant plastic masterbatches, 30 parts of ammonium polyphosphate, 0.1 parts of trimethylolpropane trimethacrylate, 1 part of silica-wrapped micaceous iron oxide, and 0.5 parts of pentaerythritol ester , N, N'-di(β-naphthyl)-p-phenylenediamine 0.5 parts, zinc oxide 5 parts, polyethylene wax 0.5 parts, carbon black 2 parts, blended and banburyed by internal mixer for 10 minutes, and then passed through cone The twin-screw extruder is eagerly cut to obtain the modified radium engraving masterbatch;
[0070] Extrude the above-mentioned modified radium engraving masterbatch through a single-screw extruder at 150°C;
[0071] Carry out irradiation cross-linking by the above-mentioned tube blank through an electron accelerator, and the irradiation dose is 150kGy;
[0072] The above-mentioned radiation cross-linked tube blank is expanded by 150 °C expansion machine for 2 times, cooled and set;
[0073] The above-ment...
Embodiment 2
[0075] According to parts by weight, 30 parts of modified solvent-resistant plastic masterbatch, 30 parts of ammonium polyphosphate, 0.1 part of trimethylolpropane trimethacrylate, 1 part of self-made flame-retardant laser auxiliary agent, 0.5 part of pentaerythritol ester, 0.5 parts of N, N'-di(β-naphthyl)-p-phenylenediamine, 5 parts of zinc oxide, 0.5 parts of polyethylene wax, and 2 parts of carbon black were blended and banburyed by an internal mixer for 10 minutes, and then passed through a conical double Screw extruded eagerly to obtain modified radium engraving masterbatch;
[0076] Extrude the above-mentioned modified radium engraving masterbatch through a single-screw extruder at 150°C;
[0077] Carry out irradiation cross-linking by the above-mentioned tube blank through an electron accelerator, and the irradiation dose is 150kGy;
[0078] The above-mentioned radiation cross-linked tube blank is expanded by 150 °C expansion machine for 2 times, cooled and set;
[0...
Embodiment 3
[0081] According to parts by weight, 30 parts of modified solvent-resistant plastic masterbatch, 30 parts of ammonium polyphosphate, 0.1 part of trimethylolpropane trimethacrylate, 1 part of basic copper phosphate, 0.5 part of pentaerythritol ester, N, 0.5 parts of N'-di(β-naphthyl)-p-phenylenediamine, 5 parts of zinc oxide, 0.5 parts of polyethylene wax, and 2 parts of carbon black were blended and kneaded by an internal mixer for 10 minutes, and then extruded through a conical twin-screw. out eagerly, to obtain the modified radium engraving masterbatch;
[0082] Extrude the above-mentioned modified radium engraving masterbatch through a single-screw extruder at 150°C;
[0083] Carry out irradiation cross-linking by the above-mentioned tube blank through an electron accelerator, and the irradiation dose is 150kGy;
[0084] The above-mentioned radiation cross-linked tube blank is expanded by 150 °C expansion machine for 2 times, cooled and set;
[0085] The above-mentioned e...
PUM
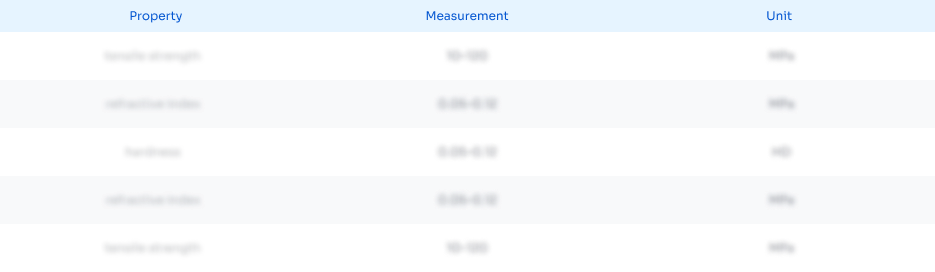
Abstract
Description
Claims
Application Information

- R&D Engineer
- R&D Manager
- IP Professional
- Industry Leading Data Capabilities
- Powerful AI technology
- Patent DNA Extraction
Browse by: Latest US Patents, China's latest patents, Technical Efficacy Thesaurus, Application Domain, Technology Topic, Popular Technical Reports.
© 2024 PatSnap. All rights reserved.Legal|Privacy policy|Modern Slavery Act Transparency Statement|Sitemap|About US| Contact US: help@patsnap.com