High-temperature-resistant inorganic hole sealing agent for thermal spraying coating and preparation method of high-temperature-resistant inorganic hole sealing agent
A thermal spraying, high temperature resistant technology, used in coatings, anti-corrosion coatings, fire-resistant coatings, etc., can solve the problems of poor penetration of the sealing agent, insufficient sealing depth, and poor adhesion, and achieve good UV resistance and resistance. High temperature performance, avoidance of brittle failure, effect of excellent permeability
- Summary
- Abstract
- Description
- Claims
- Application Information
AI Technical Summary
Problems solved by technology
Method used
Image
Examples
preparation example Construction
[0036] The present invention also provides a preparation method of the above-mentioned high-temperature-resistant inorganic sealing agent for thermal spray coating, comprising the following steps:
[0037] Take the formulated amount of inorganic functional sol and rare earth sol, heat to 50~80°C, after the sol is completely dissolved at this temperature, add inorganic film-forming agent, stir evenly, then add stabilizer, and adjust the pH value after fully mixing to 2.5 to 5 to obtain a high temperature resistant inorganic sealing agent for thermal spray coatings.
[0038] The present invention also provides a method for using the above-mentioned high temperature resistant inorganic sealing agent for thermal spray coating, comprising the following steps:
[0039] a. Preheat the thermally sprayed workpiece at 50-60°C for 30-60 minutes, and evenly coat the well-stirred inorganic sealing agent on the surface of the workpiece. The coating method is atmospheric spraying, brushing o...
Embodiment
[0044] Example Preparation of the thermal spray coating of the present invention with high temperature resistant inorganic sealing agent
[0045] The specific operation steps are as follows:
[0046] (1) Preparation of inorganic film-forming agent, weigh 300g phosphoric acid, 80g aluminum hydroxide, 3gB 2 o 3 , magnesium oxide 200g, 465gH 2 O, the reaction generates 1000g colorless translucent solution A;
[0047] (2) Add 500g Al sol, 500g Zr sol, 250g TiO to the container in sequence 2 Sol, 125g lanthanum phosphate sol, 125g yttrium phosphate sol, heated to 50°C, stirred evenly to prepare solution B; slowly added solution A to solution B, and added 125g chromic anhydride, stirred until the solution was evenly dispersed.
[0048] Use the above sealing agent to seal the plasma sprayed Al2O3 ceramic coating, the steps are as follows:
[0049] Step 1. Preheat the thermally sprayed workpiece at 60°C for 30 minutes, and apply the above-mentioned inorganic sealing agent evenly ...
PUM
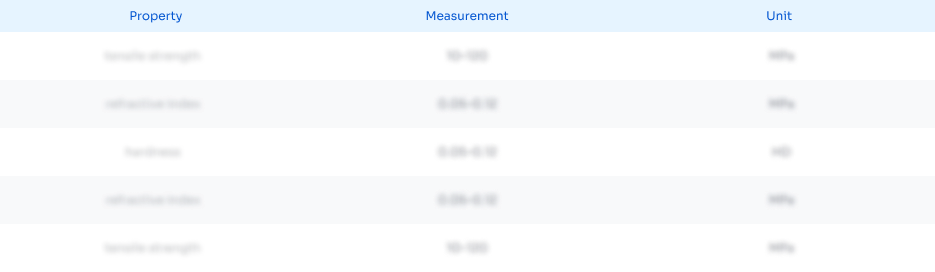
Abstract
Description
Claims
Application Information

- R&D
- Intellectual Property
- Life Sciences
- Materials
- Tech Scout
- Unparalleled Data Quality
- Higher Quality Content
- 60% Fewer Hallucinations
Browse by: Latest US Patents, China's latest patents, Technical Efficacy Thesaurus, Application Domain, Technology Topic, Popular Technical Reports.
© 2025 PatSnap. All rights reserved.Legal|Privacy policy|Modern Slavery Act Transparency Statement|Sitemap|About US| Contact US: help@patsnap.com