Hard organic framework filling material and preparation method thereof
A technology of organic skeleton and filling materials, which is applied in ceramic products, other household utensils, applications, etc., can solve the problems that cannot meet the support strength of filling materials in karst areas, cannot effectively prevent ground subsidence disasters, and destroy groundwater runoff methods, etc., to achieve The construction process is convenient and quick, the effect of solving the loss of slurry, stable and good workability
- Summary
- Abstract
- Description
- Claims
- Application Information
AI Technical Summary
Problems solved by technology
Method used
Image
Examples
preparation example Construction
[0039] A method for preparing a hard organic framework filling material, comprising the steps of:
[0040] 1) Preparation of organic framework materials: Weigh polyanhydride-type materials, polyurethane and phthalic anhydride with a weight ratio of 1:2.0-4.0:1.9-3.5, respectively, and add them to the mixer in turn and stir for 10 minutes until they are evenly mixed, then add the surfactant again After mixing evenly, the mixed material 1 is prepared, and the mixed material 1 is sealed and stored for future use;
[0041] 2) Preparation of foaming material: Weigh polyurethane, trichlorofluoromethane, and silicone foam stabilizer with a weight ratio of 1:2.3-3.5:0.1-0.3, respectively, and add them to the mixer and stir for 5 minutes until they are evenly mixed, then add retarder After mixing evenly again, the mixed material 2 is prepared, and the mixed material 2 is sealed and stored at room temperature for future use;
[0042] 3) Weigh the mixed material 1 and the mixed material...
Embodiment 1
[0045] The organic framework material is made of aromatic polyanhydride, polyurethane and phthalic anhydride in a weight ratio of 1:2:3.0.
[0046] The foaming material is made of isocyanate, trichlorofluoromethane, and silicone foam stabilizer in a weight ratio of 1:3.5:0.2.
[0047] The weight ratio of the organic framework material to the foam material is 1:3.0;
[0048] The surfactant is a sulfonate, and its dosage is 0.001% of the total weight of the filling material.
[0049] The retarder is sodium borate, and its consumption is 0.002% of the total weight of the organic framework filling material.
[0050] The silicone foam stabilizer is made of hydrogen-containing polysiloxane and terminal allyl polyether in a weight ratio of 1:0.6.
[0051] The weight ratio of the rigid organic framework material to the low-boiling foam material is 1:2.7.
[0052] The inorganic perfusion material is made of cement, fine sand, sodium carbonate and water glass in a volume ratio of 1:2...
Embodiment 2
[0056] The organic framework material is made of polyester anhydride, polyurethane and phthalic anhydride in a weight ratio of 1:2.8:2.5.
[0057] The foaming material is made of polyether, trichlorofluoromethane, and silicone foam stabilizer in a weight ratio of 1:2.8:0.2;
[0058] The weight ratio of the hard organic framework material to the low-boiling point foaming material is 1:3.0;
[0059] The surfactant is a sulfonate, and its consumption is 0.002% of the total weight of the filling material;
[0060] The retarder is magnesium sulfate, and its consumption is 0.003% of the total weight of the organic framework filling material;
[0061] The silicone foam stabilizer is made of hydrogen-containing polysiloxane and terminal allyl polyether in a weight ratio of 1:0.8.
[0062] The weight ratio of the rigid organic framework material to the low-boiling point foaming material is 1:3.0.
[0063] The inorganic pouring material is made of cement, fine sand, sodium carbonate ...
PUM
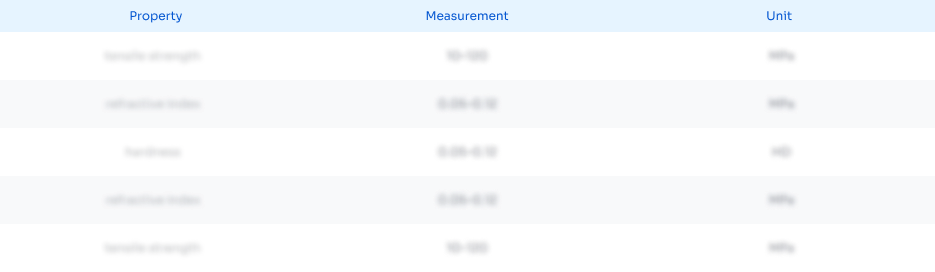
Abstract
Description
Claims
Application Information

- R&D
- Intellectual Property
- Life Sciences
- Materials
- Tech Scout
- Unparalleled Data Quality
- Higher Quality Content
- 60% Fewer Hallucinations
Browse by: Latest US Patents, China's latest patents, Technical Efficacy Thesaurus, Application Domain, Technology Topic, Popular Technical Reports.
© 2025 PatSnap. All rights reserved.Legal|Privacy policy|Modern Slavery Act Transparency Statement|Sitemap|About US| Contact US: help@patsnap.com