Method for recovering vanadium, aluminum and molybdenum from waste catalyst
A waste catalyst, vanadium-aluminum technology, applied in the field of recovering vanadium-aluminum-molybdenum, can solve the problems of high energy consumption, serious dust, long reaction time, etc., and achieve the effects of high extraction rate, strong oxidization, and high purity
- Summary
- Abstract
- Description
- Claims
- Application Information
AI Technical Summary
Problems solved by technology
Method used
Examples
Embodiment 1
[0058] The present embodiment provides a method for recovering vanadium-aluminum-molybdenum from spent catalysts, said method comprising the steps of:
[0059] (1) mix the spent catalyst containing vanadium, aluminum and molybdenum with the sodium hydroxide solution whose mass concentration is 20wt% by liquid-solid ratio 3:1, obtain reaction slurry; Contain vanadium, aluminum and molybdenum in the described spent catalyst; The waste catalyst is a waste hydrodesulfurization (HDS) aluminum-based petroleum catalyst, composed of V 2 o 5 : 10.51wt%, Al 2 o 3 : 22.15wt%, MoO 3 : 2.96wt%, NiO: 2.94wt%;
[0060] (2) The reaction slurry described in step (1) is placed in a reactor, and the reactor is equipped with a conventional down-pressing mechanical stirring paddle and an aerator, wherein the aerator is composed of a motor, a hollow stirring shaft and a hollow impeller;
[0061] The impeller of the aerator is located below the stirring paddle of the reactor, the diameter of th...
Embodiment 2
[0064] The present embodiment provides a method for recovering vanadium-aluminum-molybdenum from spent catalysts, said method comprising the steps of:
[0065] (1) mix the spent catalyst containing vanadium, aluminum and molybdenum with the sodium hydroxide solution whose mass concentration is 25wt% by liquid-solid ratio 4:1, obtain reaction slurry; Contain vanadium, aluminum and molybdenum in the described spent catalyst; The waste catalyst is a waste hydrodesulfurization (HDS) aluminum-based petroleum catalyst, composed of V 2 o 5 : 8.32wt%, Al 2 o 3 : 25.22wt%, MoO 3 : 3.07wt%, NiO: 2.35wt%;
[0066] (2) The reaction slurry described in step (1) is placed in a reactor, and the reactor is equipped with a conventional down-pressing mechanical stirring paddle and an aerator, wherein the aerator is composed of a motor, a hollow stirring shaft and a hollow impeller;
[0067] The impeller of the aerator is located below the stirring paddle of the reactor, the diameter of the...
Embodiment 3
[0070] The present embodiment provides a method for recovering vanadium-aluminum-molybdenum from spent catalysts, said method comprising the steps of:
[0071] (1) mix the spent catalyst containing vanadium, aluminum and molybdenum with the sodium hydroxide solution whose mass concentration is 30wt% according to the liquid-solid ratio of 5:1 to obtain a reaction slurry; the spent catalyst contains vanadium, aluminum and molybdenum; The waste catalyst is a waste hydrodesulfurization (HDS) aluminum-based petroleum catalyst, composed of V 2 o5 : 9.76%, Al 2 o 3 : 20.21%, MoO 3 : 2.32%, NiO: 3.23%;
[0072] (2) The reaction slurry described in step (1) is placed in a reactor, and the reactor is equipped with a conventional down-pressing mechanical stirring paddle and an aerator, wherein the aerator is composed of a motor, a hollow stirring shaft and a hollow impeller;
[0073] The impeller of the aerator is located under the stirring paddle of the reactor, the diameter of the ...
PUM
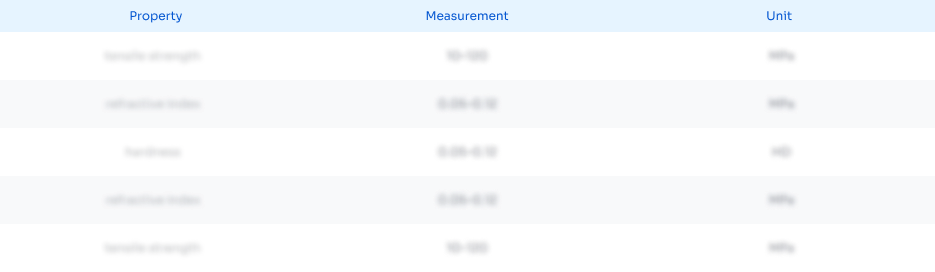
Abstract
Description
Claims
Application Information

- R&D
- Intellectual Property
- Life Sciences
- Materials
- Tech Scout
- Unparalleled Data Quality
- Higher Quality Content
- 60% Fewer Hallucinations
Browse by: Latest US Patents, China's latest patents, Technical Efficacy Thesaurus, Application Domain, Technology Topic, Popular Technical Reports.
© 2025 PatSnap. All rights reserved.Legal|Privacy policy|Modern Slavery Act Transparency Statement|Sitemap|About US| Contact US: help@patsnap.com