Method for reducing viscosity of thick oil by blending thin oil based on oil-based nano fluid
A nanofluid and heavy oil technology, applied in chemical instruments and methods, drilling compositions, molybdenum sulfide, etc., can solve the problems of large consumption of thin oil, poor viscosity reduction effect, low economic benefits, etc., to achieve good economic Benefits, reduce mining costs, improve the effect of thermal conductivity
- Summary
- Abstract
- Description
- Claims
- Application Information
AI Technical Summary
Problems solved by technology
Method used
Image
Examples
Embodiment 1
[0031] Step 1: Prepare magnetic molybdenum disulfide: prepare 100 mL of ethanol aqueous solution containing molybdenum disulfide with a mass fraction of 0.5% (the volume ratio of ethanol and water is 1:1), sonicate for 1 h; Hexaalkyltrimethylammonium bromide aqueous solution, at room temperature, stirring continuously at 800rpm for 3h; transfer the above liquid to a flask, add 2g of ferric chloride and 0.8g of ferrous chloride, and place in a constant temperature water bath at 80°C Add nitrogen gas (at a rate of 0.5 L / min) and continue the reaction for 1 h; add 10 mL of ammonium hydroxide with a concentration of 0.1 mol / L dropwise into the flask, and keep stirring for 4 h in a constant temperature water bath at 80°C; finally, the obtained liquid Filter, wash, and dry in a vacuum oven at 80°C for 6 hours to obtain magnetic molybdenum disulfide.
[0032] Step 2: Measure the diesel oil and weigh the magnetic molybdenum disulfide, disperse the magnetic molybdenum disulfide in the ...
Embodiment 2
[0039] Step 1: First, measure the initial viscosity of heavy oil at 40°C, 50°C, 60°C, 70°C, and 80°C respectively.
[0040] Step 2: Take 2 parts of heavy oil samples with a quality of 20g, weigh 5g each of the diesel oil and magnetic molybdenum disulfide / diesel dispersion in Example 1, add them to the heavy oil samples and stir evenly, and carry out thinning and viscosity reduction. The doping rate at this time was 20%.
[0041] Step 3: Measure the viscosity of two heavy oil samples mixed with thin oil at 40°C, 50°C, 60°C, 70°C, and 80°C respectively, and calculate the viscosity reduction rate. The results are shown in Table 2.
[0042] Table 2 Comparison of viscosity reduction rate of heavy oil mixed with diesel and magnetized molybdenum disulfide / diesel dispersion under different temperature conditions
[0043]
[0044] According to Table 2, under the condition of 20% dilution rate, when the temperature is 40 ℃ and 50 ℃, the viscosity reduction rate of magnetic molybdenum ...
Embodiment 3
[0047] The diesel oil, magnetic molybdenum disulfide / diesel dispersion and heavy oil in Examples 1 and 2 were used to carry out viscosity-reducing experiments at 50°C with different dilution ratios. The results are shown in Table 3.
[0048] Table 3 Comparison of viscosity reduction rate of heavy oil mixed with diesel and magnetized molybdenum disulfide / diesel dispersion under different dilution ratios
[0049]
[0050] According to Table 2, when the dilution rate is 5% and 10%, the viscosity reduction rate of diesel dispersion of magnetic molybdenum disulfide to heavy oil is 17.94% and 16.59% higher than that of diesel oil to heavy oil; When the dilution rate is 40% and 50%, it increases by 3.02% and 2.04% respectively. This shows that under the same temperature conditions, when the dilution rate is low, the viscosity-reducing effect of adding thin oil on heavy oil is mainly due to heat transfer, which reduces the viscosity of heavy oil. Therefore, the magnetized molybdenu...
PUM
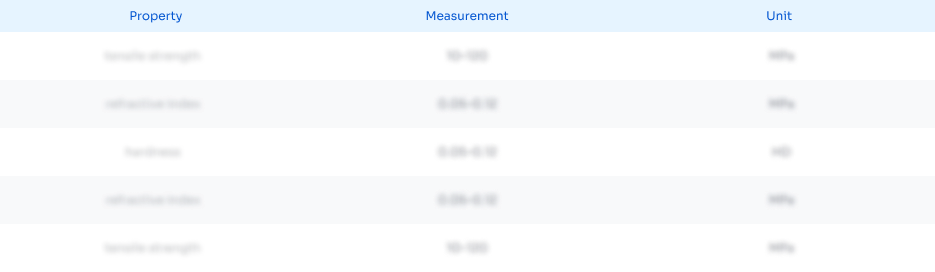
Abstract
Description
Claims
Application Information

- Generate Ideas
- Intellectual Property
- Life Sciences
- Materials
- Tech Scout
- Unparalleled Data Quality
- Higher Quality Content
- 60% Fewer Hallucinations
Browse by: Latest US Patents, China's latest patents, Technical Efficacy Thesaurus, Application Domain, Technology Topic, Popular Technical Reports.
© 2025 PatSnap. All rights reserved.Legal|Privacy policy|Modern Slavery Act Transparency Statement|Sitemap|About US| Contact US: help@patsnap.com