Catalyst for low-temperature catalytic oxidation of VOCs and preparation method thereof
A low-temperature catalysis and catalyst technology, which is applied in the field of resources and the environment, can solve problems such as chlorine poisoning catalysts, poisoning deactivation, etc., and achieve the effects of enhancing reactivity, inhibiting erosion, and strengthening interactions
- Summary
- Abstract
- Description
- Claims
- Application Information
AI Technical Summary
Problems solved by technology
Method used
Image
Examples
Embodiment 1
[0026] A preparation method of a catalyst for low-temperature catalytic oxidation of VOCs is achieved through the following steps:
[0027] (1) Preparation of mesoporous manganese-zirconium composite oxide
[0028] Stir and mix the manganese acetate solution and the zirconium oxynitrate solution at room temperature for 10 minutes, add urea and PVP and continue to stir for 25 minutes, then treat the resulting mixed solution at 85°C for 24 hours, then centrifuge, wash, and dry in sequence, and then place at 350 ℃ roasting for 6h to obtain mesoporous manganese-zirconium composite oxide; the ratio of the amount of manganese acetate and zirconyl nitrate is 0.5:1, and the amount of urea added is 10% of the total amount of manganese acetate and zirconyl nitrate times, the addition of the PVP is 4 wt% of the total mass of manganese acetate and zirconyl nitrate, the concentration of the manganese acetate solution is 0.15mol / L manganese acetate solution, and the concentration of the zir...
Embodiment 2
[0037] A method for preparing a catalyst for low-temperature catalytic oxidation of VOCs is achieved through the following steps:
[0038] (1) Preparation of mesoporous manganese-zirconium composite oxide
[0039] Stir and mix the manganese acetate solution and the zirconium oxynitrate solution at room temperature for 20 minutes, add urea and PVP and continue to stir for 35 minutes, then treat the resulting mixed solution at 95°C for 12 hours, then centrifuge, wash, and dry in sequence, and then place it at 450 ℃ roasting for 3h to obtain mesoporous manganese-zirconium composite oxide; the ratio of the amount of manganese acetate and zirconyl nitrate is 2:1, and the amount of urea added is 15% of the total amount of manganese acetate and zirconyl nitrate. times, the addition of the PVP is 6wt% of the total mass of manganese acetate and zirconyl nitrate; the concentration of the manganese acetate solution is 0.3 mol / L, and the concentration of the zirconyl nitrate solution is 0...
Embodiment 3
[0048] A method for preparing a catalyst for low-temperature catalytic oxidation of VOCs is achieved through the following steps:
[0049] (1) Preparation of mesoporous manganese-zirconium composite oxide
[0050] Stir the manganese acetate solution and the zirconium oxynitrate solution at room temperature for 15 min, add urea and PVP and continue stirring for 30 min, then treat the resulting mixed solution at 90 °C for 18 h, then centrifuge, wash, and dry in sequence, and then Roasting at 400°C for 5 h to obtain a mesoporous manganese-zirconium composite oxide; the ratio of the amount of manganese acetate to zirconyl nitrate is 1:1, and the amount of urea added is the total amount of manganese acetate and zirconyl nitrate 13 times of the amount, the addition of the PVP is 5wt% of the total mass of manganese acetate and zirconyl nitrate, the concentration of the manganese acetate solution is 0.2 mol / L, and the concentration of the zirconyl nitrate solution is 0.2 mol / L ;
[...
PUM
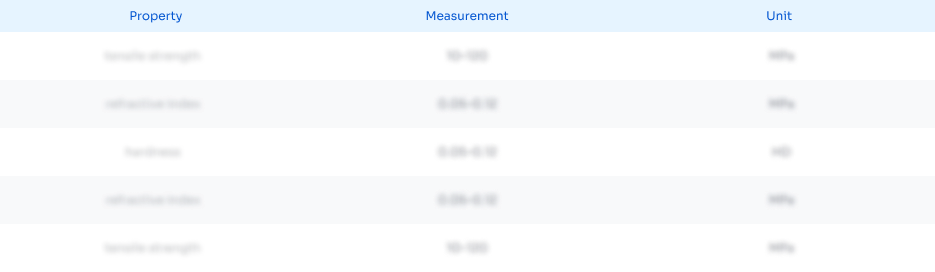
Abstract
Description
Claims
Application Information

- Generate Ideas
- Intellectual Property
- Life Sciences
- Materials
- Tech Scout
- Unparalleled Data Quality
- Higher Quality Content
- 60% Fewer Hallucinations
Browse by: Latest US Patents, China's latest patents, Technical Efficacy Thesaurus, Application Domain, Technology Topic, Popular Technical Reports.
© 2025 PatSnap. All rights reserved.Legal|Privacy policy|Modern Slavery Act Transparency Statement|Sitemap|About US| Contact US: help@patsnap.com