Method for preparing combustible gas through co-pyrolysis of sludge and biomass
A biomass and co-pyrolysis technology, which is applied in the preparation of biofuels, liquid hydrocarbon mixtures, gas fuels, etc., can solve the problems of large co-pyrolysis effects and different synergistic effects, and achieve the effect of increasing thermal mass loss rate
- Summary
- Abstract
- Description
- Claims
- Application Information
AI Technical Summary
Problems solved by technology
Method used
Image
Examples
Embodiment 1
[0027] Embodiment 1 thermogravimetric experiment analysis synergistic effect
[0028] In order to explore the synergistic effect of co-pyrolysis of sludge and wood powder, the TG and DTG curves of sludge and wood powder alone are as follows figure 1 shown.
[0029] On this basis, the blending ratio and the respective TG / DTG were calculated theoretically in a weighted form, and the theoretical TG / DTG curve of the mixed sample was obtained. Because the theoretical calculation is based on the linear superposition assumption that the co-pyrolysis process is regarded as a single raw material pyrolysis, that is, there is no interaction between sludge and wood powder, so when the calculation results are basically consistent with the experimental results, it means that there is no interaction between the two. obvious interaction. In this study, the calculated TG / DTG curve was compared with the experimental TG / DTG curve. The results are as follows: figure 2 shown.
[0030] It can ...
Embodiment 2
[0031] The influence of embodiment 2 different wood flour mixing ratios on the three-phase yield
[0032] The pyrolysis temperature was set at 900°C, and the effect of the wood flour blending ratio on the yield of the three-phase product of co-pyrolysis of sludge and wood flour was investigated. The results are as follows image 3 shown.
[0033] Depend on image 3 It can be seen that: when the wood flour blending ratio increases from 0 to 100wt.%, the gas yield increases from 3.29% to 26.06%, the tar yield increases from 11.61% to 51.80%, while the solid yield decreases from 85.09% to 22.14%. This can be explained by the fact that wood flour has a relatively high volatile content and low ash content, adding to the sludge improved the gas yield during the co-pyrolysis process. In order to evaluate possible synergistic effects during the co-pyrolysis process, the experimental and theoretically calculated yields of each phase at different wood flour blending ratios were compa...
Embodiment 3
[0039] The influence of embodiment 3 different wood flour blending ratios on gas products
[0040] In the process of co-pyrolysis of sludge and wood flour, the raw material first undergoes a pyrolysis reaction to generate steam, biochar, non-condensable gas and tar (1). Then the secondary pyrolysis reaction occurs, that is, the primary pyrolysis reaction of tar (2), the non-condensable gas C 3 h 8 、C 2 h 6 、C 2 h 4 Reactions such as chain scission and dehydrogenation occur (3)(4)(5). This process will form an atmosphere rich in steam, under this atmosphere, gas-solid phase reactions will occur, such as boudouard reaction (6), water gas reaction (7) (8), and gas phase reactions will also occur, such as reverse water gas Shift reactions (10), methane and hydrocarbon steam reforming reactions (11) (12). Co-pyrolysis of final gas components depends on a series of complex and competing reactions.
[0041] A pyrolysis reaction:
[0042]
[0043] Secondary pyrolysis reactio...
PUM
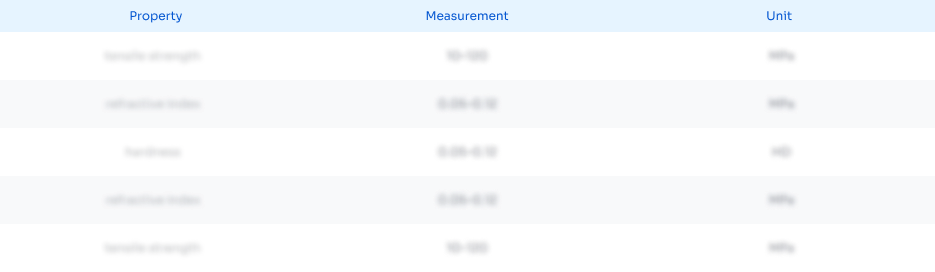
Abstract
Description
Claims
Application Information

- Generate Ideas
- Intellectual Property
- Life Sciences
- Materials
- Tech Scout
- Unparalleled Data Quality
- Higher Quality Content
- 60% Fewer Hallucinations
Browse by: Latest US Patents, China's latest patents, Technical Efficacy Thesaurus, Application Domain, Technology Topic, Popular Technical Reports.
© 2025 PatSnap. All rights reserved.Legal|Privacy policy|Modern Slavery Act Transparency Statement|Sitemap|About US| Contact US: help@patsnap.com