Full-process automatic welding wire production line
A full-process, production-line technology, applied in welding media, welding equipment, welding/cutting media/materials, etc., can solve problems such as increased production costs, unfavorable product costs, and cumbersome steps, and achieve equipment footprint reduction and improved The degree of automation and the effect of ensuring product quality
- Summary
- Abstract
- Description
- Claims
- Application Information
AI Technical Summary
Problems solved by technology
Method used
Image
Examples
Embodiment approach
[0040] refer to image 3 As shown, as a preferred embodiment of the present invention, the integrated drawing and pulling machine 130 is a split structure, and the box body 131 has a first frame 133 and a second frame 134 that are plugged into each other. The first frame 133 may be provided with 8 pulling rollers 132 , and the second frame 134 may be provided with 7 pulling rollers 132 .
[0041] The method of setting the integrated drawing machine 130 in a split structure can facilitate the installation, disassembly and transportation of the integrated drawing machine 130 on the one hand, thereby improving the assembly efficiency of the welding wire production line; on the other hand, the integrated drawing machine 130 of the split structure It can be adapted to be set in more scenarios, thereby improving the adaptability of the welding wire production line.
[0042] It should be noted that the integrated drawing and drawing machine 130 in this embodiment can be either a spl...
PUM
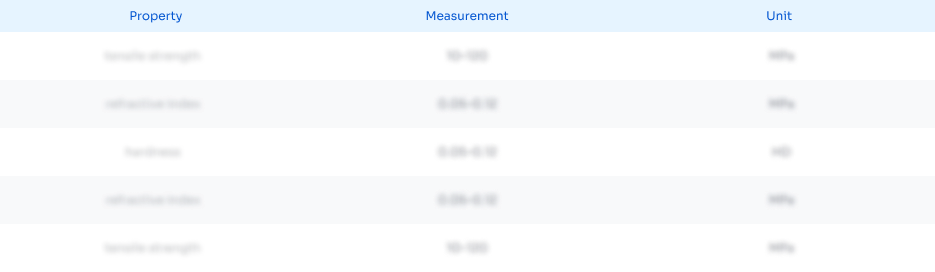
Abstract
Description
Claims
Application Information

- Generate Ideas
- Intellectual Property
- Life Sciences
- Materials
- Tech Scout
- Unparalleled Data Quality
- Higher Quality Content
- 60% Fewer Hallucinations
Browse by: Latest US Patents, China's latest patents, Technical Efficacy Thesaurus, Application Domain, Technology Topic, Popular Technical Reports.
© 2025 PatSnap. All rights reserved.Legal|Privacy policy|Modern Slavery Act Transparency Statement|Sitemap|About US| Contact US: help@patsnap.com