A kind of high fluidity nylon toughening agent and preparation method thereof
A high-fluidity, toughening agent technology, applied in the field of polymer materials, can solve the problem that the impact of toughening agents on the processing fluidity of nylon materials cannot be reduced, so as to reduce the impact, improve the toughening effect, and improve the gap The effect of impact strength
- Summary
- Abstract
- Description
- Claims
- Application Information
AI Technical Summary
Problems solved by technology
Method used
Image
Examples
Embodiment 1
[0030] Take the following raw materials according to parts by weight: the propylene-based elastomer is a propylene-ethylene copolymer with a propylene content of 84%, 90 parts; the vinyl elastomer (Dow's POE, 8150), 10 parts; the first graft monomer is Maleic anhydride, 2 parts; the second grafting monomer is styrene, 1 part; the initiator is dicumyl peroxide, 0.1 part; the diluent is acetone, 1 part.
[0031] Mix the above raw materials in a low-speed mixer for 20 minutes, and then add them to the twin-screw extruder. The temperature of the extruder zone 1 to zone 14 is set to 80°C, 160°C, 180°C, 190°C, 195°C, 195°C, 195°C , 195°C, 195°C, 190°C, 190°C, 180°C, 180°C, 180°C, the machine head is 190°C. The mixed material is melted and plasticized, kneaded and kneaded, extruded by a machine head, pelletized in a water ring, cooled, dehydrated, and blast-dried to obtain the product.
Embodiment 2
[0033]Take the following raw materials according to parts by weight: propylene-based elastomer is a propylene-ethylene copolymer with a propylene content of 92%, 70 parts; vinyl elastomer (Dow EPDM, 3745P), 30 parts; the first graft monomer is Maleic anhydride, 2 parts; The second grafting monomer is caprolactam, 1 part; Initiator is made up of dibenzoyl peroxide and dicumyl peroxide in a mass ratio of 1:2, 0.15 part; Thinner is Butanone, 1.5 parts.
[0034] Blend the above raw materials in a low-speed mixer for 20 minutes, then add them to the twin-screw extruder, and set the temperature from zone 1 to zone 14 of the extruder to 80°C, 160°C, 180°C, 190°C, 195°C, 195°C, 195°C , 195°C, 195°C, 190°C, 190°C, 180°C, 180°C, 180°C, the machine head is 190°C. The mixed material is melted and plasticized, kneaded and kneaded, extruded by a machine head, pelletized in a water ring, cooled, dehydrated, and blast-dried to obtain the product.
Embodiment 3
[0036] Take by weight the following raw materials: propylene-based elastomer is a propylene-octene copolymer with a propylene content of 88%, 60 parts; vinyl elastomer (Arkema EMA, 28MA07), 40 parts; the first grafting unit The body is glycidyl methacrylate, 5 parts; the second grafting monomer is styrene, 2.5 parts; the initiator is 2,5-dimethyl-2,5-bis(tert-butyl peroxy)hexane , 0.4 parts; the diluent is ethanol, 2 parts.
[0037] Blend the above raw materials in a low-speed mixer for 20 minutes, then add them to the twin-screw extruder, and set the temperature from zone 1 to zone 14 of the extruder to 80°C, 160°C, 180°C, 190°C, 195°C, 195°C, 195°C , 195°C, 195°C, 190°C, 190°C, 180°C, 180°C, 180°C, the machine head is 190°C. The mixed material is melted and plasticized, kneaded and kneaded, extruded by a machine head, pelletized in a water ring, cooled, dehydrated, and blast-dried to obtain the product.
PUM
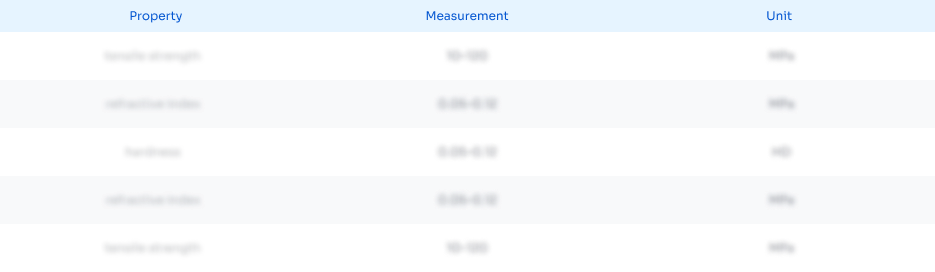
Abstract
Description
Claims
Application Information

- R&D
- Intellectual Property
- Life Sciences
- Materials
- Tech Scout
- Unparalleled Data Quality
- Higher Quality Content
- 60% Fewer Hallucinations
Browse by: Latest US Patents, China's latest patents, Technical Efficacy Thesaurus, Application Domain, Technology Topic, Popular Technical Reports.
© 2025 PatSnap. All rights reserved.Legal|Privacy policy|Modern Slavery Act Transparency Statement|Sitemap|About US| Contact US: help@patsnap.com