Method for efficiently recovering iron ore from gold extraction tailings of oxidized ore containing gold and iron
A technology for iron oxide ore and tailings, which is applied in chemical instruments and methods, high gradient magnetic separation, magnetic separation, etc., can solve the problem that the iron ore particle size is difficult to effectively recover, it is difficult to obtain iron concentrate products, and it cannot offset the dragging of ore pulp. power and other issues, to achieve high commercial use and promotion value, improve comprehensive mineral processing indicators, and achieve the effect of reasonable equipment configuration
- Summary
- Abstract
- Description
- Claims
- Application Information
AI Technical Summary
Problems solved by technology
Method used
Image
Examples
Embodiment 1
[0048] Adopt the present invention to implement the gold and iron oxide ore mechanical stirring cyanide leaching to extract gold tailings, and the technical scheme includes:
[0049] (1) Transport the mechanical agitation and leaching gold extraction tailings of gold-containing and iron oxide ores to be processed to the 1# stirring tank, and adjust the slurry according to the liquid-solid ratio of 2:1. At the same time, add sodium hexametaphosphate to make the slurry in the slurry Mineral particles are well dispersed. The dosage of sodium hexametaphosphate is 450g / t;
[0050] (2) After completing the above steps (1), transport the ore slurry to 1# weak magnetic separator for rough separation of magnetite. The magnetic induction intensity of this operation is 220mT to obtain magnetite rough concentrate and tailings. In this process, a small amount of primary fine-grained magnetite is released by using a lower magnetic induction intensity as the magnetic species for high-gradie...
Embodiment 2
[0059] Adopt the present invention to implement the gold and iron oxide ore mechanical stirring cyanide leaching to extract gold tailings, and the technical scheme includes:
[0060] (1) Transport the mechanical agitation and leaching gold extraction tailings of gold-containing and iron oxide ores to be processed to the 1# stirring tank, and adjust the slurry according to the liquid-solid ratio of 3:1. At the same time, add sodium hexametaphosphate to make the slurry in the slurry Mineral particles are well dispersed. The dosage of sodium hexametaphosphate is 150g / t;
[0061] (2) After completing the above steps (1), transport the pulp to 1# weak magnetic separator for rough separation of magnetite. The magnetic induction intensity of this operation is 160mT to obtain magnetite rough concentrate and tailings. In this process, a small amount of primary fine-grained magnetite is released by using a lower magnetic induction intensity as the magnetic species for high-gradient mag...
Embodiment 3
[0070] Adopt the present invention to implement the gold and iron oxide ore mechanical stirring cyanide leaching to extract gold tailings, and the technical scheme includes:
[0071] (1) Transport the mechanical agitation and leaching gold extraction tailings of gold-containing and iron oxide ores to be processed to the 1# stirring tank, and adjust the slurry according to the liquid-solid ratio of 2:1. At the same time, add sodium hexametaphosphate to make the slurry in the slurry Mineral particles are well dispersed. The dosage of sodium hexametaphosphate is 300g / t;
[0072] (2) After completing the above steps (1), transport the pulp to 1# weak magnetic separator for rough separation of magnetite. The magnetic induction intensity of this operation is 200mT to obtain magnetite rough concentrate and tailings. In this process, a small amount of primary fine-grained magnetite is released by using a lower magnetic induction intensity as the magnetic species for high-gradient mag...
PUM
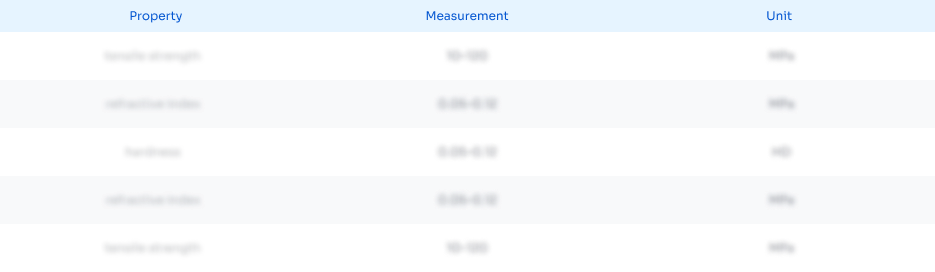
Abstract
Description
Claims
Application Information

- R&D
- Intellectual Property
- Life Sciences
- Materials
- Tech Scout
- Unparalleled Data Quality
- Higher Quality Content
- 60% Fewer Hallucinations
Browse by: Latest US Patents, China's latest patents, Technical Efficacy Thesaurus, Application Domain, Technology Topic, Popular Technical Reports.
© 2025 PatSnap. All rights reserved.Legal|Privacy policy|Modern Slavery Act Transparency Statement|Sitemap|About US| Contact US: help@patsnap.com