Preparation process of environment-friendly plastic particles filled and modified by using starch
A plastic particle and preparation technology, applied in the field of plastic particle processing, can solve the problems of reducing the uniformity of mixing, increasing the difficulty of mixing starch particles and thermoplastic matrix resin, and affecting the quality of plastic particle modification, so as to improve uniformity and improve packaging effect, the effect of improving filling efficiency
- Summary
- Abstract
- Description
- Claims
- Application Information
AI Technical Summary
Problems solved by technology
Method used
Image
Examples
Embodiment 1
[0054] see Figure 1-10 , a preparation process of environmentally friendly plastic particles filled with starch, comprising the steps of:
[0055] S1. Mixing and rounding: the starch is pretreated by mixing equipment, so that the starch is fully wrapped in the thermoplastic matrix resin and made into spherical fillers;
[0056] S2. Heat melting: add thermoplastic matrix resin into the heat melting equipment, and heat melt the thermoplastic matrix resin in advance;
[0057] S3. Auxiliary dispersant: After the thermoplastic matrix resin is melted, add an auxiliary dispersant for mixing;
[0058] S4. Filling: After mixing the auxiliary dispersant for a period of time, add spherical fillers, so that the spherical fillers are fully wrapped by the spherical fillers, and poorly decomposed, so that the starch particles are filled into the thermoplastic matrix resin;
[0059] S5. Flow aid: After mixing the hot-melt thermoplastic matrix resin and the spherical filler, add a flow aid ...
Embodiment 2
[0062] see Figure 1-10 , where the same or corresponding components as those in Embodiment 1 use the corresponding reference numerals as in Embodiment 1, and for the sake of simplicity, only the differences from Embodiment 1 will be described below. The difference between this embodiment 2 and embodiment 1 is: please refer to figure 2 , the steps of mixed circle making are:
[0063] S1. Take a certain proportion of thermoplastic matrix resin and starch to dry;
[0064] S2. Add the dried thermoplastic matrix resin and starch into the mixing equipment, and stir and mix;
[0065] S3. According to the ratio of thermoplastic matrix resin and starch, gelatin is arranged in the mixing equipment;
[0066] S4. When the mixture of thermoplastic matrix resin and starch is pelletized by the mixing equipment, the gelatin is wrapped on the surface of the spherical object to obtain a spherical filler. By using gelatin to wrap dry starch and thermoplastic matrix resin powder into balls,...
Embodiment 3
[0069] see Figure 1-10 , where the same or corresponding components as those in Embodiment 1 use the corresponding reference numerals as in Embodiment 1, and for the sake of simplicity, only the differences from Embodiment 1 will be described below. The difference between this embodiment 3 and embodiment 1 is: please refer to image 3 , the mixing equipment includes an organism 1, the body 1 is divided into a mixing chamber 101 and a ball making chamber 102, the mixing chamber 101 is located on the upper side of the ball making chamber 102, a pair of mixing assemblies 3 are connected in the mixing chamber 101, and a pair of ball making assemblies are connected in the ball making chamber 102 4. Multiple gelatin components 6 are connected to the ball making component 4, please refer to Figure 4-6 The ball making assembly 4 includes a ball making rotating rod 401, the ball making rotating rod 401 is rotatably connected in the ball making chamber 102, the outer end of the ball ...
PUM
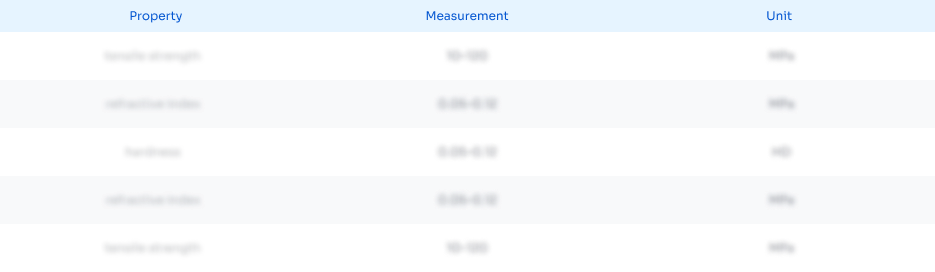
Abstract
Description
Claims
Application Information

- R&D
- Intellectual Property
- Life Sciences
- Materials
- Tech Scout
- Unparalleled Data Quality
- Higher Quality Content
- 60% Fewer Hallucinations
Browse by: Latest US Patents, China's latest patents, Technical Efficacy Thesaurus, Application Domain, Technology Topic, Popular Technical Reports.
© 2025 PatSnap. All rights reserved.Legal|Privacy policy|Modern Slavery Act Transparency Statement|Sitemap|About US| Contact US: help@patsnap.com