Catalyst for preparing low-carbon olefin from synthesis gas as well as preparation method and application thereof
A low-carbon olefin and catalyst technology, applied in the field of catalyst and its preparation, can solve the problem of low selectivity of low-carbon olefins
- Summary
- Abstract
- Description
- Claims
- Application Information
AI Technical Summary
Problems solved by technology
Method used
Image
Examples
Embodiment 1
[0086] Get 583.8 grams of ferric nitrate, add 1000 g of water to dissolve, obtain material I, get 12.40 grams of cerium nitrate and add 100 g of water to dissolve, obtain material II, get 25.30 grams of manganese nitrate solution that concentration is 50% (w / w), 3.46 grams of nitric acid Put copper and 1.44 g of chromium nitrate in the same container, add 100 g of water, stir and dissolve to obtain material III.
[0087] Mix materials I, II and III to obtain material IV, and use ammonia water to precipitate material IV, wash and separate the precipitate.
[0088] Add 312.5 grams of silica sol with a solid phase mass content of 40% under stirring, then add 50 g of magnesium nitrate solution (containing 0.40 gram of magnesium nitrate), adjust the pH value of the above slurry with ammonia water so that the pH of the mixed slurry=5.0 , The viscosity of the slurry is 35.
[0089] Under the condition of stirring at 70-100°C, add glycerol to adjust the viscosity of the slurry to 200...
Embodiment 2
[0095] Get 525.2 grams of ferric nitrate, add 1000 g of water to dissolve, obtain material I, get 44.70 grams of cerium nitrate and add 200 g of water to dissolve, obtain material II, get 22.80 grams of manganese nitrate solution that concentration is 50% (w / w), 3.11 grams of nitric acid Put copper and 1.30 g of chromium nitrate in the same container, add 100 g of water, stir and dissolve to obtain material III.
[0096] Mix materials I, II and III to obtain material IV, and use ammonia water to precipitate material IV, wash and separate the precipitate.
[0097] Add 312.5 grams of alumina sol with a solid phase mass content of 40% under stirring, then add magnesium nitrate solution 100g (containing 0.30 grams of magnesium nitrate), adjust the acidity of the above-mentioned slurry with ammonia so that the pH of the mixed slurry=4.0, slurry The viscosity of the material is 62.
[0098] Add glucose to adjust the viscosity of the slurry to 320 under the condition of stirring at ...
Embodiment 3
[0104] Get 605.0 grams of ferric nitrate, add 1000 g of water to dissolve, obtain material I, get 0.60 gram of cerium nitrate and add 10 g of water to dissolve, obtain material II, get 26.30 grams of manganese nitrate solution that concentration is 50% (w / w), 3.58 grams of nitric acid Put copper and 1.50 g of chromium nitrate in the same container, add 100 g of water, stir and dissolve to obtain material III.
[0105] Mix materials I, II and III to obtain material IV, and use ammonia water to precipitate material IV, wash and separate the precipitate.
[0106] Add 312.5 grams of silica sol with a solid phase mass content of 40% under stirring, then add 50 g of calcium nitrate solution (containing 0.40 gram of calcium nitrate), adjust the pH value of the above slurry with ammonia water to make the pH of the mixed slurry=5.0 , The viscosity is 36.
[0107] Under the condition of stirring at 70-100° C., add glucose to adjust the viscosity of the slurry to 191.
[0108] After fu...
PUM
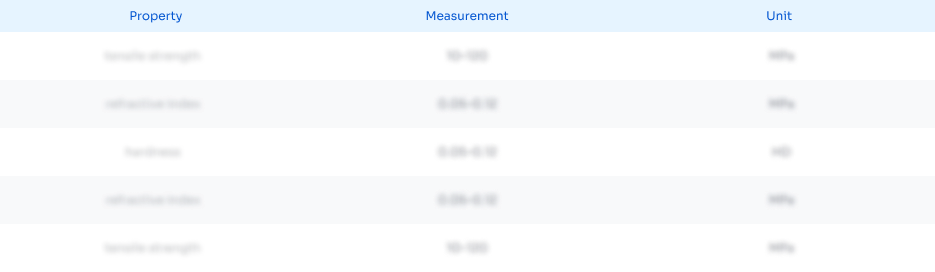
Abstract
Description
Claims
Application Information

- R&D
- Intellectual Property
- Life Sciences
- Materials
- Tech Scout
- Unparalleled Data Quality
- Higher Quality Content
- 60% Fewer Hallucinations
Browse by: Latest US Patents, China's latest patents, Technical Efficacy Thesaurus, Application Domain, Technology Topic, Popular Technical Reports.
© 2025 PatSnap. All rights reserved.Legal|Privacy policy|Modern Slavery Act Transparency Statement|Sitemap|About US| Contact US: help@patsnap.com