Impurity removal and treatment method in lithium battery scrapped positive electrode material recovery process
A cathode material, lithium battery technology, applied in battery recycling, lithium storage battery, waste collector recycling, etc., can solve problems such as lithium ion poisoning, affecting the stability of co-precipitation process, etc.
- Summary
- Abstract
- Description
- Claims
- Application Information
AI Technical Summary
Problems solved by technology
Method used
Image
Examples
Embodiment 1
[0082] Step 1: At room temperature, add 30 L of lithium battery scrap cathode material leaching solution into the 50 L first reaction kettle.
[0083] Step 2: Use a pH meter to control the peristaltic pump online to pump 2 mol / L lithium hydroxide solution into the first reaction kettle until the pH value is stable at 5.5, stop pumping the lithium hydroxide solution, and allow the mixture to react for 1 hour. The reaction consumed a total of 4.2 L of lithium hydroxide solution.
[0084]Step 3: filter the reacted mixture with a filter press of 200 mesh filter cloths, and use 0.6 MPa high-pressure air to blow-wash the filter cake until no filtrate flows out. During the filtration process, if the internal pressure of the filter press rises rapidly, for example, when it rises to the pressure upper limit of 0.5MPa within 2 minutes, the filtration needs to be stopped, indicating that the filterability of the precipitate is poor. Wait until the pressure drops to 0MPa, and then contin...
Embodiment 2
[0089] Step 1: Add 10 L of the filtrate in Example 1 to the 50 L first reaction kettle as the first bottom liquid, so that the electrode of the pH meter is located below the liquid level, and heat the first reaction kettle to keep the reaction temperature at 70°C.
[0090] Step 2: Use a peristaltic pump to pump the leaching solution of the scrapped positive electrode material of the lithium battery and the 2 mol / L lithium hydroxide solution into the first reaction kettle respectively. The pumping speed of lithium battery scrap cathode material leaching liquid is controlled at 200 ml / min, and the pumping speed of lithium hydroxide is controlled by an online pH meter, and the pumping speed of lithium hydroxide is controlled so that the pH of the mixture is 5.5. After fully reacting for 3 h, the mixture overflowed from the overflow port of the first reaction kettle and entered the first aging kettle. During this process, a total of 36 L of lithium battery scrap positive electrode...
Embodiment 3
[0132] Step 1: Add 10L of deionized water and 300mL of 23.5% ammonia water into the 50L second reaction kettle as the second bottom liquid, maintain the reaction temperature at 50°C, and pass nitrogen gas as the protective gas.
[0133] Step 2: The first filtrate obtained in Example 2 was pumped into the second reactor at a flow rate of 60 mL / min, and 12% ammonia water was pumped into the second reactor at a flow rate of 5 mL / min. Use a pH meter to control the flow rate of the pumped 4mol / L lithium hydroxide solution in real time, and control the flow rate of the lithium hydroxide solution so that the pH of the mixture is between 10.7-11.2. After fully reacting for 5 hours, the mixture overflowed from the overflow port of the second reaction kettle and flowed into the second aging kettle.
[0134] Step 3: heating the second aging tank to keep the aging temperature at 50° C., and aging the mixture in the second aging tank for 1 h.
[0135] Step 4: filter the aged mixture with ...
PUM
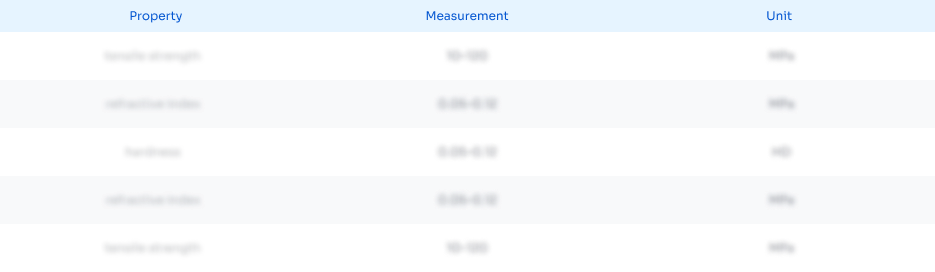
Abstract
Description
Claims
Application Information

- Generate Ideas
- Intellectual Property
- Life Sciences
- Materials
- Tech Scout
- Unparalleled Data Quality
- Higher Quality Content
- 60% Fewer Hallucinations
Browse by: Latest US Patents, China's latest patents, Technical Efficacy Thesaurus, Application Domain, Technology Topic, Popular Technical Reports.
© 2025 PatSnap. All rights reserved.Legal|Privacy policy|Modern Slavery Act Transparency Statement|Sitemap|About US| Contact US: help@patsnap.com