Anti-recrystallization method in repair process of turbine blade after service
A technology of turbine blade and recrystallization, which is applied in the direction of heat treatment process control, furnace type, furnace, etc., can solve the problems affecting the service performance of turbine blades and the defects of recrystallization of turbine blades.
- Summary
- Abstract
- Description
- Claims
- Application Information
AI Technical Summary
Problems solved by technology
Method used
Image
Examples
Embodiment 1
[0060] Example 1 Tissue Repair of Turbine Guide Vanes After Overheating Service
[0061] Turbine guide blades have overheated in service, and the overheated temperature is 1250°C (the normal service temperature is 1150°C).
[0062] First: observe the original structure of the turbine guide vane, and use the DSC analysis method to determine the initial melting back temperature T of the γ’ phase of the original turbine guide vane s 1280°C and complete melting back temperature T f The initial melting point temperature of the alloy is 1320°C and 1350°C.
[0063] Second: Stress-relief treatment is carried out on the guide vanes of overheated turbines in service. The specific parameters are: heating up to 900±20°C, holding for 3 hours, and cooling with the furnace.
[0064] Then, anti-recrystallization heat treatment is carried out, and the specific parameters are: increase to 1200±5°C at a rate of 10°C / min, hold for 0.5h, and then cool down to 1100±5°C at a rate of 10°C / min; cont...
Embodiment 2
[0068] Example 2 Tissue Repair of Turbine Working Blades in Creep Service
[0069] For the turbine working blade, it bears a certain centrifugal force, mainly due to the degradation of the structure after creep, including the dissolution, coarsening and rafting of the γ’ phase.
PUM
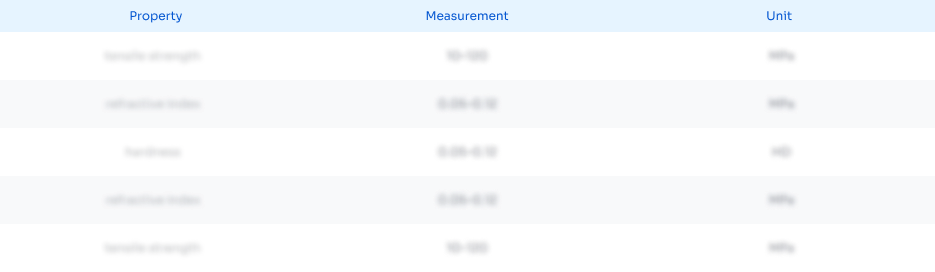
Abstract
Description
Claims
Application Information

- R&D
- Intellectual Property
- Life Sciences
- Materials
- Tech Scout
- Unparalleled Data Quality
- Higher Quality Content
- 60% Fewer Hallucinations
Browse by: Latest US Patents, China's latest patents, Technical Efficacy Thesaurus, Application Domain, Technology Topic, Popular Technical Reports.
© 2025 PatSnap. All rights reserved.Legal|Privacy policy|Modern Slavery Act Transparency Statement|Sitemap|About US| Contact US: help@patsnap.com