Epoxy modified silicon resin coating and preparation method thereof
A technology of epoxy modification and silicone resin, which is applied in the direction of chemical instruments and methods, coatings, mixers, etc., can solve the problems of fine dispersion of solid materials, poor stirring effect of multi-blade paddles, and influence on the final quality of products, etc., to achieve Improve poor adhesion, solve difficult bonding, and improve construction efficiency
- Summary
- Abstract
- Description
- Claims
- Application Information
AI Technical Summary
Problems solved by technology
Method used
Image
Examples
preparation example Construction
[0029] A preparation method for preparing epoxy-modified silicone resin coating in claim 1, comprising the following steps
[0030] Step (1): preparing the base resin: adding the D monomer, T monomer and silane coupling agent to the multifunctional stirrer in turn, the stirring speed is set to 100r / min, while the stirring is turned on, distilled water and the catalyst are added in turn, After the reaction system releases heat, add solvent, stir and mix evenly, and stand for 12 hours to prepare resin prepolymer, namely base resin;
[0031] Step (2): Preparation of the coating: 100 parts of the base resin prepared in the step (1) and 4 parts of the crosslinking agent are mixed uniformly to obtain a water-based epoxy modified silicone resin coating.
[0032] The multifunctional agitator in the above step (1) includes a shock absorbing base 1, a supporting foot 11, a tank body 12, a sealing hatch 2, a planetary stirring system 3, a feeding system 4, and a bubble eliminating device...
Embodiment 2
[0039]An epoxy-modified silicone resin coating: consisting of a base resin and a crosslinking agent in a mass ratio of 100:5, the base resin comprising the following components in parts by mass: 250 parts D monomer, 250 parts T monomer body, 100 parts of silane coupling agent, 150 parts of distilled water, 10 parts of catalyst, 200 parts of solvent; the D monomer is dimethyldimethoxysilane or dimethyldiethoxysilane, the T monomer is It is methyltrimethoxysilane or methyltriethoxysilane; the silane coupling agent is γ-glycidyl ether oxypropyltrimethoxysilane, and the solvent is prepared from methanol and diacetone alcohol in a mass ratio of 1:3 made;
[0040] A kind of preparation method for preparing epoxy modified silicone resin coating in claim 1, is characterized in that: comprises the following steps
[0041] Step (1): prepare the base resin: add the D monomer, T monomer and silane coupling agent into the multifunctional stirrer in turn, the stirring speed is set to 200r / ...
Embodiment 3
[0045] An epoxy-modified silicone resin coating: consisting of a base resin and a crosslinking agent in a mass ratio of 100:6, the base resin comprising the following components in parts by mass: 400 parts D monomer, 400 parts T monomer body, 150 parts of silane coupling agent, 200 parts of distilled water, 12 parts of catalyst, 250 parts of solvent; the D monomer is dimethyldimethoxysilane or dimethyldiethoxysilane, the T monomer is It is methyltrimethoxysilane or methyltriethoxysilane; the silane coupling agent is γ-glycidyl ether oxypropyltrimethoxysilane, and the solvent is prepared from methanol and diacetone alcohol in a mass ratio of 1:3 made;
[0046] A kind of preparation method for preparing epoxy modified silicone resin coating in claim 1, is characterized in that: comprises the following steps
[0047] Step (1): prepare the base resin: add the D monomer, T monomer and silane coupling agent into the multifunctional stirrer in turn, the stirring speed is set to 300r...
PUM
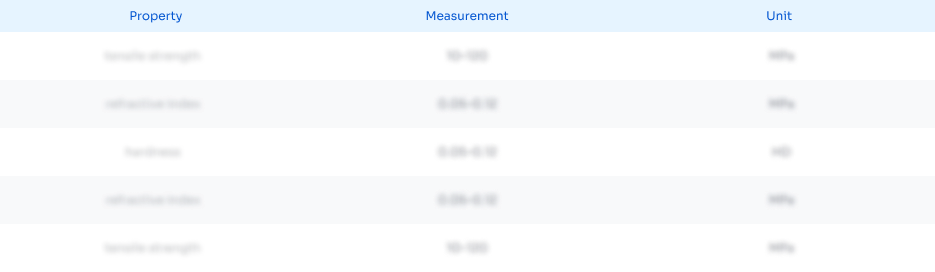
Abstract
Description
Claims
Application Information

- R&D Engineer
- R&D Manager
- IP Professional
- Industry Leading Data Capabilities
- Powerful AI technology
- Patent DNA Extraction
Browse by: Latest US Patents, China's latest patents, Technical Efficacy Thesaurus, Application Domain, Technology Topic, Popular Technical Reports.
© 2024 PatSnap. All rights reserved.Legal|Privacy policy|Modern Slavery Act Transparency Statement|Sitemap|About US| Contact US: help@patsnap.com