Temperature measuring point sleeve device for high-temperature and high-pressure steam pipeline of thermal power plant
A high-temperature, high-pressure, steam pipeline technology, applied to measuring devices, thermometers, thermometer parts, etc., can solve the problem of large differences in chemical composition and thermal expansion coefficient, breakage of stainless steel temperature measuring point casing 3, affecting the safe and stable operation of the unit, etc. problems, to achieve the effect of high rigidity, safety and reliability guarantee, and high reliability
- Summary
- Abstract
- Description
- Claims
- Application Information
AI Technical Summary
Problems solved by technology
Method used
Image
Examples
Embodiment example
[0028] Implementation case: The original opening on the alloy steel pipe 1 is a full-diameter hole. Before installation, the upper part of the original opening of the alloy steel pipe 1 is reamed, and a circular boss with a beveled surface with a thickness of more than 3mm is left at the bottom of the new opening. , the reaming is coaxial with the inner wall of the upper nozzle of the alloy steel temperature measuring point casing 2, and the deviation between the diameter of the upper nozzle of the newly reamed hole and the diameter of the upper nozzle of the alloy steel temperature measuring point casing 2 is less than 1mm; use a tapping machine on the alloy steel pipe The inner wall of the reaming hole of channel 1 is processed with fine-tooth internal threads, and the small-diameter columnar body fine-tooth external threads in the middle of the alloy steel temperature measuring point casing 2 match the processing specifications of the inner wall of the reaming inner wall of t...
PUM
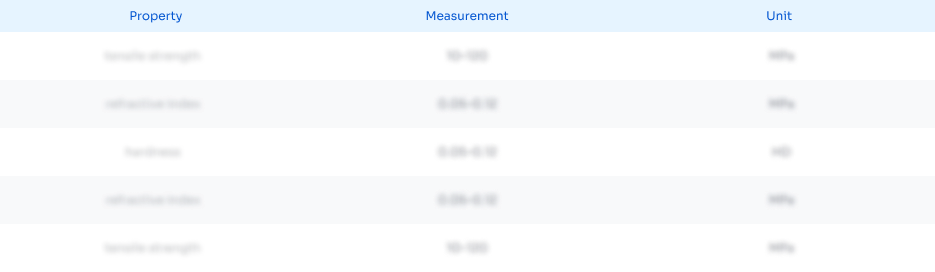
Abstract
Description
Claims
Application Information

- R&D
- Intellectual Property
- Life Sciences
- Materials
- Tech Scout
- Unparalleled Data Quality
- Higher Quality Content
- 60% Fewer Hallucinations
Browse by: Latest US Patents, China's latest patents, Technical Efficacy Thesaurus, Application Domain, Technology Topic, Popular Technical Reports.
© 2025 PatSnap. All rights reserved.Legal|Privacy policy|Modern Slavery Act Transparency Statement|Sitemap|About US| Contact US: help@patsnap.com