Phosphate anti-oxidation coating of carbon/carbon composite material and coating process thereof
A technology of carbon composite materials and phosphate, which is applied to the coating process for making the above-mentioned phosphate anti-oxidation coating, and the field of phosphate anti-oxidation coating of carbon/carbon composite materials, which can solve the problems of high raw material cost, difficult processing, Problems such as difficulty in field maintenance, etc., achieve the effect of simple preparation process and wide application range
- Summary
- Abstract
- Description
- Claims
- Application Information
AI Technical Summary
Problems solved by technology
Method used
Examples
Embodiment 1
[0033] According to weight percentage, dry, grind and mix the powder of aluminum hydroxide 25%-30%, CeO 25%-8%, then add phosphorus oxide 20%-25%, distilled water 40%-60%, and stir evenly; Heat the mixture to 100°C and keep it for 20-30 minutes to fully react to form a phosphate aqueous solution; hot-coat it on the non-friction surface of the carbon brake disc of the MA60 aircraft, and treat it at a high temperature under a controlled atmosphere of 1200°C Serve in 1.5 hours.
[0034] Performance tests were carried out on the above carbon brake discs to test the performance of the phosphate anti-oxidation coating, as follows:
[0035] ① Static heating simulation test.
[0036] Equipment: Thermogravimetric Analyzer (STA409DG / DG);
[0037] Test conditions: placed at 700°C for 50 hours;
[0038] Test results: The oxidation weight loss rate is only 1.96%.
[0039] ② Thermal shock test.
[0040] Equipment: double-tube high-temperature carbon-fixing furnace (SK-2.5-14S);
[004...
Embodiment 2
[0048] By weight percentage, Al 2 o 330%-35% and Pr3%-6% powder are dried, ground and mixed, then add phosphoric acid 25%-30% and distilled water 45%-50% and stir evenly; heat the mixture to 100°C and keep for 30 - 40 minutes, fully reacted to form a phosphate aqueous solution; hot-coated on the non-friction surface of a certain type of aircraft carbon brake disc, and treated at a high temperature of 900 ° C for 4 hours under a controlled atmosphere.
[0049] Performance tests were carried out on the above carbon brake discs to test the performance of the phosphate anti-oxidation coating, as follows:
[0050] ① Static heating simulation test.
[0051] Equipment: Thermogravimetric Analyzer (STA409DG / DG);
[0052] Test conditions: placed at 800°C for 30 hours;
[0053] Test results: The oxidation weight loss rate is only 2.78%.
[0054] ② Ground bench test.
PUM
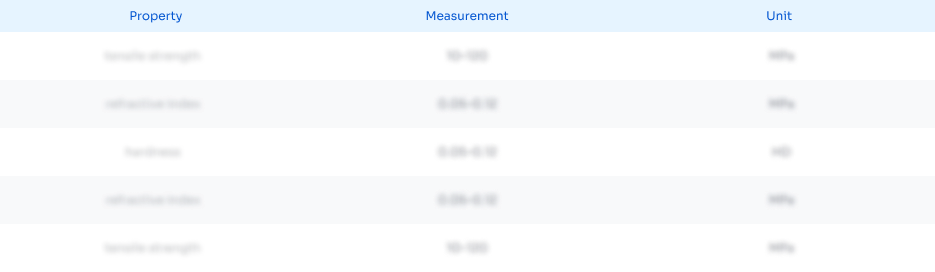
Abstract
Description
Claims
Application Information

- R&D
- Intellectual Property
- Life Sciences
- Materials
- Tech Scout
- Unparalleled Data Quality
- Higher Quality Content
- 60% Fewer Hallucinations
Browse by: Latest US Patents, China's latest patents, Technical Efficacy Thesaurus, Application Domain, Technology Topic, Popular Technical Reports.
© 2025 PatSnap. All rights reserved.Legal|Privacy policy|Modern Slavery Act Transparency Statement|Sitemap|About US| Contact US: help@patsnap.com