Method for aluminizing and chromizing surface of nickel-based high-temperature alloy used on turbine blade or guider
A nickel-based high-temperature alloy and turbine blade technology, applied in metal material coating process, coating, solid-state diffusion coating, etc., can solve the problems of limited corrosion resistance of aluminized coating, unable to guarantee supply, etc., and achieve superior performance , good thermal corrosion resistance effect
- Summary
- Abstract
- Description
- Claims
- Application Information
AI Technical Summary
Problems solved by technology
Method used
Image
Examples
Embodiment 1
[0022]The aluminum chrome method of this embodiment is carried out as follows:
[0023]1, the infiltration configuration, with a mass ratio, the raw material powder, the alumina powder content of 50%, the chrome powder content of 39%, the aluminum powder content of 10%, 1% ammonium chloride; and use a drum type The ball mill grinds the powder ball for 9.5 h to give a mixed bleeding.
[0024]2, pretreatment of bleging agent: calcine the ball after milling, the calcination temperature is controlled at 1100 ° C, and the holding time is controlled at 15.5 h, after the calcination is completed, the chamber is cooled. Then, in the baked bure agent, add a relative raw material total amount of aluminum powder, 1% chromium powder and 0.4% NH.4CL; then bleed at 1030 ° C for 11 h, after the air was burned, the furnace was cooled to give a sample.
[0025]3, parts pretreatment: Totally blow up the part with 200 目 砂, pressure 0.28MPa, after blowing, the blower cleans the surface residual sand, obtains th...
Embodiment 2
[0036]1, the infiltration configuration, with a mass ratio, the raw material powder, the alumina powder content of 50%, the chrome powder content of 44%, the aluminum powder content of 5%, 1% ammonium chloride content; and use roller type The ball mill grinds the powder ball for 9.5 h to give a mixed bleeding.
[0037]2, pretreatment of bleging agent: calcine the ball after milling, the calcination temperature is controlled at 1100 ° C, and the holding time is controlled at 15.5 h, after the calcination is completed, the chamber is cooled. Then, in the baked bure agent, add a relative raw material total amount of aluminum powder, 1% chromium powder and 0.4% NH.4CL; then bleed at 1030 ° C for 11 h, after the air was burned, the furnace was cooled to give a sample.
[0038]3, parts pretreatment: Totally blow up the part with 200 目 砂, pressure 0.28MPa, after blowing, the blower cleans the surface residual sand, obtains the pretreatment parts, the parts in this example are nickel groups. High...
experiment example 2
[0048]The results of the corrosion resistance test of the experimental example 2 and the contraction example 2 are shown in Table 2.
[0049]Table 2
[0050] Example 2 Contrast 2 Corrosion potential -1.32-1.89
[0051]From the experimental results, the corrosion resistance performance of Experimental Example 2 is superior to Comparative Example 2. Further, the diffusion of the permeability layer of the contraction is uneven, and some are crackled.
PUM
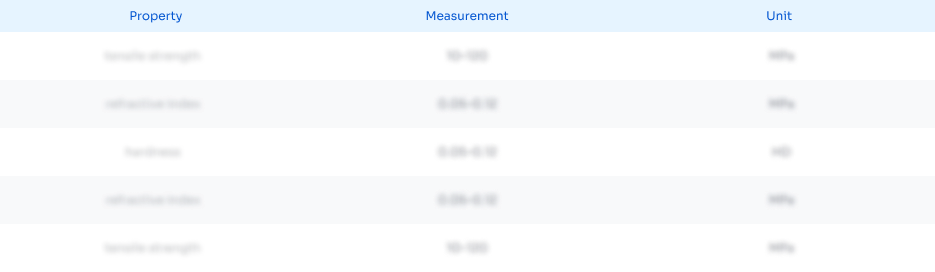
Abstract
Description
Claims
Application Information

- R&D Engineer
- R&D Manager
- IP Professional
- Industry Leading Data Capabilities
- Powerful AI technology
- Patent DNA Extraction
Browse by: Latest US Patents, China's latest patents, Technical Efficacy Thesaurus, Application Domain, Technology Topic, Popular Technical Reports.
© 2024 PatSnap. All rights reserved.Legal|Privacy policy|Modern Slavery Act Transparency Statement|Sitemap|About US| Contact US: help@patsnap.com