Method for preparing high-performance powder metallurgy Ti6Al4V alloy
A powder metallurgy, high-performance technology, applied in the field of powder metallurgy titanium, can solve the problems affecting the mechanical properties of Ti6Al4V alloy products, high content of interstitial oxygen atoms, loss of alloying elements, etc., to promote industrial development, avoid high oxygen increment, Small grain size effect
- Summary
- Abstract
- Description
- Claims
- Application Information
AI Technical Summary
Problems solved by technology
Method used
Examples
Embodiment 1
[0024] According to the mass percentage, it is composed of the following ingredients: 4.2wt.% VCl 3 , 14.9wt.% aluminum powder, the balance is TiCl 2 , where the particle size D of the aluminum powder 50 = 50 μm. Concrete preparation steps are as follows:
[0025] (1) VCl meeting the formula requirements 3 、TiCl 2 Put it into the mixing tank with aluminum powder, and mix it on the mixer for 12 hours to obtain a uniform mixed powder;
[0026] (2) heat-treating the mixed powder under vacuum at a temperature of 600° C. for a holding time of 4 hours to obtain a heat-treated product;
[0027] (3) Put the heat-treated product into a ball mill tank for high-energy ball milling, the ball-to-material ratio is 6:1, and crush for 72 hours to obtain fine Ti6Al4V alloy powder;
[0028] (4) Put the fine Ti6Al4V alloy powder in a high-purity argon-protected glove box and put it into a silica gel sheath to vibrate. After sealing, perform cold isostatic pressing. The pressing pressure is...
Embodiment 2
[0031] According to the mass percentage, it is composed of the following ingredients: 4.5wt.% VCl 3 , 15.2wt.% aluminum powder, the balance is TiCl 2 , where the particle size D of the aluminum powder 50 = 200 μm. Concrete preparation steps are as follows:
[0032] (1) VCl meeting the formula requirements 3 、TiCl 2 Put it into the mixing tank with aluminum powder, and mix it on the mixer for 10 hours to obtain a uniform mixed powder;
[0033] (2) heat-treating the mixed powder under vacuum at a temperature of 750° C. for a holding time of 3 hours to obtain a heat-treated product;
[0034] (3) Put the heat-treated product into a ball mill tank for high-energy ball milling, with a ball-to-material ratio of 10:1, and crush for 48 hours to obtain fine Ti6Al4V powder;
[0035] (4) Put the fine Ti6Al4V alloy powder in a high-purity argon-protected glove box and put it into a rubber sheath to vibrate. After sealing, perform cold isostatic pressing. The pressing pressure is 400M...
PUM
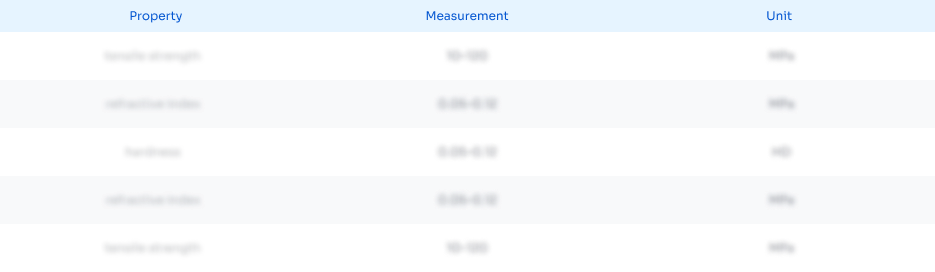
Abstract
Description
Claims
Application Information

- Generate Ideas
- Intellectual Property
- Life Sciences
- Materials
- Tech Scout
- Unparalleled Data Quality
- Higher Quality Content
- 60% Fewer Hallucinations
Browse by: Latest US Patents, China's latest patents, Technical Efficacy Thesaurus, Application Domain, Technology Topic, Popular Technical Reports.
© 2025 PatSnap. All rights reserved.Legal|Privacy policy|Modern Slavery Act Transparency Statement|Sitemap|About US| Contact US: help@patsnap.com