A method for selectively reclaiming lithium and copper in waste lithium iron phosphate batteries
A lithium iron phosphate battery, a selective technology, applied in the direction of battery recycling, recycling technology, waste collector recycling, etc., can solve problems such as complex procedures, high recycling costs, and large consumption of acid-base reagents, and achieve a short process flow , low cost of reagents, and high-efficiency leaching effect
- Summary
- Abstract
- Description
- Claims
- Application Information
AI Technical Summary
Problems solved by technology
Method used
Image
Examples
Embodiment 1
[0046]100g of a waste lithium iron phosphate electrode material is added to a sulfuric acid solution with a concentration of 0.02mol / L. The amount of sulfuric acid solution added is 0.9 according to the ratio of the moles of hydrogen ions in the sulfuric acid solution to the moles of lithium and copper in the waste lithium iron phosphate electrode material. : 1 was added; feeding oxygen to control the oxygen partial pressure was 1.9Mpa, the reaction temperature was 150°C, and the reaction time was 5 hours; after the reaction was finished, it was filtered to obtain the leaching solution and ferric phosphate leaching residue respectively; the lithium leaching rate was calculated to be 98.2%, The leaching rate of copper is 99.1%, and the leaching rate of iron is 0.05%. Iron powder is added to the leaching solution to separate the copper in the leaching solution. After oxidation, sodium carbonate is added to adjust the pH to 6.5 to separate iron and aluminum impurities to obtain a p...
Embodiment 2
[0048] Add 100 g of a waste lithium iron phosphate electrode material to a sulfuric acid solution with a concentration of 4 mol / L. The amount of sulfuric acid solution added is 1.2 according to the ratio of the number of moles of hydrogen ions in the sulfuric acid solution to the number of moles of lithium and copper in the waste lithium iron phosphate electrode material: 1 added; feed oxygen to control the oxygen partial pressure to 0.3Mpa, the reaction temperature to 96°C, and the reaction time to 0.5 hours; filter after the reaction to obtain the leaching solution and ferric phosphate leaching residue respectively; the calculated lithium leaching rate is 99.3%, copper The leaching rate is 99.6%, and the iron leaching rate is 4.6%. Add sodium sulfide to the leaching solution to separate the copper in the leaching solution, add sodium bicarbonate to adjust the pH to 5.5 to separate iron and aluminum impurities, and obtain a purification solution; then add to the purification so...
Embodiment 3
[0050] Add 100 g of a waste lithium iron phosphate electrode material to a hydrochloric acid solution with a concentration of 1 mol / L. The amount of hydrochloric acid solution added is 1.1 according to the ratio of the moles of hydrogen ions in the hydrochloric acid solution to the moles of lithium and copper in the waste lithium iron phosphate electrode material: 1 was added; the oxygen partial pressure was controlled to be 1.3Mpa by feeding oxygen, the reaction temperature was 120°C, and the reaction time was 3.0 hours; after the reaction was completed, it was filtered to obtain the leaching solution and ferric phosphate leaching residue; the calculated lithium leaching rate was 99.7%, copper The leaching rate is 99.8%, and the leaching rate of iron is 0.09%. Add sodium sulfide to the leaching solution to separate the copper in the leaching solution, add sodium hydroxide to adjust the pH to 6.0 to separate iron and aluminum impurities, and obtain a purification solution; then ...
PUM
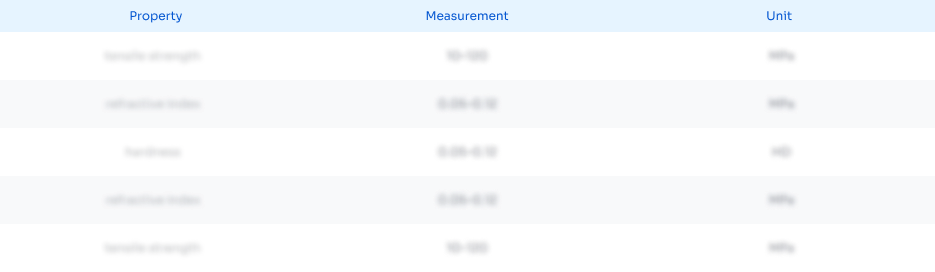
Abstract
Description
Claims
Application Information

- Generate Ideas
- Intellectual Property
- Life Sciences
- Materials
- Tech Scout
- Unparalleled Data Quality
- Higher Quality Content
- 60% Fewer Hallucinations
Browse by: Latest US Patents, China's latest patents, Technical Efficacy Thesaurus, Application Domain, Technology Topic, Popular Technical Reports.
© 2025 PatSnap. All rights reserved.Legal|Privacy policy|Modern Slavery Act Transparency Statement|Sitemap|About US| Contact US: help@patsnap.com