Biomass composite ammonium polyphosphate intumescent flame retardant, preparation method and application thereof
A technology for compounding ammonium polyphosphate and intumescent flame retardant, applied in the field of composite materials, can solve the problems of insufficient flame retardant efficiency, poor water resistance of intumescent flame retardant, etc., and achieve excellent carbon residue rate, high flame retardant efficiency, and low hygroscopicity. Effect
- Summary
- Abstract
- Description
- Claims
- Application Information
AI Technical Summary
Problems solved by technology
Method used
Image
Examples
preparation example Construction
[0036] The preparation method of above-mentioned biomass composite ammonium polyphosphate expansion flame retardant specifically comprises the following steps:
[0037] Step 1, weighing 65-85 parts of ammonium polyphosphate, 10.5-28 parts of starch derivatives and 4-7 parts of biomass;
[0038] Step 2. Add the starch derivative weighed in step 1 into deionized water, stir at room temperature to disperse the starch derivative evenly, obtain a starch dispersion with a mass percentage concentration of 3-12wt%, and heat the starch dispersion to 70- 130°C, and stir at constant temperature for 0.5-3h until starch gelatinization, after cooling down to 30-60°C, starch paste liquid is obtained;
[0039] Step 3, adding the biomass weighed in step 1 into deionized water, stirring at room temperature to dissolve the biomass, and obtaining a biomass solution with a mass percentage concentration of 2-7wt%;
[0040] Step 4. Disperse the ammonium polyphosphate weighed in step 1 in deionized ...
Embodiment 1
[0046] Step 1, weighing 70 parts of ammonium polyphosphate, 17 parts of starch phosphate and 6.5 parts of hyaluronic acid;
[0047] Step 2. Add the starch phosphate ester weighed in step 1 into deionized water, stir at room temperature to disperse the starch phosphate ester evenly, obtain a starch dispersion with a mass percentage concentration of 5wt%, and heat the starch dispersion to 80° C., and Stir at constant temperature for 2.5 hours until the starch is gelatinized, and after cooling down to 40°C, the starch paste liquid is obtained;
[0048] Step 3, adding the hyaluronic acid weighed in the step 1 into deionized water, stirring at room temperature to dissolve the hyaluronic acid, and obtaining a biomass solution with a mass percent concentration of 4 wt %;
[0049] Step 4. Disperse the ammonium polyphosphate weighed in step 1 in deionized water to obtain an ammonium polyphosphate dispersion with a mass percent concentration of 40 wt%, and add the starch paste obtained ...
Embodiment 2
[0053] Step 1, weighing 80 parts of ammonium polyphosphate, 15 parts of starch phosphate and 5 parts of sodium alginate;
[0054] Step 2. Add the starch phosphate weighed in step 1 into deionized water, stir at room temperature to disperse the starch phosphate evenly, obtain a starch dispersion with a mass percentage concentration of 8wt%, and heat the starch dispersion to 130° C., and Stir at constant temperature for 1 hour until the starch is gelatinized, and after cooling down to 50°C, the starch paste liquid is obtained;
[0055] Step 3, adding the sodium alginate weighed in step 1 into deionized water, stirring at room temperature to dissolve the sodium alginate to obtain a biomass solution with a concentration of 6 wt% by mass;
[0056] Step 4. Disperse the ammonium polyphosphate weighed in step 1 in deionized water to obtain an ammonium polyphosphate dispersion with a mass percent concentration of 40 wt%, and add the starch paste obtained in step 2 to the ammonium polyp...
PUM
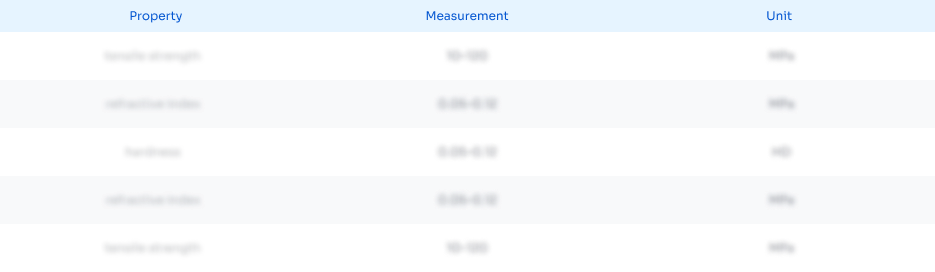
Abstract
Description
Claims
Application Information

- R&D
- Intellectual Property
- Life Sciences
- Materials
- Tech Scout
- Unparalleled Data Quality
- Higher Quality Content
- 60% Fewer Hallucinations
Browse by: Latest US Patents, China's latest patents, Technical Efficacy Thesaurus, Application Domain, Technology Topic, Popular Technical Reports.
© 2025 PatSnap. All rights reserved.Legal|Privacy policy|Modern Slavery Act Transparency Statement|Sitemap|About US| Contact US: help@patsnap.com