Preparation process of ultrathin rock plate
A preparation process and technology for slate, applied in the field of preparation technology of ultra-thin slate, can solve problems such as easy cracking of ultra-thin slate ceramics, improve connectivity and compactness, improve high temperature resistance, and improve compactness Effect
- Summary
- Abstract
- Description
- Claims
- Application Information
AI Technical Summary
Problems solved by technology
Method used
Examples
Embodiment 1
[0025] The invention provides a preparation process of ultra-thin slate, comprising the following steps:
[0026] Step S1: Preparation of raw material powder, putting corundum, quartz, potassium feldspar, albite, and polycrystalline mullite fibers into a ball mill according to the proportion for ball milling;
[0027] Step S2: Powder fabric: after magnetic separation, iron removal and homogenization, then add toughening agent and activator to the powder according to the proportion, dry and spray in a dry sprayer at a temperature of 450°C to form a mixture , and then enter into the distribution machine cloth, wherein by weight fraction, the mixture includes 100 parts of corundum, 15 parts of quartz, 1 part of potassium feldspar, 3 parts of albite feldspar, 5 parts of polycrystalline mullite fiber, toughening agent trioxide 1 part of antimony, 4 parts of ricinoleic acid acyl epoxy resin, 2 parts of activator magnesium oxide powder, 1 part of silicon dioxide powder and 1 part of ...
Embodiment 2
[0035] The invention provides a preparation process of ultra-thin slate, comprising the following steps:
[0036] Step S1: Preparation of raw material powder, putting corundum, quartz, potassium feldspar, albite, and polycrystalline mullite fibers into a ball mill according to the proportion for ball milling;
[0037] Step S2: Powder fabric: after magnetic separation, iron removal and homogenization, then add toughening agent and activator to the powder according to the proportion, dry and spray in a dry sprayer at a temperature of 450°C to form a mixture , and then enter the cloth of the distribution machine, wherein the mixture includes 100 parts of corundum, 20 parts of quartz, 5 parts of potassium feldspar, 5 parts of albite feldspar, 10 parts of polycrystalline mullite fiber, toughening agent trioxide 3 parts of antimony and 5 parts of ricinoleic acid acyl epoxy resin, 5 parts of activator magnesium oxide powder, 2 parts of silicon dioxide powder and 3 parts of cerium oxi...
Embodiment 3
[0045] The invention provides a preparation process of ultra-thin slate, comprising the following steps:
[0046] Step S1: Preparation of raw material powder, putting corundum, quartz, potassium feldspar, albite, and polycrystalline mullite fibers into a ball mill according to the proportion for ball milling;
[0047]Step S2: Powder fabric: after magnetic separation, iron removal and homogenization, then add toughening agent and activator to the powder according to the proportion, dry and spray in a dry sprayer at a temperature of 500°C to form a mixture , and then enter into the distribution machine cloth, wherein the mixture includes 100 parts of corundum, 18 parts of quartz, 3 parts of potassium feldspar, 4 parts of albite feldspar, 8 parts of polycrystalline mullite fiber, toughening agent trioxide 2 parts of antimony and 4.5 parts of ricinoleic acid acyl epoxy resin, 3 parts of activator magnesium oxide powder, 1.5 parts of silicon dioxide powder and 2 parts of cerium oxi...
PUM
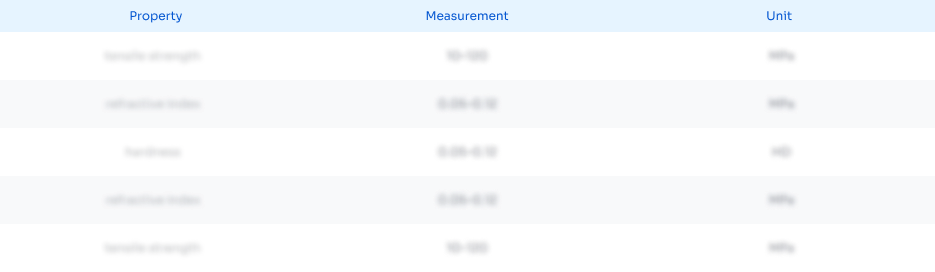
Abstract
Description
Claims
Application Information

- Generate Ideas
- Intellectual Property
- Life Sciences
- Materials
- Tech Scout
- Unparalleled Data Quality
- Higher Quality Content
- 60% Fewer Hallucinations
Browse by: Latest US Patents, China's latest patents, Technical Efficacy Thesaurus, Application Domain, Technology Topic, Popular Technical Reports.
© 2025 PatSnap. All rights reserved.Legal|Privacy policy|Modern Slavery Act Transparency Statement|Sitemap|About US| Contact US: help@patsnap.com