On-line preparation method of steel plate strip with anti-damage corrosion-resistant copper-based coating
An anti-damage and corrosion-resistant technology, which is applied in the direction of coating, metal material coating process, heating inorganic powder coating, etc., to achieve good bonding strength, good corrosion resistance, and overcome the effects of pores
- Summary
- Abstract
- Description
- Claims
- Application Information
AI Technical Summary
Problems solved by technology
Method used
Image
Examples
Embodiment 1
[0034] Example 1 An online preparation method of a damage-resistant and corrosion-resistant copper-based coating for steel strips:
[0035]Steel billet surface cleaning treatment: first use wire brushes, hammers or spatulas to manually derust the surface of the billet, and then use a grinder with a speed of 800 rpm and a No. 23 grinding wheel to electrically remove the surface rust layer.
[0036] Copper powder coating: spray copper powder or brush copper powder to form a certain thickness of copper powder coating on the surface of the billet, and the thickness of the copper powder coating can be controlled within 1mm.
[0037] Billet heating: the steel billet coated with copper-based powder coating was heated in a muffle furnace at a heating temperature of 1150°C for 1 hour.
[0038] Billet rolling: rolling process parameters: rolling speed 1m / s, reduction 20%. figure 2 and image 3 For the present invention, samples are cut along the rolling direction and perpendicular to...
Embodiment 2
[0041] Example 2 An online preparation method of an anti-damage and corrosion-resistant copper-based coating on a steel strip:
[0042] Billet surface cleaning treatment is the same as in Example 1.
[0043] Copper powder coating: spray copper powder or brush copper powder to form a certain thickness of copper powder coating on the surface of the billet, and the thickness of the copper powder coating can be controlled at 5mm.
[0044] Billet heating: the steel billet coated with copper-based powder coating was heated in a muffle furnace at a heating temperature of 1150°C for 1 hour.
[0045] Billet rolling: rolling process parameters: rolling speed 1m / s, reduction 40%. figure 2 and image 3 For the present invention, samples are cut along the rolling direction and perpendicular to the rolling direction (as shown by number 4 in the figure). The copper coating on the steel substrate surface was analyzed by scanning electron microscopy. The prepared copper coating is dense a...
Embodiment 3
[0048] Example 3 An online preparation method of an anti-damage and corrosion-resistant copper-based coating on a steel strip:
[0049] Billet surface cleaning treatment is the same as in Example 1.
[0050] Copper powder coating: spray copper powder or brush copper powder to form a certain thickness of copper powder coating on the surface of the billet, and the thickness of the copper powder coating can be controlled at 5mm, such as figure 1 shown.
[0051] Billet heating: the steel billet coated with copper-based powder coating was heated in a muffle furnace at a heating temperature of 1150°C for 1 hour.
[0052] Billet rolling: rolling process parameters: rolling speed 1m / s, reductions are 25%, 35% and 50% respectively. figure 2 and image 3 For the present invention, samples are cut along the rolling direction and perpendicular to the rolling direction (as shown by serial numbers 2~3, 5 in the figure). The copper coating on the steel substrate surface was analyzed by ...
PUM
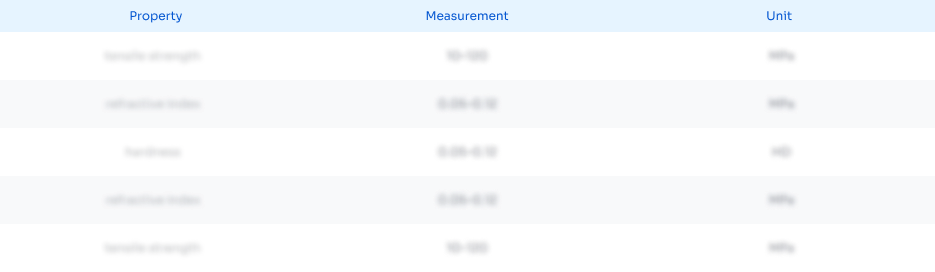
Abstract
Description
Claims
Application Information

- Generate Ideas
- Intellectual Property
- Life Sciences
- Materials
- Tech Scout
- Unparalleled Data Quality
- Higher Quality Content
- 60% Fewer Hallucinations
Browse by: Latest US Patents, China's latest patents, Technical Efficacy Thesaurus, Application Domain, Technology Topic, Popular Technical Reports.
© 2025 PatSnap. All rights reserved.Legal|Privacy policy|Modern Slavery Act Transparency Statement|Sitemap|About US| Contact US: help@patsnap.com