Method for producing high-chromium alloy by doping aluminum-magnesium alloy and various rare metals
A rare metal, aluminum-magnesium alloy technology, applied in the field of high-chromium alloy production of high-chromium alloys with mixed ratio of aluminum-magnesium alloys and various rare metals, can solve the problems of unsatisfactory mechanical properties of high-chromium alloys, and achieve fine grains, high hardness and hardness. improved effect
- Summary
- Abstract
- Description
- Claims
- Application Information
AI Technical Summary
Problems solved by technology
Method used
Examples
Embodiment 1
[0041]A method for producing high-chromium alloy by mixing aluminum-magnesium alloy and various rare metals, including the following steps:
[0042]S1: Refine the aluminum-magnesium alloy, rare metals, chromium, silicon, boron and iron by high-energy ball milling to obtain nano-sized powders of various components;
[0043]S2: The chromium and iron powders are mixed in proportions and then melted to melt into molten iron, then sample and analyze the chemical composition, and adjust the carbon content according to the test results;
[0044]S3: Add silicon, boron, and rare metal powder to the liquid phase for melting;
[0045]The order of adding silicon, boron, and rare metal powder is as follows:
[0046]Silicon: After the chemical composition in the furnace is adjusted, the temperature is appropriate, add silicon, and tap the steel within 10-25min after adding;
[0047]Boron: add it just before tapping, and add proper amount of aluminum and titanium to the steel before adding boron;
[0048]Manganese: ad...
Embodiment 2
[0071]A method for producing high-chromium alloy by mixing aluminum-magnesium alloy and various rare metals, including the following steps:
[0072]S1: Refine the aluminum-magnesium alloy, rare metals, chromium, silicon, boron and iron by high-energy ball milling to obtain nano-sized powders of various components;
[0073]S2: The chromium and iron powders are mixed in proportions and then melted to melt into molten iron, then sample and analyze the chemical composition, and adjust the carbon content according to the test results;
[0074]S3: Add silicon, boron, and rare metal powder to the liquid phase for melting;
[0075]The order of adding silicon, boron, and rare metal powder is as follows:
[0076]Silicon: After the chemical composition in the furnace is adjusted, the temperature is appropriate, add silicon, and tap the steel within 10-25min after adding;
[0077]Boron: add it just before tapping, and add proper amount of aluminum and titanium to the steel before adding boron;
[0078]Manganese: ad...
Embodiment 3
[0101]A method for producing high-chromium alloy by mixing aluminum-magnesium alloy and various rare metals, including the following steps:
[0102]S1: Refine the aluminum-magnesium alloy, rare metals, chromium, silicon, boron and iron by high-energy ball milling to obtain nano-sized powders of various components;
[0103]S2: The chromium and iron powders are mixed in proportions and then melted to melt into molten iron, then sample and analyze the chemical composition, and adjust the carbon content according to the test results;
[0104]S3: Add silicon, boron, and rare metal powder to the liquid phase for melting;
[0105]The order of adding silicon, boron, and rare metal powder is as follows:
[0106]Silicon: After the chemical composition in the furnace is adjusted, the temperature is appropriate, add silicon, and tap the steel within 10-25min after adding;
[0107]Boron: add it just before tapping, and add proper amount of aluminum and titanium to the steel before adding boron;
[0108]Manganese: ad...
PUM
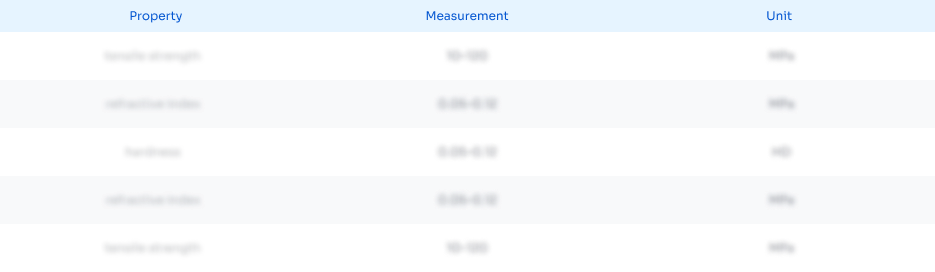
Abstract
Description
Claims
Application Information

- R&D
- Intellectual Property
- Life Sciences
- Materials
- Tech Scout
- Unparalleled Data Quality
- Higher Quality Content
- 60% Fewer Hallucinations
Browse by: Latest US Patents, China's latest patents, Technical Efficacy Thesaurus, Application Domain, Technology Topic, Popular Technical Reports.
© 2025 PatSnap. All rights reserved.Legal|Privacy policy|Modern Slavery Act Transparency Statement|Sitemap|About US| Contact US: help@patsnap.com