Cylindrical lithium-ion battery and its manufacturing process
A manufacturing process and a lithium-ion technology, which are applied in the field of cylindrical lithium-ion batteries and their manufacturing processes, can solve the problems that the high-rate cycle performance of lithium-ion batteries needs to be improved, the rate performance of carbon-based lithium-ion electrode materials is poor, and the like. High rate discharge performance, excellent charge and discharge capacity, and the effect of promoting full dissolution
- Summary
- Abstract
- Description
- Claims
- Application Information
AI Technical Summary
Problems solved by technology
Method used
Image
Examples
Embodiment 1
[0067] The manufacturing process of the cylindrical lithium-ion storage battery of the present embodiment comprises the following steps:
[0068] 1) Preparation of spinning solution
[0069] Prepare the inner layer spinning solution: take 100g of the first solvent tetrahydrofuran, stir at 20°C, then add 12g of polystyrene particles under the stirring condition, and add the polystyrene particles in several times, about 1g each time, each time After the addition, after the polystyrene particles dissolve and disappear, add about 1g of polystyrene particles again until 12g of polystyrene is added, and then stir for 15 minutes to obtain the inner layer spinning solution;
[0070] Preparation of the middle layer spinning solution: Take 80g of the second solvent N,N-dimethylformamide (DMF), add 8g of polyacrylonitrile powder, swell for 20h, and then stir at 85°C for 18h at a speed of 500r / min to obtain Middle layer spinning solution;
[0071]Preparation of the outer layer spinning ...
Embodiment 2
[0086] The difference between the manufacturing process of the cylindrical lithium-ion battery of this embodiment and that of Embodiment 1 is that when preparing the inner layer spinning solution in step 1), 120 g of the first solvent chloroform is taken, stirred at 20° C., and then stirred Add 10g of polystyrene particles under certain conditions, add polystyrene particles several times, add about 1g each time, add about 1g of polystyrene particles after each addition until the polystyrene particles dissolve and disappear, until 10g of polystyrene particles are added polystyrene, and then stirred for 10 minutes to obtain the inner spinning solution. Others are all the same as in Example 1.
Embodiment 3
[0088] The difference between the manufacturing process of the cylindrical lithium-ion battery of this example and Example 1 is that when preparing the inner layer spinning solution in step 1), 1 g of 2-methyl-2- Butyl acrylate monomer and 3 g of styrene-methyl methacrylate copolymer. Others are all the same as in Example 1.
PUM
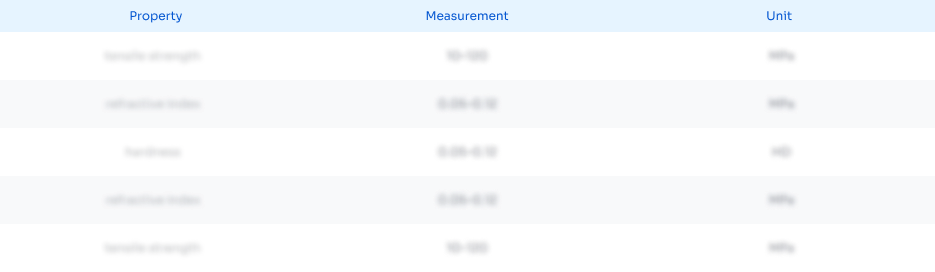
Abstract
Description
Claims
Application Information

- R&D
- Intellectual Property
- Life Sciences
- Materials
- Tech Scout
- Unparalleled Data Quality
- Higher Quality Content
- 60% Fewer Hallucinations
Browse by: Latest US Patents, China's latest patents, Technical Efficacy Thesaurus, Application Domain, Technology Topic, Popular Technical Reports.
© 2025 PatSnap. All rights reserved.Legal|Privacy policy|Modern Slavery Act Transparency Statement|Sitemap|About US| Contact US: help@patsnap.com