Steel-solid waste concrete combined bearing platform with composite structure and construction method thereof
A technology of waste concrete and concrete-filled steel tube piles, which is used in infrastructure engineering, construction, sheet pile walls, etc., can solve the problems of yielding of steel bars on the upper surface, local shear failure, and overall punching failure, etc., and achieve joint stiffness improvement and reduction. The effect of developing and increasing the degree of connection
- Summary
- Abstract
- Description
- Claims
- Application Information
AI Technical Summary
Problems solved by technology
Method used
Image
Examples
specific Embodiment approach 1
[0035] Specific implementation mode one: see Figure 1-5 This embodiment will be described. The steel-solid waste concrete combined cap with a composite structure described in this embodiment includes a closed box, a steel tube concrete column 7, four steel tube concrete piles 8, a shear truss 11, a force coordination truss 14 and solid waste concrete 16. The four concrete-filled steel pipe piles 8 are respectively located at the four corners of the composite cap. The concrete-filled steel pipe columns 7 penetrate the top plate of the closed box, and the four concrete-filled steel pipe piles 8 penetrate the bottom plate of the closed box. A shear truss 11 is set between the steel tube concrete piles 8, a force coordination truss 14 is set between two adjacent steel tube concrete piles 8, and other positions of the closed box are densely filled with solid waste concrete 16 or steel bar-solid waste concrete.
[0036] The concrete-filled steel pipe column 7 includes a reinforcem...
PUM
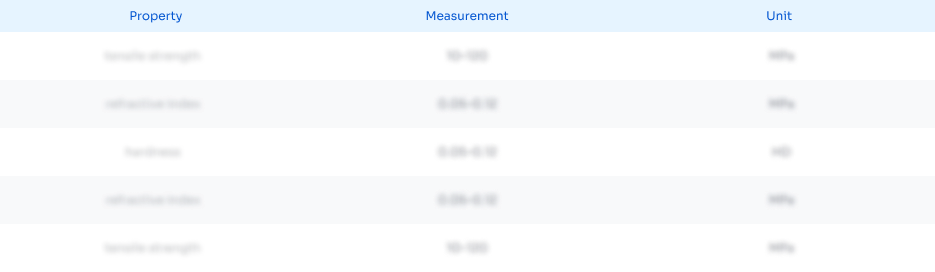
Abstract
Description
Claims
Application Information

- R&D
- Intellectual Property
- Life Sciences
- Materials
- Tech Scout
- Unparalleled Data Quality
- Higher Quality Content
- 60% Fewer Hallucinations
Browse by: Latest US Patents, China's latest patents, Technical Efficacy Thesaurus, Application Domain, Technology Topic, Popular Technical Reports.
© 2025 PatSnap. All rights reserved.Legal|Privacy policy|Modern Slavery Act Transparency Statement|Sitemap|About US| Contact US: help@patsnap.com