Converter repairing material and production method thereof
A technology for repairing materials and converters, which is applied in the field of refractory material production, can solve the problems of restricting promotion and application, reducing converter production efficiency, and long sintering repairing time.
- Summary
- Abstract
- Description
- Claims
- Application Information
AI Technical Summary
Problems solved by technology
Method used
Examples
Embodiment 1
[0031] A converter repair material is prepared from the following raw materials in parts by weight:
[0032] Aggregate: 80 parts of 200 mesh dead burnt magnesia; 25 parts of 1-3mm large crystal fused magnesia, 25 parts of 200 mesh large crystal fused magnesia;
[0033] Ingredients: 3 parts of metal aluminum powder with a particle size of 200 mesh, 3 parts of 180 mesh zirconia powder, 3 parts of 180 mesh magnesium aluminum spinel, 3 parts of calcite powder, 3 parts of potassium feldspar powder, 4 parts of forsterite powder;
[0034] Binder: 5 parts of asphalt, 5 parts of sodium oleate, 5 parts of magnesium trisilicate.
[0035] A method for producing converter repair material, comprising the steps of:
[0036] 1) According to the above weight parts, mix the aggregate dead burnt magnesia, 1-3mm large crystal fused magnesia, and 200 mesh large crystal fused magnesia with a roller mixer for 3-5 minutes, and then add Asphalt, magnesium trisilicate, stirring for more than 30 minut...
Embodiment 2
[0041] A converter repair material is prepared from the following raw materials in parts by weight:
[0042] Aggregate: 85 parts of 200 mesh dead burnt magnesia; 28 parts of 1-3mm large crystal fused magnesia, 28 parts of 200 mesh large crystal fused magnesia;
[0043] Ingredients: 4 parts of metal aluminum powder with particle size of 200 mesh, 4 parts of 180 mesh zirconia powder, 4 parts of 180 mesh magnesium aluminum spinel, 2 parts of calcite powder, 2 parts of potassium feldspar powder, 3 parts of forsterite powder;
[0044] Binder: 6 parts of asphalt, 6 parts of sodium oleate, 6 parts of magnesium trisilicate.
[0045] The production method of a converter repair material is the same as that in Example 1, and the service life of the furnace lining repair in this embodiment is 73 furnaces.
Embodiment 3
[0047] A converter repair material is prepared from the following raw materials in parts by weight:
[0048] Aggregate: 90 parts of 200 mesh dead burnt magnesia; 22 parts of 1-3mm large crystal fused magnesia, 22 parts of 200 mesh large crystal fused magnesia;
[0049] Ingredients: 2 parts of metal aluminum powder with a particle size of 200 mesh, 5 parts of 180 mesh zirconia powder, 5 parts of 180 mesh magnesium aluminum spinel, 2 parts of calcite powder, 4 parts of potassium feldspar powder, and 5 parts of forsterite powder;
[0050] Binder: 8 parts of asphalt, 7 parts of sodium oleate, 11 parts of magnesium trisilicate.
[0051] The production method of a converter repair material is the same as that in Example 1, and the service life of the furnace lining repair in this embodiment is 73 furnaces.
PUM
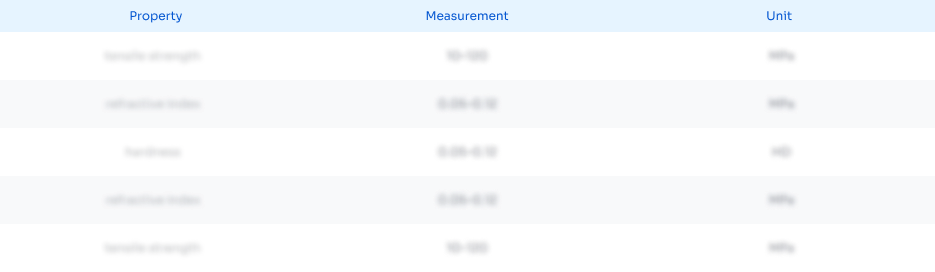
Abstract
Description
Claims
Application Information

- Generate Ideas
- Intellectual Property
- Life Sciences
- Materials
- Tech Scout
- Unparalleled Data Quality
- Higher Quality Content
- 60% Fewer Hallucinations
Browse by: Latest US Patents, China's latest patents, Technical Efficacy Thesaurus, Application Domain, Technology Topic, Popular Technical Reports.
© 2025 PatSnap. All rights reserved.Legal|Privacy policy|Modern Slavery Act Transparency Statement|Sitemap|About US| Contact US: help@patsnap.com