High-melt-index PC composite material for 3D printing and preparation method thereof
A technology of 3D printing and composite materials, which is applied in the field of high-melting index PC composite materials and its preparation, can solve the problems of difficult wire diameter control, easy warping of printed products, and easy warping of printed products, so as to reduce unqualified The risk of warping, obvious warping, and the effect of warping improvement
- Summary
- Abstract
- Description
- Claims
- Application Information
AI Technical Summary
Problems solved by technology
Method used
Image
Examples
Embodiment 1(1)
[0011] Example 1 (1) Weigh the following raw materials by weight: 80 parts of polycarbonate, 15 parts of PETG, 4 parts of compatibilizer, 0.3 part of antioxidant, and 0.5 part of lubricant. The PC material was dried in a drying oven at 120 °C for 5 h, and the PETG material was dried at 70 °C for 6 h. (2) Add the polycarbonate, PETG, compatibilizer, antioxidant, and lubricant weighed in step (1) into a high-speed mixer, and mix for 2-4 minutes. (3) Place the mixed premix in a co-rotating twin-screw extruder for melt extrusion and granulation. The temperatures of the twin-screw barrel and head are: 220°C, 235°C, 245°C, 245°C, 245°C, 240°C; put the pellets into a single-screw extruder and extrude them into 1.75mm filaments for 3D printing. °C, 240 °C, 230 °C.
[0012] The performance of the PC composite material prepared in this example is compared with that of the PC material in the following table:
[0013] Table 1 Embodiment 1 and PC material performance contrast
[0014] ...
Embodiment 2
[0017] Example 2 (1) Weigh the following raw materials by weight: 70 parts of polycarbonate, 25 parts of PETG, 5 parts of compatibilizer, 0.3 part of antioxidant, and 0.5 part of lubricant. The PC material was dried in a drying oven at 120 °C for 5 h, and the PETG material was dried at 70 °C for 6 h. (2) Add the polycarbonate, PETG, compatibilizer, antioxidant, and lubricant weighed in step (1) into a high-speed mixer, and mix for 2-4 minutes. (3) Place the mixed premix in a co-rotating twin-screw extruder for melt extrusion and granulation. The temperatures of the twin-screw barrel and head are: 220°C, 230°C, 240°C, 240°C, 245°C, 240°C; put the pellets into a single-screw extruder and extrude them into 1.75mm filaments for 3D printing. °C, 240 °C, 230 °C.
[0018] The performance of the PC composite material prepared in this example is compared with that of the PC material in the following table:
[0019]
[0020] Table 2 Performance comparison between Example 2 and PC ...
PUM
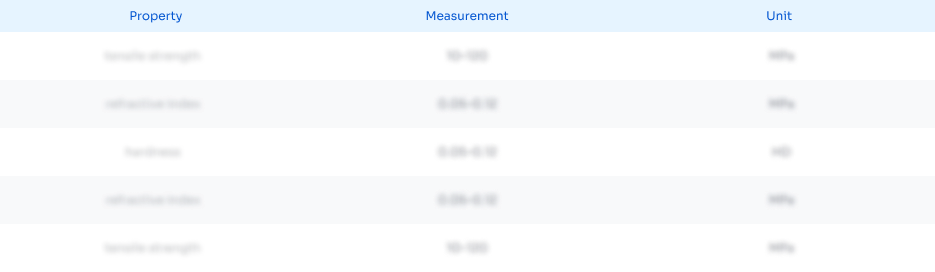
Abstract
Description
Claims
Application Information

- R&D
- Intellectual Property
- Life Sciences
- Materials
- Tech Scout
- Unparalleled Data Quality
- Higher Quality Content
- 60% Fewer Hallucinations
Browse by: Latest US Patents, China's latest patents, Technical Efficacy Thesaurus, Application Domain, Technology Topic, Popular Technical Reports.
© 2025 PatSnap. All rights reserved.Legal|Privacy policy|Modern Slavery Act Transparency Statement|Sitemap|About US| Contact US: help@patsnap.com