Preparation method of 3-methyl-1, 5-pentanediol
A technology of pentanediol and methylpentane, which is applied in the field of preparing 3-methyl-1,5-pentanediol, can solve the problems of increased separation energy consumption, reduced selectivity and high cost, and can improve the reaction rate and reaction rate. Equilibrium constant, reaction to reduce double bond hydration, effect to reduce ratio of isomers
- Summary
- Abstract
- Description
- Claims
- Application Information
AI Technical Summary
Problems solved by technology
Method used
Image
Examples
Embodiment 1
[0042]1) First, add 180g (3.2mol) of isobutylene into the autoclave, start stirring and raise the temperature to 275°C, and the pressure to 9MPa, then add 1.2g of catalyst propane sulfonate pyridinium salt, 0.3g of auxiliary ferrous phosphate, and then add 900g of 50wt % (14.9mol) formaldehyde aqueous solution, the pH of the system is 6.8 after adding the material, and react at 275°C for 20 minutes. After the reaction is completed, a cooling liquid is passed to cool down, and the unreacted isobutene is recovered by flash evaporation, and then rectified and separated to obtain the condensation product 3 -Methylenepentane-1,5-diol and 3-methylpent-2-ene-1,5-pentanediol, formaldehyde conversion 95.6%, 3-methylenepentane-1,5-diol Alcohol selectivity was 93.2%, and 3-methylpent-2-ene-1,5-pentanediol selectivity was 6.1%.
[0043] NMR spectrum of 3-methylenepentane-1,5-diol:
[0044] 1 H-NMR (CDCl 3 )δ: 2.15(4H), 3.57(4H), 3.65(2H), 4.92(1H), 5.11(1H)
[0045] NMR spectrum of 3-...
Embodiment 2
[0051] 1) First, add 250g (4.5mol) of isobutene into the autoclave, start stirring and raise the temperature to 185°C, and the pressure to 6MPa, then add 24g of catalyst pyridine mesylate, 1.2g of sodium dihydrogen phosphate, and then add 542.95g 37% (6.7mol) formaldehyde aqueous solution, the pH of the system is 4 after adding the material, and then react at 185 ° C for 10 minutes. After the reaction is completed, the cooling liquid is passed to cool down, and the unreacted isobutene is recovered by flash evaporation, and then separated by rectification to obtain the condensation product 3-Methylenepentane-1,5-diol and 3-methylpent-2-ene-1,5-pentanediol, formaldehyde conversion 95.2%, 3-Methylenepentane-1,5- The selectivity to diol was 95.2%, and the selectivity to 3-methylpent-2-ene-1,5-pentanediol was 4.6%.
[0052] 2) Take 100g of the 3-methylenepentane-1,5-diol and 3-methylpent-2-ene-1,5-pentanediol mixture obtained in step 1) and add 1.2g RC-311 as Hydrogenation catalys...
Embodiment 3
[0054] 1) First, add 300g (5.3mol) of isobutene into the autoclave, start stirring and raise the temperature to 200°C, and the pressure to 10MPa, then add 20g of the catalyst pyridinium p-toluenesulfonate, 13g of the auxiliary agent disodium dihydrogen pyrophosphate, and then add 1004.4g of 40% (13.4mol) formaldehyde aqueous solution, the pH of the system after adding the material is 3, react at 200°C for 15min, after the reaction is completed, pass in a cooling liquid to cool down, recover unreacted isobutene by flash evaporation, and then carry out rectification and separation to obtain condensation Products 3-methylenepentane-1,5-diol and 3-methylpent-2-ene-1,5-pentanediol, formaldehyde conversion rate 96.40%, 3-methylenepentane-1,5 -diol selectivity 96.40%, 3-methylpent-2-ene-1,5-pentanediol selectivity 3.4%.
[0055] 2) Take 100g of the 3-methylenepentane-1,5-diol and 3-methylpent-2-ene-1,5-pentanediol mixture obtained in step 1) and add 9.5g of 1,1- Bis(di-tert-butylpho...
PUM
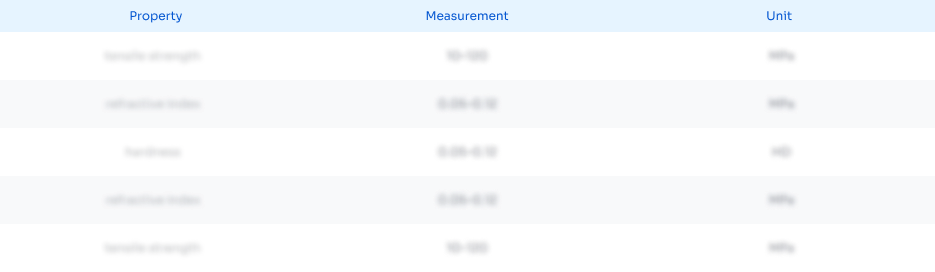
Abstract
Description
Claims
Application Information

- R&D
- Intellectual Property
- Life Sciences
- Materials
- Tech Scout
- Unparalleled Data Quality
- Higher Quality Content
- 60% Fewer Hallucinations
Browse by: Latest US Patents, China's latest patents, Technical Efficacy Thesaurus, Application Domain, Technology Topic, Popular Technical Reports.
© 2025 PatSnap. All rights reserved.Legal|Privacy policy|Modern Slavery Act Transparency Statement|Sitemap|About US| Contact US: help@patsnap.com