Single-field anhydrous stemming for high-strength smelting small blast furnace as well as preparation method and application of single-field anhydrous stemming
An anhydrous taphole clay and blast furnace technology, which is applied in the field of refractory materials and metallurgy, can solve the problems of increasing labor intensity of workers, increasing consumption before iron, poor opening of tapholes, etc., achieving good mud fighting performance and resistance to erosion and erosion of taphole clay. Good properties and fast curing speed
- Summary
- Abstract
- Description
- Claims
- Application Information
AI Technical Summary
Problems solved by technology
Method used
Image
Examples
Embodiment 1
[0040] Ingredients are prepared according to the following ratio of raw materials: quartz 3-1mm 13%, slide 3-1mm 7%, slide 1-0.088mm 10%, Guangxi white mud 8%, albite powder 7%, coke foam 3-1mm 16%, carbonization Silicon powder 16%, graphite electrode powder 2%, phenolic resin powder 2%, modified asphalt 6%, skateboard powder 13%.
[0041] The above raw materials were mixed in a pre-mixer for 4 minutes; coal tar was added into the mixer, fully mixed and rolled to a suitable state, and then the mud was discharged, squeezed into shape, and packaged to obtain a single-field anhydrous tapped mud product for high-strength smelting small blast furnaces.
[0042] This high-strength smelting small blast furnace is used in single field anhydrous taphole clay, in a certain 450m 3 It is used on a blast furnace, the tapping interval is 30 minutes, there is no thick smoke and high tide mud during the opening process, basically no need for baking iron spouts, the splashing time after openin...
Embodiment 2
[0044] Ingredients are prepared according to the following ratio of raw materials: pyrophyllite 3-1mm 10%, pyrophyllite 1-0.088mm 10%, coal gangue 3-1mm 7%, Jiaozuo clay 10%, potassium feldspar powder 9%, coke foam 3-1mm 18%, silicon carbide powder 14%, ferrosilicon nitride 5%, graphite electrode powder 1%, phenolic resin powder 0.5%, modified asphalt 5%, alumina powder 10.5%.
[0045] The above raw materials were mixed in a pre-mixer for 5 minutes; coal tar was added into the mixer, fully mixed and rolled to a suitable state, and then the mud was discharged, squeezed into shape, and packaged to obtain a single-field anhydrous tapped mud product for high-strength smelting small blast furnaces.
[0046] This high-strength smelting small blast furnace uses single field anhydrous taphole mud, in a certain 580m 3 It is used on a blast furnace, and the tapping interval is 25 minutes. During the opening process, there is no thick smoke or high tide mud, basically no need for baking ...
Embodiment 3
[0048]Ingredients are made according to the following raw materials: quartz 3~1mm 17%, torpedo brick 1~0.088mm 10%, Guangxi white mud 8%, albite powder 12%, coke foam 3~1mm 15%, silicon carbide powder 15%, graphite Electrode powder 5%, phenolic resin powder 1%, modified asphalt 7%, torpedo tank brick powder 10%.
[0049] The above raw materials were mixed in a pre-mixer for 6 minutes; coal tar was added into the mixer, fully mixed and rolled to a suitable state, and then the mud was discharged, squeezed into shape, and packaged to obtain a single-field anhydrous tapped mud product for high-strength smelting small blast furnaces.
[0050] The high-strength smelting small blast furnace is used in single field anhydrous taphole mud, in a certain 350m 3 When used in blast furnaces, it is required to see iron at an interval of 25 minutes. During the opening process, there will be no smoke or high tide mud. Baking iron holes are basically not needed.
PUM
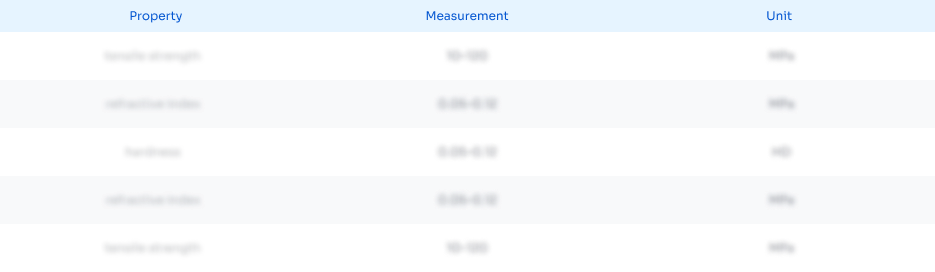
Abstract
Description
Claims
Application Information

- R&D
- Intellectual Property
- Life Sciences
- Materials
- Tech Scout
- Unparalleled Data Quality
- Higher Quality Content
- 60% Fewer Hallucinations
Browse by: Latest US Patents, China's latest patents, Technical Efficacy Thesaurus, Application Domain, Technology Topic, Popular Technical Reports.
© 2025 PatSnap. All rights reserved.Legal|Privacy policy|Modern Slavery Act Transparency Statement|Sitemap|About US| Contact US: help@patsnap.com