Preparation method of cellulose acetate-based composite membrane and application of cellulose acetate-based composite membrane in dynamic separation and extraction of tellurium
A technology of cellulose acetate and composite membrane, applied in semipermeable membrane separation, chemical instruments and methods, membrane technology, etc., can solve the problems of difficult and efficient separation and recovery, low separation efficiency, etc., and achieve low cost and high separation efficiency , the effect of simple operation
- Summary
- Abstract
- Description
- Claims
- Application Information
AI Technical Summary
Problems solved by technology
Method used
Image
Examples
Embodiment 1
[0025] A preparation method of cellulose acetate-based composite film, comprising the steps of:
[0026] a) Mix magnesium chloride, sodium carbonate and water in a molar volume ratio of 1:1:50 (mol / mL), add them to a polytetrafluoroethylene-lined autoclave, and conduct a hydrothermal reaction at 80°C for 10 hours, Cool, wash with distilled water and ethanol for 3 times, dry at 60°C for 12 hours, and calcinate at 500°C for 1 hour to obtain magnesium oxide microspheres;
[0027] b), the mass ratio of magnesium oxide microspheres to cellulose acetate is 1:20, the mass ratio of polyvinylpyrrolidone to cellulose acetate is 1:4, and the mass ratio of cellulose acetate to polyethylene glycol is 1:10, Mix magnesium oxide microspheres, cellulose acetate, polyvinylpyrrolidone, and polyethylene glycol at a volume ratio of 1:15 (g / mL) between the mass of cellulose acetate and solvent, stir at 50°C for 8 hours, let stand and cool, and 4mL of the mixed solution was cast on a glass plate an...
Embodiment 2
[0030] A preparation method of cellulose acetate-based composite film, comprising the steps of:
[0031] a) Mix magnesium nitrate, sodium acetate and water at a molar volume ratio of 1:1:50 (mol / mL), add them to a polytetrafluoroethylene-lined autoclave, and conduct a hydrothermal reaction at 70°C for 12 hours , cooled, washed with distilled water and ethanol for 3 times, dried at 70°C for 6 hours, and calcined at 600°C for 2 hours to obtain the magnesium oxide superstructure.
[0032] b), the mass ratio of magnesium oxide superstructure and cellulose acetate is 1:4, the mass ratio of polyvinylpyrrolidone and cellulose acetate is 1:2, and the mass ratio of cellulose acetate and polyethylene glycol is 1:10, Mix magnesium oxide superstructure, cellulose acetate, polyvinylpyrrolidone, and polyethylene glycol according to the volume ratio of the mass of cellulose acetate to the solvent of 1:15 (g / mL), stir at 50°C for 8h, let stand and cool, and 4mL of the mixed solution was cast...
Embodiment 3
[0034] A preparation method of cellulose acetate-based composite film, comprising the steps of:
[0035] a) Mix zirconium nitrate, urea and water at a molar volume ratio of 1:1:80 (mol / mL), add them to a polytetrafluoroethylene-lined autoclave, and conduct a hydrothermal reaction at 70°C for 8 hours. Cool, wash with distilled water and ethanol for three times, dry at 60°C for 12 hours, and calcinate at 600°C for 5 hours to obtain zirconia microspheres.
[0036] b), the mass ratio of zirconia microspheres to cellulose acetate is 1:4, the mass ratio of polyvinylpyrrolidone to cellulose acetate is 1:4, and the mass ratio of cellulose acetate to polyethylene glycol is 1:10, Mix zirconia microspheres, cellulose acetate, polyvinylpyrrolidone, and polyethylene glycol at a volume ratio of 1:15 (g / mL) between the mass of cellulose acetate and solvent, stir at 50°C for 8 hours, let stand and cool, and 5mL of the mixed solution was cast on a glass plate and immersed in deionized water t...
PUM
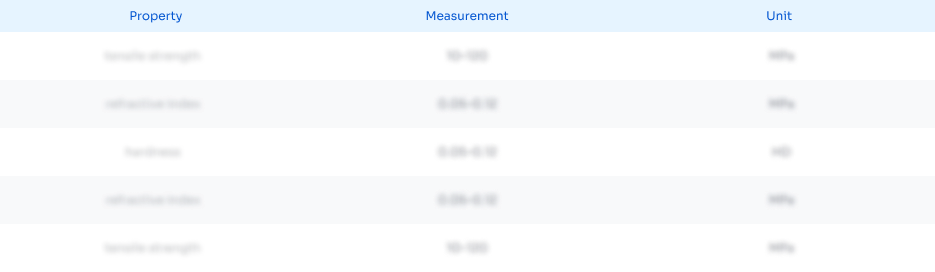
Abstract
Description
Claims
Application Information

- R&D Engineer
- R&D Manager
- IP Professional
- Industry Leading Data Capabilities
- Powerful AI technology
- Patent DNA Extraction
Browse by: Latest US Patents, China's latest patents, Technical Efficacy Thesaurus, Application Domain, Technology Topic, Popular Technical Reports.
© 2024 PatSnap. All rights reserved.Legal|Privacy policy|Modern Slavery Act Transparency Statement|Sitemap|About US| Contact US: help@patsnap.com