Special high-surface-tension PC/ABS material for in-mold transfer printing and preparation method thereof
An ABS material, in-mold transfer technology, applied in the field of polymer materials, can solve the problems of insufficient surface tension, low qualified rate of transfer finished products, pattern breakage, etc., to prevent the viscosity of the system from rising, improve color brightness, improve pigment dispersive effect
- Summary
- Abstract
- Description
- Claims
- Application Information
AI Technical Summary
Problems solved by technology
Method used
Image
Examples
preparation example Construction
[0028] The preparation method of the special high surface tension PC / ABS material for in-mold transfer printing comprises the following steps:
[0029] (1) Take each component in proportion;
[0030] (2) Add ABS resin, PC resin, compatibilizer, coupling agent, antioxidant and lubricant in proportion to the high-speed mixer to obtain the mixture after high-speed mixing;
[0031] (3) The mixture obtained in step (2) is sent into a twin-screw extruder, and the required PC / ABS material is obtained after melt blending, extrusion granulation, and drying;
[0032] Wherein, the preparation process temperature of each zone of the twin-screw extruder is: zone 1 100°C, zone 2 200°C, zone 3 220°C, zone 4 230°C, zone 5 230°C, zone 6 220°C, zone 7 220°C , 220°C in the eighth zone, 220°C in the ninth zone, 220°C in the tenth zone, and a head temperature of 230°C; the screw speed of the twin-screw extruder is 400-600 rpm.
[0033] The specific component weight percentages of each embodiment...
Embodiment 1
[0035] A PC / ABS material with high surface tension for in-mold transfer printing, including the following components by weight percentage:
[0036]
[0037] In this embodiment, the lubricant is PETS, and the screw speed of the twin-screw extruder is 400 rpm.
Embodiment 2
[0039] A PC / ABS material with high surface tension for in-mold transfer printing, including the following components by weight percentage:
[0040]
[0041] In this embodiment, the lubricant is silicone masterbatch, and the screw speed of the twin-screw extruder is 4600 rpm.
PUM
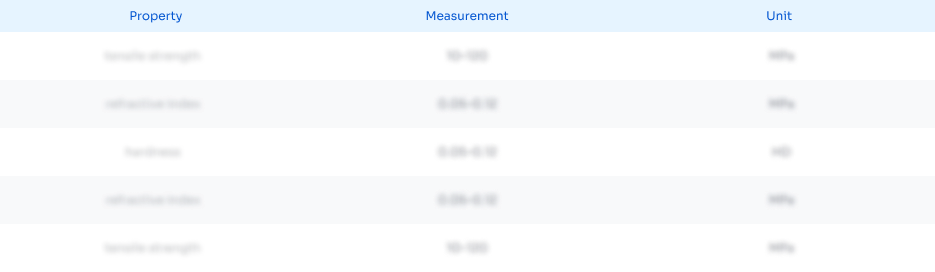
Abstract
Description
Claims
Application Information

- R&D
- Intellectual Property
- Life Sciences
- Materials
- Tech Scout
- Unparalleled Data Quality
- Higher Quality Content
- 60% Fewer Hallucinations
Browse by: Latest US Patents, China's latest patents, Technical Efficacy Thesaurus, Application Domain, Technology Topic, Popular Technical Reports.
© 2025 PatSnap. All rights reserved.Legal|Privacy policy|Modern Slavery Act Transparency Statement|Sitemap|About US| Contact US: help@patsnap.com