Preparation method of carbon/silicon hybrid fiber and carbon/silicon hybrid fiber
A technology of silicon hybridization and fiber, which is applied in the field of fiber, can solve the problems of poor mechanical strength and incompressibility, and achieve the effect of low density, high modulus and good conductivity
- Summary
- Abstract
- Description
- Claims
- Application Information
AI Technical Summary
Problems solved by technology
Method used
Image
Examples
Embodiment 1
[0032] Mix 10g of 1,4-bis(trimethoxysilyl)benzene, 856g of methyltrimethoxysilane, 4500ml of DMF and 600ml of deionized water, add 1mol / L dilute hydrochloric acid to adjust the pH to 2.5 for hydrolysis, then add ammonia water to adjust the pH to 9.5 Condensation was carried out to obtain a gel, which was aged at 40° C. for 45 hours, soaked in DMF for 20 hours twice, and taken out to obtain a wet gel.
[0033] Take 10g of wet gel and pulverize it into a mesh of no more than 2000, add it to 8g of polyacrylonitrile DMF solution with a concentration of 10wt%, mix well, and use the electrospinning process to obtain the raw silk. , 220°C, 235°C, 250°C, 270°C, and 300°C for 8 minutes, respectively, and then carbonized at 1000°C for 160 seconds under a nitrogen atmosphere to obtain a silicon / carbon hybrid fiber 1.
Embodiment 2
[0035] Mix 10g of 1,4-bis(triethoxysilyl)benzene, 520g of ethyl orthosilicate, 2800ml of DMF and 400ml of deionized water, add 1mol / L dilute hydrochloric acid to adjust the pH to 2.5 for hydrolysis, then add sodium carbonate to adjust the pH to 9.0 was condensed to obtain a gel, which was aged at 50°C for 30 hours, then soaked in DMF for 20 hours twice, and taken out to obtain a wet gel.
[0036] Take 10g of wet gel and crush it into a mesh of no more than 2000, add it to 20g of polyacrylonitrile DMF solution with a concentration of 6wt%, mix well, and use wet spinning process to obtain raw silk, which is pre-oxidized at 205°C in air atmosphere 9 minutes, 9 minutes of pre-oxidation at 220°C, 8 minutes of pre-oxidation at 250°C, 8 minutes of pre-oxidation at 280°C, and 5 minutes of pre-oxidation at 320°C, and then stay at 1200°C for 120 seconds and 2000°C for 20 seconds under nitrogen atmosphere. A silicon / carbon hybrid fiber 2 was obtained.
Embodiment 3
[0038] Mix 10g of 1,4-bis(trimethoxysilylethyl)benzene, 41g of methyltrimethoxysilane, 41g of ethyl orthosilicate, 480ml of DMF and 200ml of deionized water, add 1mol / L oxalic acid solution to adjust the pH to 2.5 Hydrolyze, then add ammonia water to adjust the pH to 9.0 and condense to obtain a gel. The gel is aged at 40°C for 45 hours, then soaked in DMF for 20 hours twice, and taken out to obtain a wet gel.
[0039] Take 10g of wet gel and crush it into a mesh of no more than 2000, add it to 40g of polyacrylonitrile DMF solution with a concentration of 14wt%, mix well, and use wet spinning process to obtain raw silk, which is pre-oxidized at 205°C in air atmosphere 9 minutes, pre-oxidation at 220°C for 9 minutes, pre-oxidation at 250°C for 8 minutes, pre-oxidation at 280°C for 8 minutes, and pre-oxidation at 320°C for 5 minutes, and then stay at 1500°C for 120 seconds in a nitrogen atmosphere to obtain silicon / carbon hybrid fibers 3.
PUM
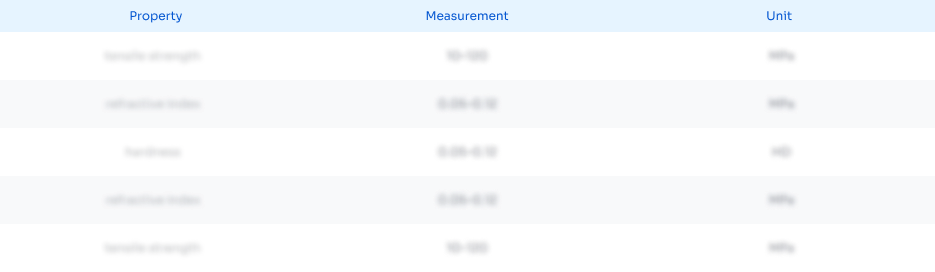
Abstract
Description
Claims
Application Information

- R&D
- Intellectual Property
- Life Sciences
- Materials
- Tech Scout
- Unparalleled Data Quality
- Higher Quality Content
- 60% Fewer Hallucinations
Browse by: Latest US Patents, China's latest patents, Technical Efficacy Thesaurus, Application Domain, Technology Topic, Popular Technical Reports.
© 2025 PatSnap. All rights reserved.Legal|Privacy policy|Modern Slavery Act Transparency Statement|Sitemap|About US| Contact US: help@patsnap.com