Preparation method and application of antibacterial polyethylene master batch
A polyethylene and masterbatch technology, applied in the field of preparation of antibacterial polyethylene masterbatches, can solve the problems of agglomeration, uneven distribution, poor filterability, etc., achieve good filterability and film-forming performance by casting, and inhibit reproduction and spread. Effect
- Summary
- Abstract
- Description
- Claims
- Application Information
AI Technical Summary
Problems solved by technology
Method used
Image
Examples
Embodiment 1
[0031] (1) 50 parts by weight of S16 bacteriostatic agent are fully dispersed in 100 parts by weight of pure water to obtain a dispersion, in which the active ingredients of S16 bacteriostatic agent are separated out in a suspended liquid state;
[0032] (2) Add 0.5 parts by weight of tetrakis[3-(3,5-di-tert-butyl-4-hydroxyphenyl)propionic acid]pentaerythyl ester to the dispersion obtained in step (1), and mix well;
[0033] (3) add 0.3 parts by weight of sodium hydroxide in the material of step (2) gained, mix homogeneously;
[0034] (4) drying the material obtained in step (3) at 100° C. to obtain antibacterial powder;
[0035] (5) 4 parts by weight of the antibacterial powder of step (4) gained and 96 parts by weight of the film-grade polyethylene powder whose melt index center value is 2g / min are dropped into the mixer, and stirred and mixed at a high speed at a speed of 1000rpm for 5min;
[0036] (6) The material obtained in step (5) is sent into a twin-screw extruder fo...
Embodiment 2
[0038] (1)-(4) are the same as embodiment 1.
[0039] (5) 6 parts by weight of the antibacterial powder of step (4) gained and 94 parts by weight of film-grade polyethylene powder whose melt index center value is 2g / min are dropped into the mixer, and stirred and mixed at a high speed at a speed of 1000rpm for 5min;
[0040] (6) The material obtained in step (5) is sent into a twin-screw extruder for melt granulation, the length-to-diameter ratio of the screw of the twin-screw extruder is 40: 1, and the temperature of the melt granulation is 200 ± 3 ℃, the screw speed is 280rpm, the S16 bacteriostatic agent is further uniformly dispersed in polyethylene by shearing and kneading of the twin-screw, then extruded and granulated, and dried to obtain the transparent bacteriostatic polyethylene masterbatch.
Embodiment 3
[0042] (1)-(4) are the same as embodiment 1.
[0043] (5) 8 parts by weight of the antibacterial powder of step (4) gained and 92 parts by weight of the film-grade polyethylene powder whose melt index center value is 2g / min are dropped into the mixer, and stirred and mixed at a high speed at a speed of 1000rpm for 5min;
[0044] (6) The material obtained in step (5) is sent into a twin-screw extruder for melt granulation, the length-to-diameter ratio of the screw of the twin-screw extruder is 40: 1, and the temperature of the melt granulation is 207 ± 3 °C, the screw speed is 250rpm, the S16 bacteriostatic agent is further uniformly dispersed in the polyethylene through the shearing and mixing of the twin-screw, and then extruded and granulated, and dried to obtain the transparent bacteriostatic polyethylene masterbatch.
PUM
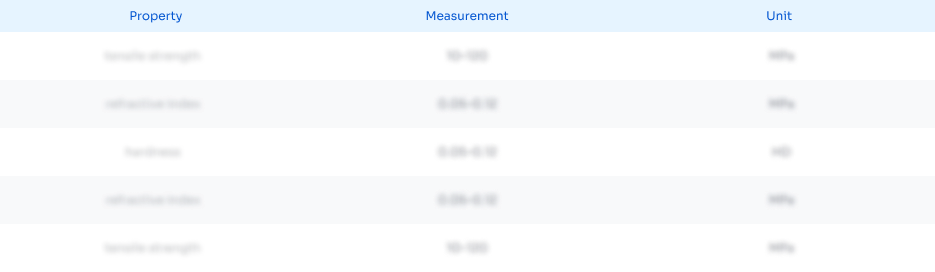
Abstract
Description
Claims
Application Information

- R&D Engineer
- R&D Manager
- IP Professional
- Industry Leading Data Capabilities
- Powerful AI technology
- Patent DNA Extraction
Browse by: Latest US Patents, China's latest patents, Technical Efficacy Thesaurus, Application Domain, Technology Topic, Popular Technical Reports.
© 2024 PatSnap. All rights reserved.Legal|Privacy policy|Modern Slavery Act Transparency Statement|Sitemap|About US| Contact US: help@patsnap.com