High-efficiency short-process preparation method of high-strength high-conductivity copper alloy
A technology of copper alloys and alloying elements, which is applied in the field of preparation of high-strength and high-conductivity copper alloys, can solve the problems of large production costs and equipment investment, copper alloy performance needs to be improved, and low yield, so as to avoid stress cracking and high-strength characteristics , the effect of shortening the process
- Summary
- Abstract
- Description
- Claims
- Application Information
AI Technical Summary
Problems solved by technology
Method used
Image
Examples
Embodiment 0
[0083] Embodiment 0: the preparation embodiment of forging high-temperature nickel-based alloy:
[0084] The alloy ingot is smelted by vacuum smelting + electroslag remelting process, the composition is: 0.05wt.%C, 15wt.%Cr, 6wt.%Mo, 5wt.%W, 2wt.%Ti, 5.5wt.%Al, the rest For you. After the alloy ingot was homogenized at 1250°C for 1h, it was formed by isothermal forging at 1000°C with a deformation of 80%. After that, it was kept at 800°C for 16 hours, quenched and tempered at 350°C for 1 hour, and the tensile properties of the alloy at room temperature to 800°C were tested. The results are shown in Table 1:
[0085] Table 1 High Temperature Mechanical Properties of Alloys
[0086] temperature / ℃ Tensile strength / MPa Yield strength / MPa Elongation / % room temperature 1200 1100 8 500 1220 1120 9 800 1280 1150 9
Embodiment 1
[0088] The first step: batching melting: according to the alloy composition of Cu-0.5wt.%Ag, batching is carried out, put into the melting furnace and fully melted, carry out sampling inspection and analysis of oxygen content and alloy element content, feed and fully deoxidize to within 10ppm according to the analysis results, The melt is introduced into the holding furnace through the inner guide groove of the melting furnace.
[0089] The second step: horizontal continuous casting: horizontal continuous casting is carried out under the side of the holding furnace, and two crystallizers with an interval of 400mm are arranged horizontally and installed under the side of the holding furnace. Group 1 cooling units are closest to the holding furnace. The reverse cooling method is adopted, and the temperature of the water inlet is lower than 20°C. The water flow V3 of the third group of cooling units is 2000L / min, the water flow V2 of the second group of cooling units is 2400L / mi...
Embodiment 2
[0096] Step 2: Horizontal continuous casting: 4 crystallizers are used with an interval of 200mm. The water flow V3 of the third cooling unit is 100L / min, and the water flow V2 of the second cooling unit is 120L / min. The water flow V1 of the unit is 150L / min, the electromagnetic stirring frequency used is 2Hz, and the cross-sectional area of the blank is 50mm 2 , the extraction speed is 100mm / min, 30 atomizing nozzles are set, the distance between the nozzles is 20mm, the distance between the nozzle and the surface of the billet is 50mm, and the water pressure is 0.5MPa.
[0097] The third step: continuous extrusion: the rotation speed of the extrusion wheel is 8 rpm, the extrusion ratio is 8, and the extrusion gap is 2 mm. Set 25 atomizing nozzles, the interval between the atomizing nozzles is 20mm, the distance between the nozzle and the surface of the billet is 50mm, and the water pressure is 0.5MPa.
[0098] The fourth step: cold working: the deformation amount of each ...
PUM
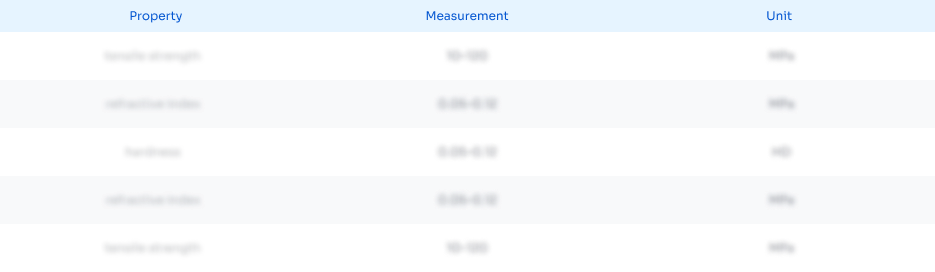
Abstract
Description
Claims
Application Information

- R&D
- Intellectual Property
- Life Sciences
- Materials
- Tech Scout
- Unparalleled Data Quality
- Higher Quality Content
- 60% Fewer Hallucinations
Browse by: Latest US Patents, China's latest patents, Technical Efficacy Thesaurus, Application Domain, Technology Topic, Popular Technical Reports.
© 2025 PatSnap. All rights reserved.Legal|Privacy policy|Modern Slavery Act Transparency Statement|Sitemap|About US| Contact US: help@patsnap.com