Preparation method of metal bump structure
A technology of metal bumps and insulating pads, applied in semiconductor/solid-state device manufacturing, semiconductor/solid-state device parts, semiconductor devices, etc., can solve problems such as short-circuiting and affecting chip performance
- Summary
- Abstract
- Description
- Claims
- Application Information
AI Technical Summary
Problems solved by technology
Method used
Image
Examples
Embodiment Construction
[0020] The embodiments described below by referring to the figures are exemplary, and are only for explaining the present invention, and cannot be construed as limiting the present invention.
[0021] Embodiments of the present invention: as Figure 9 As shown, a metal bump structure is disclosed, and the metal bump structure includes:
[0022] A bare chip 10, wherein the bare chip 10 includes a substrate 101, the upper surface of the substrate 101 is formed with a pad 102 and a passivation layer 103, and the pad 102 is outward from the passivation layer opening 104 on the passivation layer 103 Exposure; the material of the pad 102 includes metals such as aluminum and copper and metal alloys; the passivation layer 103 is used as a protective layer, and the material includes inorganic thin film materials such as silicon nitride and silicon oxide or dielectric properties such as polyimide. Good photosensitive organic polymer material.
[0023] The metal bump 20 is arranged on ...
PUM
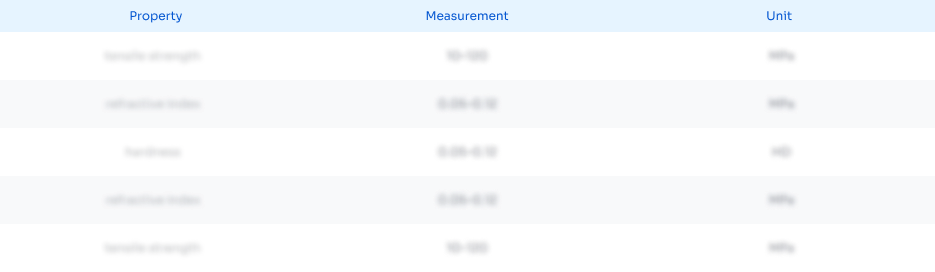
Abstract
Description
Claims
Application Information

- R&D
- Intellectual Property
- Life Sciences
- Materials
- Tech Scout
- Unparalleled Data Quality
- Higher Quality Content
- 60% Fewer Hallucinations
Browse by: Latest US Patents, China's latest patents, Technical Efficacy Thesaurus, Application Domain, Technology Topic, Popular Technical Reports.
© 2025 PatSnap. All rights reserved.Legal|Privacy policy|Modern Slavery Act Transparency Statement|Sitemap|About US| Contact US: help@patsnap.com