Filled plant fiber, preparation method thereof, and high-strength plastic wave-absorbing concrete
A plant fiber, filling technology, applied in the field of composite materials, can solve the problems affecting the durability of concrete, the decrease of fiber breaking strength, chlorine resistance, crack resistance and poor load-bearing capacity, so as to avoid the decrease of breaking strength and maintain the breaking strength. , to ensure the effect of adhesion
- Summary
- Abstract
- Description
- Claims
- Application Information
AI Technical Summary
Problems solved by technology
Method used
Image
Examples
preparation example Construction
[0026] The invention provides a preparation method of filling plant fiber, which comprises the following steps: after soaking the plant fiber in an alkali-resistant filler dispersion liquid, taking it out for cooling, drying and cutting to obtain the filling plant fiber. The alkali-resistant filler solution is poured into the inner cavity of the plant fiber, and then the bonding force between the alkali-resistant filler and the inner cavity of the plant fiber is accelerated under cooling and drying procedures. Since the plant fiber is a long section of fiber, the fiber is cut into short-cut fiber, which is conducive to improving the bonding force between the filling fiber and the cement-based cementitious material, and improving the strength of the concrete. It should be noted that it has been verified by experiments that during the process of soaking the plant fibers in the alkali-resistant filler dispersion, due to the capillary phenomenon inside the fibers, the alkali-resist...
Embodiment 1
[0037] The utility model relates to a filling plant fiber, which uses a hollow tubular plant fiber as a wall material and an alkali-resistant filler as a core material. Hollow tubular plant fibers can be selected from A: sisal fiber, B: ramie fiber, C: bamboo fiber, D: palm fiber, E: coconut shell fiber; alkali-resistant fillers can be selected from a: styrene-acrylic emulsion, b: bentonite, c : silica fume, d: polyethylene acetate, e: styrene-acrylic emulsion and epoxy resin, f: fly ash; g: silica fume; its preparation method is that the plant fiber is put into a 50% resistant After soaking in the alkaline filler dispersion, the ratio of solid to liquid is 1:6, the soaking time is 50min, and the soaking temperature is 30°C. After natural cooling at room temperature, put it in a hot air drying oven to dry, and then cut into 10mm chopped fibers.
Embodiment 2
[0039] A high-strength plastic wave-absorbing concrete, the components are calculated by weight ratio, including: 35 parts of filled plant fibers prepared in Example 1, 275 parts of low-heat cement, 135 parts of fly ash, and 25 parts of calcium sulfoaluminate type expansion Agent, 750 parts of sand, 1000 parts of crushed stone, 6.0 parts of polycarboxylate superplasticizer, 0.55 parts of TY-YQ air-entraining agent and 150 parts of water. The hollow tubular plant fiber is selected from A: sisal fiber, and the alkali-resistant filler is selected from a: styrene-acrylic emulsion.
PUM
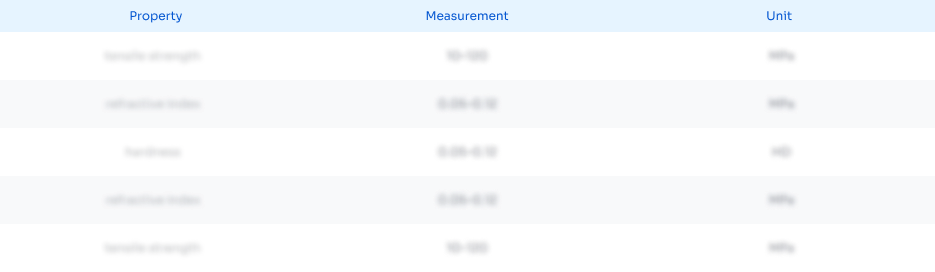
Abstract
Description
Claims
Application Information

- R&D Engineer
- R&D Manager
- IP Professional
- Industry Leading Data Capabilities
- Powerful AI technology
- Patent DNA Extraction
Browse by: Latest US Patents, China's latest patents, Technical Efficacy Thesaurus, Application Domain, Technology Topic, Popular Technical Reports.
© 2024 PatSnap. All rights reserved.Legal|Privacy policy|Modern Slavery Act Transparency Statement|Sitemap|About US| Contact US: help@patsnap.com