Preparation method of cellulose-based self-reinforcing material
A technology of reinforcing materials and cellulose, which is applied in the field of preparation of cellulose-based self-reinforcing materials, can solve the problems that the anti-ultraviolet aging performance of materials needs to be improved, cellulose cannot realize full shielding in the ultraviolet region, and the anti-ultraviolet aging performance is insufficient, etc., to achieve Excellent UV full shielding performance, excellent anti-ultraviolet aging performance, and the effect of improving anti-ultraviolet aging performance
- Summary
- Abstract
- Description
- Claims
- Application Information
AI Technical Summary
Problems solved by technology
Method used
Image
Examples
Embodiment 1
[0034] (1) Preparation of cellulose ether compounds: Take 10 g of 2% cellulose ionic liquid solution and add it to the reaction flask, and add 0.482g of 1-phenyl-2-propyn-1-one and 0.045g of dimethylaminopyridine (DMAP) were stirred at room temperature for 4 hours to obtain cellulose phenylpropyl ketene ether.
[0035] (2) Preparation and self-reinforcement of cellulose phenylpropyl ketene ether gel: Cast cellulose phenylpropyl ketene ether in the above step (1) into a plastic petri dish, store at 4°C for 3 hours, and finally Deionized water and ethanol washing purification obtained from reinforced cellulose phenylpropenyl ketene ether gel.
[0036] The self-reinforcing cellulose gel can also be obtained by irradiating the cellulose gel obtained above under a 365 nm ultraviolet lamp for 2 hours.
Embodiment 2
[0038] (1) Nanocellulose can be synthesized according to the synthesis method in the open literature (Yu, J. Cellulose 2019, 26(10), 6023-6034).
[0039] After solvent exchange, 0.162 g of nanocellulose (1 mmol AGU) was ultrasonically dispersed in DMF, and then 0.130 g of 1-phenyl-2-propyn-1-one (PPK, 1 mmol) and 0.012 g of dimethylaminopyridine (DMAP , 0.1 mmol) was added to the nanocellulose dispersion, and reacted for 4 hours at room temperature; finally, the nanocellulose phenylpropyl ketene ether (TOCNPPK) was obtained by ethanol washing and purification.
[0040] (2) Preparation and self-reinforcement of nanocellulose phenyl propyl ketene ether film: TOCNPPK film was prepared by solution casting method. Casting 0.4wt% nano-cellulose dispersion liquid into a tetrafluoroethylene mold, drying at 25-80° C. to constant weight, and obtaining a self-reinforced nano-cellulose phenylpropyl ketene ether film.
[0041] The self-reinforced nanocellulose film can also be obtained by...
Embodiment 3
[0044] (1) Nanocellulose phenyl propyl ketene ether (TOCNPPK) was prepared from Example 2.
[0045](2) Preparation and self-reinforcement of nanocellulose phenyl propyl ketene ether film: TOCNPPK film was prepared by solution casting method. The 0.3wt% nano-cellulose dispersion is cast into a tetrafluoroethylene mold, dried at 25-80° C. to constant weight, and the self-reinforced nano-cellulose phenylpropenyl ketene ether film is obtained.
[0046] The cellulose film obtained above can also be exposed to natural light for 2 hours to obtain a self-reinforced nanocellulose film.
PUM
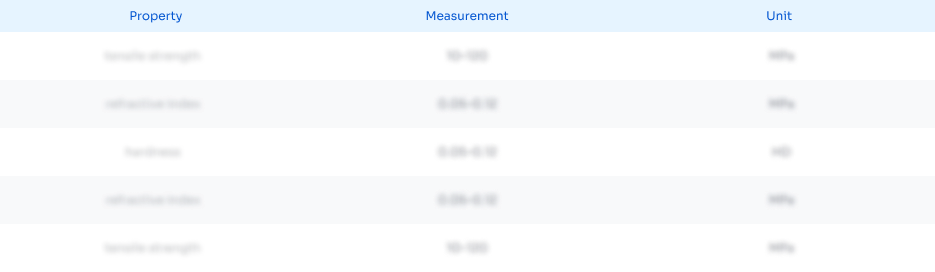
Abstract
Description
Claims
Application Information

- R&D
- Intellectual Property
- Life Sciences
- Materials
- Tech Scout
- Unparalleled Data Quality
- Higher Quality Content
- 60% Fewer Hallucinations
Browse by: Latest US Patents, China's latest patents, Technical Efficacy Thesaurus, Application Domain, Technology Topic, Popular Technical Reports.
© 2025 PatSnap. All rights reserved.Legal|Privacy policy|Modern Slavery Act Transparency Statement|Sitemap|About US| Contact US: help@patsnap.com