Castable as well as preparation method and application thereof
A pouring material and pouring molding technology, which is applied in the direction of manufacturing tools, heat treatment equipment, casting molding equipment, etc., can solve the problems of poor thermal conductivity, fatigue resistance, poor thermal conductivity, and easy cracking of the mold by alternating cold and hot, and achieve reduction Effect of pearlite content, improvement of service life, and inhibition of cracking tendency
- Summary
- Abstract
- Description
- Claims
- Application Information
AI Technical Summary
Problems solved by technology
Method used
Examples
Embodiment 1
[0034] This embodiment provides a special mold material for alloy casting and its preparation method. The mass percentage of its chemical composition is: C3.15%; Si1.53%; Mn0.46%; P0.03%; S0.03%; Mg0 .022%; Re0.016%, Ti0.18%, and the balance is Fe.
[0035] The preparation method of mold comprises the following steps:
[0036] (1) Weigh each raw material according to a certain mass percentage, first add 72% of pig iron and 25% of low-carbon steel to the electric furnace, after complete melting, add 0.75% of ferrosilicon and 0.46% of ferromanganese, heat up to 1480~1520℃ and add titanium Iron 0.38%, keep warm for 2~3 minutes and then release from the oven.
[0037] (2) 0.55% rare-earth magnesium-silicon alloy and 0.3% ferrosilicon alloy are used for modification treatment when it is released from the furnace. The treated molten iron is cast into sand molds, and the pouring temperature is controlled at 1360~1400°C.
[0038] (3) Perform artificial aging treatment on the mold ca...
Embodiment 2
[0040] This embodiment provides a special mold material for alloy casting and its preparation method. The mass percentage of its chemical composition is: C3.24%; Si1.60%; Mn0.55%; P0.025%; S0.022%; Mg0 .020%; Re0.017%, Ti0.14%, the balance is Fe.
[0041]The preparation method of mold comprises the following steps:
[0042] (1) Weigh each raw material according to a certain mass percentage, first add 75% of pig iron and 23% of low-carbon steel to the electric furnace, after complete melting, add 0.83% of ferrosilicon and 0.62% of ferromanganese, heat up to 1480~1520℃ and add titanium Iron 0.29%, keep warm for 2~3 minutes and then release from the oven.
[0043] (2) 0.55% rare-earth magnesium-silicon alloy and 0.3% ferrosilicon alloy are used for modification treatment when it is released from the furnace. The treated molten iron is cast into sand molds, and the pouring temperature is controlled at 1360~1400°C.
[0044] (3) Perform artificial aging treatment on the mold casti...
Embodiment 3
[0046] This embodiment provides a special mold material for alloy casting and its preparation method. The mass percentage of its chemical composition is: C3.25%; Si1.69%; Mn0.38%; P0.024%; S0.026%; Mg0 .020%; Re0.016%, Ti0.16%, and the balance is Fe.
[0047] The preparation method of mold comprises the following steps:
[0048] (1) Weigh each raw material according to a certain mass percentage, first add 75% of pig iron and 22.5% of low-carbon steel to the electric furnace, after complete melting, add 0.96% of ferrosilicon and 0.35% of ferromanganese, heat up to 1480~1520℃ and add titanium Iron 0.34%, keep warm for 2~3 minutes and then release from the oven.
[0049] (2) 0.55% rare-earth magnesium-silicon alloy and 0.4% ferrosilicon alloy are used for modification treatment when it is released from the furnace. The treated molten iron is cast into sand molds, and the pouring temperature is controlled at 1360~1400°C.
[0050] (3) Perform artificial aging treatment on the mol...
PUM
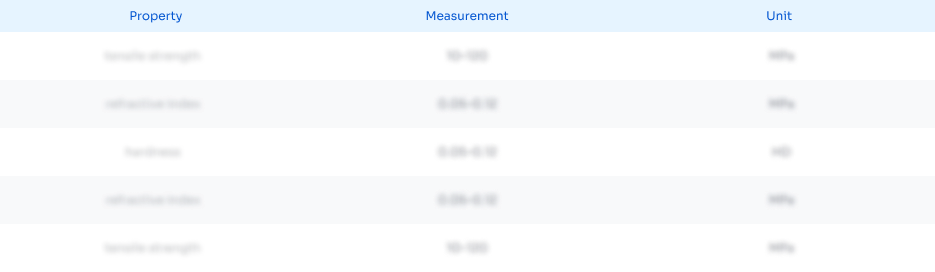
Abstract
Description
Claims
Application Information

- R&D
- Intellectual Property
- Life Sciences
- Materials
- Tech Scout
- Unparalleled Data Quality
- Higher Quality Content
- 60% Fewer Hallucinations
Browse by: Latest US Patents, China's latest patents, Technical Efficacy Thesaurus, Application Domain, Technology Topic, Popular Technical Reports.
© 2025 PatSnap. All rights reserved.Legal|Privacy policy|Modern Slavery Act Transparency Statement|Sitemap|About US| Contact US: help@patsnap.com