Comprehensive treatment process of conversion condensate
A comprehensive treatment and condensate technology, applied in the field of coal chemical industry, can solve the problems of blocked pipes, low ammonia content, high sulfur content in ammonia water, etc.
- Summary
- Abstract
- Description
- Claims
- Application Information
AI Technical Summary
Problems solved by technology
Method used
Image
Examples
Embodiment 1
[0036] The comprehensive treatment process of transforming condensate in a chemical plant in Shanxi is as attached figure 1 As shown, its process includes the following steps:
[0037] Step 1: Transformation condensate comes from the liquid phase of the four separators in the conversion section, which are divided into two, three, five and six. First, after heat exchange, it is sent to the atmospheric stripping tower 1, and the steam is heated and stripped to maintain the pressure. 0.3MPa, the temperature at the bottom of the tower is 135°C, the liquid phase containing a small amount of ammonia at the bottom of the stripping tower is sent to gasification for reuse, and the gas phase at the top of the tower passes through the raw material water-atmospheric pressure stripping tower top gas heat exchanger 2. Atmospheric pressure stripping tower top After the cooler 3 is cooled, the liquid separation tank 4 at the top of the atmospheric stripping tower is separated, the gas phase o...
Embodiment 2
[0048] The comprehensive treatment process for transforming condensate in a chemical plant in Shandong is as attached figure 1 As shown, the shift condensate is first sent to the atmospheric stripping tower 1 after heat exchange, and is stripped by steam heating. The vaporized high-flash gas enters the middle and lower part of the deammonization tower as the stripping gas of the deammonization tower, and the pressure is maintained at 0.4MPa. The temperature at the bottom of the tower is 145°C, and the liquid phase containing a small amount of ammonia in the bottom of the stripping tower is sent to gasification for reuse, and the gas phase at the top of the tower passes through raw water-atmospheric pressure stripping tower top gas heat exchanger 2, atmospheric stripping tower top cooler 3 After cooling, the liquid separation tank 4 at the top of the atmospheric stripping tower is separated, the gas phase of the liquid separation tank is sent to the water washing tower 5, and th...
PUM
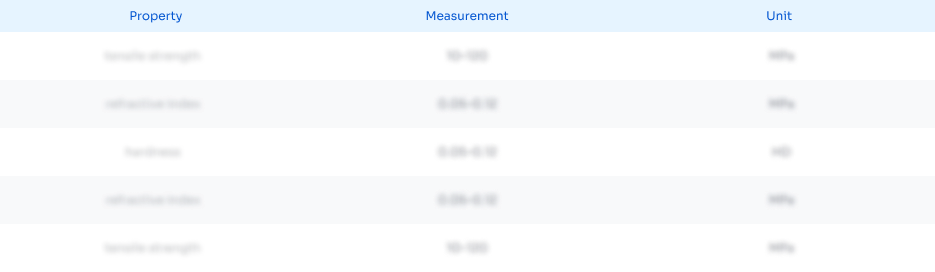
Abstract
Description
Claims
Application Information

- Generate Ideas
- Intellectual Property
- Life Sciences
- Materials
- Tech Scout
- Unparalleled Data Quality
- Higher Quality Content
- 60% Fewer Hallucinations
Browse by: Latest US Patents, China's latest patents, Technical Efficacy Thesaurus, Application Domain, Technology Topic, Popular Technical Reports.
© 2025 PatSnap. All rights reserved.Legal|Privacy policy|Modern Slavery Act Transparency Statement|Sitemap|About US| Contact US: help@patsnap.com