Medium and low temperature curing bio-based epoxy asphalt composite material and application thereof
A technology based on epoxy asphalt and composite materials, applied in building thermal insulation materials, building structures, building components, etc., can solve the problems of poor compatibility between epoxy resin and asphalt, low pollution, high curing temperature, and achieve improved performance and The effect of value, simple construction process and good workability
- Summary
- Abstract
- Description
- Claims
- Application Information
AI Technical Summary
Problems solved by technology
Method used
Examples
Embodiment 1
[0017] Medium and low temperature curing bio-based epoxy asphalt composite material is composed of two components A and B, and the proportion of component A is as follows: 35 parts of bisphenol A epoxy resin E51, 15 parts of oleic acid epoxy, polyethylene 4.9 parts of glycol diglycidyl ether, 0.1 part of curing accelerator triethylamine, 45 parts of petroleum pitch; B component is the curing agent tung oil-based polyamide; the ratio of parts by mass between components A and B is 100:60 .
[0018] Step 1: Petroleum pitch is placed in the baking oven of 110 ℃ and heats 30min, then adds bisphenol A type epoxy resin E51, oleic acid epoxy, polyethylene glycol diglycidyl ether and curing accelerator triethylamine, at 80 Continue stirring at ℃ for 30 minutes, and cool to room temperature to obtain component A of the bio-based epoxy asphalt composite material.
[0019] Step 2: Mix the prepared component A and component B, stir for 5 minutes at a speed of 500 r / min, and cure at room t...
Embodiment 2
[0023] Medium and low temperature curing bio-based epoxy asphalt composite material is composed of two components A and B, and the proportion of component A is as follows: 25 parts of bisphenol A epoxy resin E44, 25 parts of dimer fatty acid epoxy, three 9.5 parts of methylolpropane triglycidyl ether, 0.5 part of curing accelerator triethanolamine, 40 parts of petroleum pitch; B component is curing agent dimer acid-based polyamide; the mass and number ratio of A component and B component is 100:65.
[0024] Step 1: Petroleum pitch is placed in 110 ℃ baking oven and heat 30min, then add bisphenol A type epoxy resin E44, dimer fatty acid epoxy, trimethylolpropane triglycidyl ether and curing accelerator triethanolamine, in Continue stirring at 80°C for 30 minutes, and cool to room temperature to obtain component A of the bio-based epoxy asphalt composite material.
[0025] Step 2: Mix the prepared component A and component B, stir at a speed of 500r / min for 5min, and cure at 70...
Embodiment 3
[0027] The medium and low temperature curing bio-based epoxy asphalt composite material is composed of two components A and B, and the proportion of component A is as follows: bisphenol A epoxy resin E44 35 parts, polyurethane modified epoxy 14 parts, polyester 5 parts of propylene glycol diglycidyl ether, 1 part of curing accelerator DMP-30, 45 parts of petroleum pitch; component B is curing agent tung oil-based polyamide and polyetheramine D230 (mass fraction ratio is 4:1); group A The ratio of parts by mass to component B is 100:70.
[0028] Step 1: Put petroleum asphalt in an oven at 110°C and heat it for 30 minutes, then add bisphenol A epoxy resin E44, polyurethane modified epoxy, polypropylene glycol diglycidyl ether and curing accelerator DMP-30, at 80°C Continue to stir for 30 minutes, and cool to room temperature to obtain component A of the bio-based epoxy asphalt composite material.
[0029] Step 2: Mix the prepared component A and component B, stir at a speed of ...
PUM
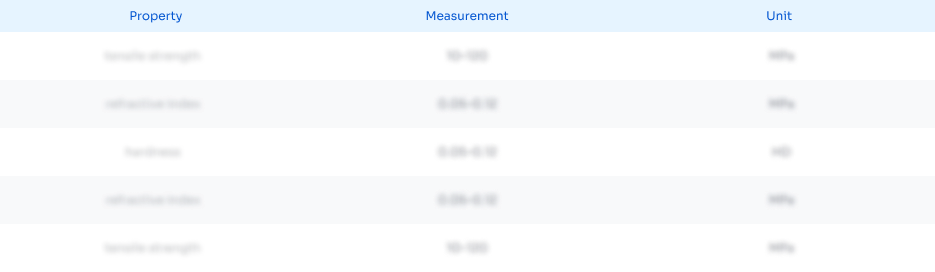
Abstract
Description
Claims
Application Information

- Generate Ideas
- Intellectual Property
- Life Sciences
- Materials
- Tech Scout
- Unparalleled Data Quality
- Higher Quality Content
- 60% Fewer Hallucinations
Browse by: Latest US Patents, China's latest patents, Technical Efficacy Thesaurus, Application Domain, Technology Topic, Popular Technical Reports.
© 2025 PatSnap. All rights reserved.Legal|Privacy policy|Modern Slavery Act Transparency Statement|Sitemap|About US| Contact US: help@patsnap.com