Adhesive for diamond lattice dispensing insulation paper and preparation method of adhesive
A technology of insulating paper and adhesives, applied in the direction of adhesives, adhesive types, epoxy resin glue, etc., can solve the problems of transformers, motors, electrical products, hidden dangers in quality, difficulty in meeting the requirements of transformers, and decrease in bonding strength. , to achieve excellent cohesiveness and storage, large market application value, and improved cohesive strength
- Summary
- Abstract
- Description
- Claims
- Application Information
AI Technical Summary
Problems solved by technology
Method used
Image
Examples
preparation example Construction
[0027] A method for preparing an adhesive for rhombic dispensing insulating paper, specifically:
[0028] First start stirring, add a solvent with a mass percentage of 6.2%-7.1% into the reaction kettle, slowly add 2.5%-3.1% curing agent A, stir for 5 minutes, slowly add 8.0%-9.0% epoxy resin A, stir After 10 minutes, turn on the steam to raise the temperature, and turn off the steam when the mixture is heated to 110°C within 20-60 minutes. Under the reflux state, keep the temperature at 110°C-130°C for about 60-90 minutes and then start sampling to measure the molding time. (160±2°C, knife method, 2 grams of sample), if the molding time reaches 9 minutes to 14 minutes (160±2°C, knife method), then turn off the steam and cool down to below 100°C and slowly add a mass percentage of 20%-23 % epoxy resin B, then keep warm at 90-100°C for 30 minutes, after the glue becomes clear, release the vacuum, turn off the steam and cool down to below 60°C, slowly add 11.2%-13% epoxy resin C...
Embodiment 1
[0037] First start stirring, add mass percentage in reaction kettle and be 6.2% xylene, slowly add 2.5% curing agent DDM, slowly add 8.0% E51 epoxy resin after stirring for 5 minutes, turn on steam and heat up after stirring for 10 minutes, When the temperature of the mixed material is raised to 110°C within 20 minutes, close the steam inlet valve, and in the reflux state, keep the temperature at 130°C for about 60 minutes and then start sampling to measure the molding time (160±2°C, knife method, 2 grams of sample), molding The time is 11 minutes, and if the process requirements are met, close the steam inlet valve, lower the temperature of the material below 100°C and slowly add 23% E12 epoxy resin by mass percentage, and then properly open the steam inlet valve to keep the material at 100°C for 30 minutes After the glue solution becomes clear, close the steam inlet valve, cool down to below 60°C and slowly add 11.2% F53 epoxy resin by mass percentage, 1.1% modified amine lat...
Embodiment 2
[0039] First start stirring, add 7.1% solvent butanol in the reaction kettle, slowly add 3.1% curing agent m-phenylenediamine, stir for 5 minutes, slowly add 9.0% EF180 epoxy resin A, stir for 10 minutes Turn on the steam to raise the temperature, raise the temperature of the mixture to 110°C within 60 minutes, then close the steam inlet valve, and in the reflux state, keep the temperature at 120°C for about 60 minutes and start sampling to measure the molding time (160±2°C, knife method, 2 grams of sample), the molding time is 11 minutes, to meet the process requirements, then close the steam inlet valve, make the temperature of the material drop below 100 ℃ and slowly add 20% E20 epoxy resin by mass percentage, then properly open the steam inlet valve to make the material in Keep warm at 90°C for 30 minutes. After the glue becomes clear, close the steam inlet valve, cool down to below 60°C and slowly add 13% F51 epoxy resin and 1.6% boron trifluoride ethylamine complex Curin...
PUM
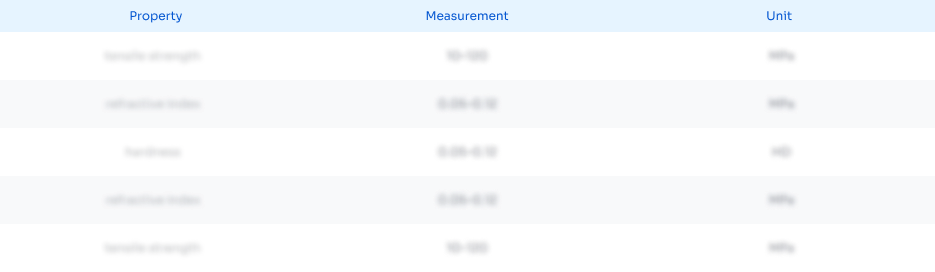
Abstract
Description
Claims
Application Information

- R&D Engineer
- R&D Manager
- IP Professional
- Industry Leading Data Capabilities
- Powerful AI technology
- Patent DNA Extraction
Browse by: Latest US Patents, China's latest patents, Technical Efficacy Thesaurus, Application Domain, Technology Topic, Popular Technical Reports.
© 2024 PatSnap. All rights reserved.Legal|Privacy policy|Modern Slavery Act Transparency Statement|Sitemap|About US| Contact US: help@patsnap.com